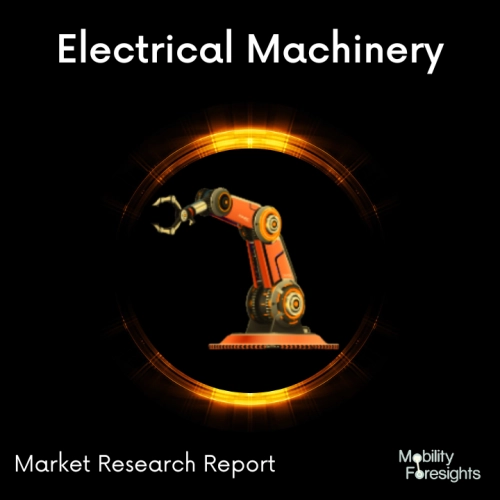
- Get in Touch with Us
Last Updated: Apr 25, 2025 | Study Period: 2023-2030
The mechanical removal method known as abrasive flow machining (AFM). The technique is used to provide high-quality surface finishes on internal and exterior contours, for targeted precision edge rounding and deburring, or for the accurate deburring of intersections.
The typical components of an abrasive flow machine are a fixture for holding the workpiece, two medium chambers with hydraulic rams, and a clamping system to hold everything together securely.
The majority of machines feature the ability to change the pressure at which the abrasive medium is extruded through the workpiece as well as the ability to load several types of abrasive media.
The Global Abrasive flow machining centre market accounted for $XX Billion in 2022 and is anticipated to reach $XX Billion by 2030, registering a CAGR of XX% from 2023 to 2030.
Using abrasive flow machining (AFM) technology, the items' surface quality can be effectively upgraded. The nozzle is chosen as the study object, and the self-designed polishing liquid is used to conduct research on the major technological parameters of abrasive flow machining linear tube in order to analyse the mechanism and technology of abrasive flow machining nonlinear tubes.
A nozzle surface topography and scanning electron microscopy (SEM) map are used to examine the effects of technological parameters on the surface quality of the parts.
The effectiveness of abrasive flow machining in improving the surface quality of a nonlinear runner has been demonstrated through experimentation, and the findings from this research can be used as a technical guide for further research into the theory behind this process.
Based on this technology, several academics have carried out a great deal of study. About abrasive flow machining technology, several academics have produced research studies.
Researchers studied how abrasive flow processing works using BP neural networks, and they conducted experimental studies on the pace at which material is removed from surfaces and their roughness.
They also adjusted the processing parameters. In order to simulate the abrasive carrier and changes in the processing medium's stickiness that affect the amount of material removed from the workpiece and its surface roughness, finite element simulation is used throughout the process.
It is determined that the primary wear mechanism for material in abrasive flow processing is being struck off by abrasives, and that the goal of fine processing is subsequently achieved.
Sl no | Topic |
1 | Market Segmentation |
2 | Scope of the report |
3 | Abbreviations |
4 | Research Methodology |
5 | Executive Summary |
6 | Introduction |
7 | Insights from Industry stakeholders |
8 | Cost breakdown of Product by sub-components and average profit margin |
9 | Disruptive innovation in the Industry |
10 | Technology trends in the Industry |
11 | Consumer trends in the industry |
12 | Recent Production Milestones |
13 | Component Manufacturing in US, EU and China |
14 | COVID-19 impact on overall market |
15 | COVID-19 impact on Production of components |
16 | COVID-19 impact on Point of sale |
17 | Market Segmentation, Dynamics and Forecast by Geography, 2023-2030 |
18 | Market Segmentation, Dynamics and Forecast by Product Type, 2023-2030 |
19 | Market Segmentation, Dynamics and Forecast by Application, 2023-2030 |
20 | Market Segmentation, Dynamics and Forecast by End use, 2023-2030 |
21 | Product installation rate by OEM, 2023 |
22 | Incline/Decline in Average B-2-B selling price in past 5 years |
23 | Competition from substitute products |
24 | Gross margin and average profitability of suppliers |
25 | New product development in past 12 months |
26 | M&A in past 12 months |
27 | Growth strategy of leading players |
28 | Market share of vendors, 2023 |
29 | Company Profiles |
30 | Unmet needs and opportunity for new suppliers |
31 | Conclusion |
32 | Appendix |