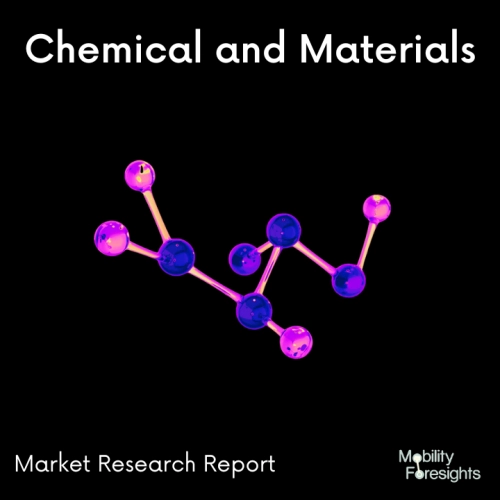
- Get in Touch with Us
Last Updated: Apr 25, 2025 | Study Period: 2024-2030
The martensite structure and strength-inducing nanoparticles of the 3D-printed steel were demonstrated through mechanical tests to be equivalent to those of traditionally manufactured steel.
Selective laser melting is used for steel 3D printing (SLM). In the case of martensitic steel, this method melts layers of powder measuring 40 microns (1.2709).Martensitic steel and L-40 parts may need to undergo heat treatment to increase their hardness after they are created, depending on their intended usage.
One of the stainless steel grades that corresponds to a specific crystalline microstructure is martensitic stainless steel. The tetragonal structure of the steel makes it possible to harden and temper it using a range of temperature profiles, making it very valuable in industry.Manufacturers might be able to eliminate the need for specialised tools, expensive production expenses, and additional time using 3D printing.
The Global 3D Printed Martensite Stainless Steel market accounted for $XX Billion in 2023 and is anticipated to reach $XX Billion by 2030, registering a CAGR of XX% from 2024 to 2030.
3D-printed martensitic steel, A method based on 3D printing for using martensitic steels to create intricate structures and a variety of shapes Texas A&M University and the U.S. Air Force Research Laboratory collaborated to create the martensite steel powder used in 3D printing.
Using selective laser melting technology to deposit and stack layers, this high strength, low cost type of steel may now be manufactured. It is made by rapidly cooling the austenite form of iron. The highest documented tensile strength for a 3D printed alloy to date was found in the samples produced by the researchers, which also had up to 11% elongation.
Modelling studies were carried out to estimate how a single layer of martensitic steel powder would melt under various laser speed and power settings in order to prevent the introduction of defects, manifest in the form of pores, into the material.
Then, by comparing the types and quantities of observed and predicted defects in a single track of melted powder, process guidelines were developed.
The use of robust, ductile martensitic steels in automotive, aerospace, and defence applications could be increased using additive manufacturing. It is simple to modify the method originally created for this kind of steel for usage with other metals and alloys.
Sl no | Topic |
1 | Market Segmentation |
2 | Scope of the report |
3 | Abbreviations |
4 | Research Methodology |
5 | Executive Summary |
6 | Introduction |
7 | Insights from Industry stakeholders |
8 | Cost breakdown of Product by sub-components and average profit margin |
9 | Disruptive innovation in the Industry |
10 | Technology trends in the Industry |
11 | Consumer trends in the industry |
12 | Recent Production Milestones |
13 | Component Manufacturing in US, EU and China |
14 | COVID-19 impact on overall market |
15 | COVID-19 impact on Production of components |
16 | COVID-19 impact on Point of sale |
17 | Market Segmentation, Dynamics and Forecast by Geography, 2024-2030 |
18 | Market Segmentation, Dynamics and Forecast by Product Type, 2024-2030 |
19 | Market Segmentation, Dynamics and Forecast by Application, 2024-2030 |
20 | Market Segmentation, Dynamics and Forecast by End use, 2024-2030 |
21 | Product installation rate by OEM, 2023 |
22 | Incline/Decline in Average B-2-B selling price in past 5 years |
23 | Competition from substitute products |
24 | Gross margin and average profitability of suppliers |
25 | New product development in past 12 months |
26 | M&A in past 12 months |
27 | Growth strategy of leading players |
28 | Market share of vendors, 2023 |
29 | Company Profiles |
30 | Unmet needs and opportunity for new suppliers |
31 | Conclusion |
32 | Appendix |