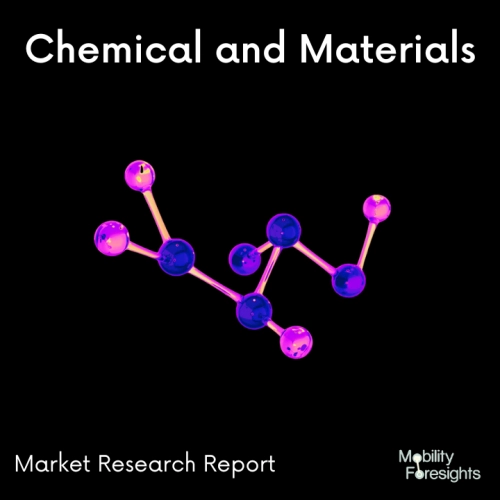
- Get in Touch with Us
Last Updated: Apr 26, 2025 | Study Period: 2022-2030
The ability of a 3D printed capsule co-formulated with the permeation enhancer sodium caprate to transport the synthetic octapeptide octreotide in beagle dogs was assessed.
The capsule is made to break free from the physiological pressures in the antropyloric area. Traditional enteric coated hard gelatin capsules and enteric coated tablets were contrasted with the pressure sensitive capsules.
Using a bottom-up assembly method, 3D biological structures are created by depositing biomaterials or biomaterials combined with cells in predefined patterns layer by layer.
Replicating the structure, makeup, and complexity of human tissues is now possible thanks to technology, which could ultimately result in the development of whole organ engineering for medical applications.
The Global 3D bioprinted capsules market accounted for $XX Billion in 2021 and is anticipated to reach $XX Billion by 2030, registering a CAGR of XX% from 2022 to 2030.
The multinational pharmaceutical giant Merck has made plans to collaborate with AMCM, an EOS Group company that creates specialised additive manufacturing equipment.
The two businesses will collaborate on designing and manufacturing 3D printed tablets, initially for use in clinical trials and subsequently for mass production.
"Our relationship with AMCM / EOS has the potential to change the way tablets are made," said Merck's Chief Strategy Officer. The sector will undergo a significant shift toward digitization.
The purpose of powder bed fusion, in which powder is melted and fused together layer by layer by a laser, is to create pharmaceuticals. AM is anticipated to speed up and reduce the cost of tablet manufacturing by enabling the avoidance of reformulations during pharmaceutical development and commercial production. Additionally, 3D printing offers the flexibility to adjust to patient needs.
Sl no | Topic |
1 | Market Segmentation |
2 | Scope of the report |
3 | Abbreviations |
4 | Research Methodology |
5 | Executive Summary |
6 | Introduction |
7 | Insights from Industry stakeholders |
8 | Cost breakdown of Product by sub-components and average profit margin |
9 | Disruptive innovation in the Industry |
10 | Technology trends in the Industry |
11 | Consumer trends in the industry |
12 | Recent Production Milestones |
13 | Component Manufacturing in US, EU and China |
14 | COVID-19 impact on overall market |
15 | COVID-19 impact on Production of components |
16 | COVID-19 impact on Point of sale |
17 | Market Segmentation, Dynamics and Forecast by Geography, 2022-2030 |
18 | Market Segmentation, Dynamics and Forecast by Product Type, 2022-2030 |
19 | Market Segmentation, Dynamics and Forecast by Application, 2022-2030 |
20 | Market Segmentation, Dynamics and Forecast by End use, 2022-2030 |
21 | Product installation rate by OEM, 2022 |
22 | Incline/Decline in Average B-2-B selling price in past 5 years |
23 | Competition from substitute products |
24 | Gross margin and average profitability of suppliers |
25 | New product development in past 12 months |
26 | M&A in past 12 months |
27 | Growth strategy of leading players |
28 | Market share of vendors, 2022 |
29 | Company Profiles |
30 | Unmet needs and opportunity for new suppliers |
31 | Conclusion |
32 | Appendix |