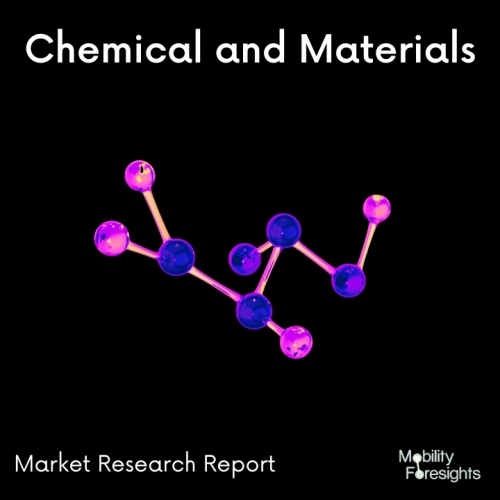
- Get in Touch with Us
Last Updated: Apr 25, 2025 | Study Period: 2023-2030
While emitting less carbon, the superalloy created using 3D printing can produce more energy. The alloy's intricate structure enabled it to have a high hardness that was immune to temperature up to 800 °C.
The researchers developed the 3D-printed superalloy, which is stronger and lighter than the most recent cutting-edge materials used in gas turbine equipment thanks to an unusual composition.
The results raise the possibility of a new class of related alloys that have not yet been identified, which could have significant ramifications for the energy, aerospace, and automotive sectors.
The Global 3D-Printed Superalloy market accounted for $XX Billion in 2022 and is anticipated to reach $XX Billion by 2030, registering a CAGR of XX% from 2023 to 2030.
New 3D printed superalloy was developed by Sandia experts. The high-performance metal alloy is more durable and lightweight than the components used in gas turbine equipment right now.
In comparison to other high-performance alloys, the new superalloy can endure higher temperatures thanks to its composition of 42% aluminium, 25% titanium, 13% niobium, 8% zirconium, 8% molybdenum, and 4% tantalum. More energy can be converted into electricity as a consequence, and less waste heat is discharged into the environment.
The researchers rapidly melted together powdered metals and printed a sample of the mixture using a Laser Engineered Net Shaping (LENS) 3D printer, demonstrating how the technology can be applied as a quick and effective way to create new materials.It demonstrate that this material can access previously unattainable combos of high strength, low weight, and high-temperature resiliency.
The researchers are now interested in investigating whether computer modelling methods could aid in the discovery of additional members of what may turn out to be a new class of high-performance superalloys. All of these metals interact with one another at the microscopic, even atomic, level, and it is these interactions that actually decide a metal's strength, malleability, melting point, and other properties.
Because their model can compute all of that and allow us to forecast a new material's performance prior to fabrication, it significantly reduces the amount of guesswork in metallurgy.
Sl no | Topic |
1 | Market Segmentation |
2 | Scope of the report |
3 | Abbreviations |
4 | Research Methodology |
5 | Executive Summary |
6 | Introduction |
7 | Insights from Industry stakeholders |
8 | Cost breakdown of Product by sub-components and average profit margin |
9 | Disruptive innovation in the Industry |
10 | Technology trends in the Industry |
11 | Consumer trends in the industry |
12 | Recent Production Milestones |
13 | Component Manufacturing in US, EU and China |
14 | COVID-19 impact on overall market |
15 | COVID-19 impact on Production of components |
16 | COVID-19 impact on Point of sale |
17 | Market Segmentation, Dynamics and Forecast by Geography, 2023-2030 |
18 | Market Segmentation, Dynamics and Forecast by Product Type, 2023-2030 |
19 | Market Segmentation, Dynamics and Forecast by Application, 2023-2030 |
20 | Market Segmentation, Dynamics and Forecast by End use, 2023-2030 |
21 | Product installation rate by OEM, 2023 |
22 | Incline/Decline in Average B-2-B selling price in past 5 years |
23 | Competition from substitute products |
24 | Gross margin and average profitability of suppliers |
25 | New product development in past 12 months |
26 | M&A in past 12 months |
27 | Growth strategy of leading players |
28 | Market share of vendors, 2023 |
29 | Company Profiles |
30 | Unmet needs and opportunity for new suppliers |
31 | Conclusion |
32 | Appendix |