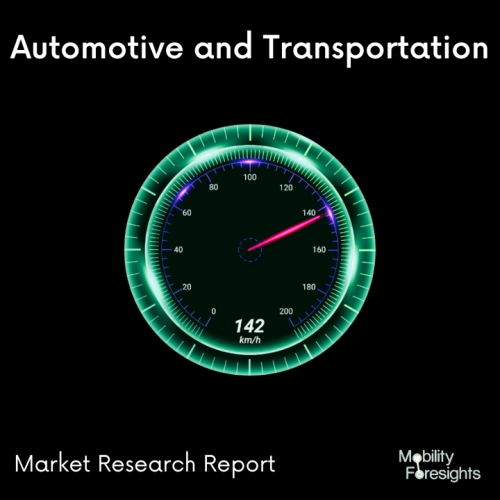
- Get in Touch with Us
Last Updated: Apr 25, 2025 | Study Period: 2024-2030
Continuous advancements in power electronics, battery technologies, and associated components are enhancing the overall efficiency, reliability, and cost-effectiveness of 800V systems. This ongoing technological evolution is instrumental in driving innovation and fostering market expansion.
Consumer preferences are shifting towards high-performance electric vehicles, driving the demand for advanced solutions. The 800V technology stands out by providing faster charging capabilities, increased power output, and enhanced efficiency, aligning with consumer expectations and attracting a broader customer base.
The contemporary electric cars have load power voltages of 400 V, resulting in load currents around a few hundred amps. When transporting such currents, big and heavy electric components, such as relays and fuses, are necessary, which are difficult to compact in a battery pack.
As a result, car manufacturers are presently planning to use voltage levels of up to 800 V in commercial applications in order to minimize power dissipation and control energy loss while employing multiple components.
Automobile manufacturers develop their wiring architecture of the system for increased (charging) power using 800-volt technology. Higher currents (mainly for quick charging, as well as for higher powerful drives) necessitate larger connections or better cooling since more heat is created.
This adds to the vehicle's mass and sophistication. Since for federal mandates to minimize CO2 and NOx emissions, along with limited fossil fuel supplies, the automobile of the long term will be electrically, battery, or hybrid driven.
This entails rewriting the conventional idea of an automobile, which carries with it a slew of new problems, innovations, and adjustments. Sports concepts using 400-volt technology may also offer the maximum allowable recovery power of 300 kilowatts, as specified in endurance standards.
Their on-board infrastructure, nevertheless, necessitates wire widths that are twice as heavy, culminating in an additional weight of around 30 kilos. Inside the end, total efficiency is what matters. With less weight and fewer refueling stops, the dominating 800-volt bolides extended their advantage even farther.
The gGlobal 800 V EV Components Market size was valued at USD xx billion in 2023 and is projected to reach USD xx billion by 2030, growing at a CAGR of xx% during the forecast period.
Development of next-generation power electronics, including wide bandgap semiconductors like Gallium Nitride (GaN), will lead to smaller, lighter, and more efficient 800V components. This will enhance performance, reduce costs, and further drive market adoption.
Improvements in battery chemistry, cell design, and thermal management will lead to denser batteries with longer lifespans and faster charging capabilities, further improving the performance and appeal of 800V EVs.
Integrated onboard charging systems and bi-directional charging capabilities will be increasingly adopted, allowing EVs to not only receive but also feed power back into the grid, contributing to grid stability and energy efficiency.
SiC devices offer superior efficiency and thermal performance compared to traditional silicon-based components, making them ideal for 800V systems.
Onboard charging systems and bi-directional charging capabilities are gaining traction, offering greater flexibility and convenience for EV users.
Development of charging systems capable of delivering even faster charging speeds, potentially reaching 350 kW or higher. Solid-state battery technology offers increased energy density, faster charging times, and improved safety, presenting significant potential for 800V EV applications.
Governments worldwide are playing a crucial role in driving the adoption of electric vehicles (EVs) and promoting the development of 800V EV technologies. They are implementing various regulatory measures and incentive programs to achieve this goal.
Infineon Technologies' OptiMOS⢠5 High-Voltage MOSFET Series is a major development in the 800V EV component market. This series boasts significant advancements and promises to revolutionize the design and performance of 800V inverters, leading to more efficient and powerful electric vehicles.
Continental AG's unveiling of the CU800SiC++ inverter marks a significant milestone in the advancement of electric vehicle technology. This next-generation inverter utilizes silicon carbide (SiC) technology to deliver even higher power density and efficiency, paving the way for more powerful and efficient electric vehicles.
ABB's latest innovation, the Terra 800V+ DC-DC converter, marks a significant advancement in charging infrastructure for electric vehicles. This cutting-edge technology promises faster charging times and improved performance, accelerating the transition towards a more sustainable transportation future.
Denso Corporation's release of the DCDC800L, a compact and lightweight 800V DC-DC converter, addresses a critical challenge in the 800V EV component market: space constraints. This innovative product offers several advantages for manufacturers and designers of various electric vehicles and applications
Sl no | Topic |
1 | Market Segmentation |
2 | Scope of the report |
3 | Research Methodology |
4 | Executive Summary |
5 | Average B2b Price, By Region |
6 | Potential Opportunities For Client |
7 | Introduction |
8 | Latest & Upcoming 800 V Ev Components to the Market |
9 | Discussion on the role of solid-state batteries and their potential impact on the 800V EV landscape. |
10 | Analysis of power electronics, including the power inverter responsible for converting DC power from the battery to AC power |
11 | Detailed exploration of the system architecture, emphasizing the role and integration of components |
12 | Analysis of wireless charging technologies and their adoption. |
13 | New product development in past 12 months |
14 | Market Size, Dynamics and Forecast by Type, 2024-2030 |
15 | Market Size, Dynamics and Forecast by Voltage Rating, 2024-2030 |
16 | Market Size, Dynamics and Forecast by Cooling Technology, 2024-2030 |
17 | Market Size, Dynamics and Forecast by Geography Type, 2024-2030 |
18 | Competitive Landscape |
19 | Gross margin and average profitability of suppliers |
20 | M&A in past 12 months |
21 | Growth strategy of leading players |
22 | Market share of vendors, 2023 |
23 | Company Profiles |
24 | Unmet needs and opportunity for new suppliers |
25 | Conclusion |