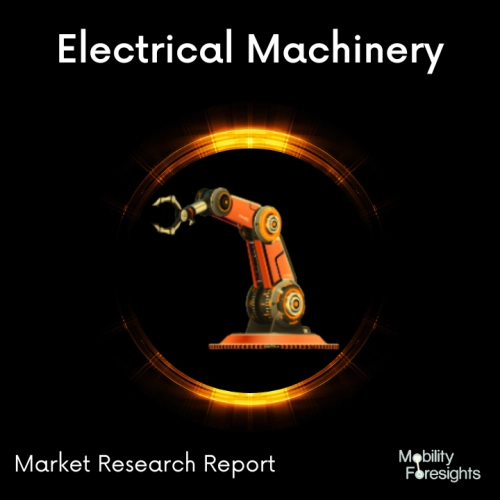
- Get in Touch with Us
Last Updated: Apr 25, 2025 | Study Period: 2024-2030
The multi-variable Inverter Adaptive Control from WeldComputer for resistance welders can enhance quality and repeatability. It offers a dependable and strong solution for guaranteeing the integrity of each weld and is capable of significantly enhancing the uniformity and throughput of any resistance welding control.
Any type of transformer for resistance welding can be interfaced with by this adaptable control. (single phase, three phase, frequency converter or MFDC).
The Global AC Inverter Resistance Spot Welding machine market accounted for $XX Billion in 2022 and is anticipated to reach $XX Billion by 2030, registering a CAGR of XX% from 2024 to 2030.
The i4 Inverter Resistance Spot Welder was developed to work with challenging materials to weld, like boron steels and Advanced High Strength Steels. (AHSS). Rapidly, automobile manufacturers are switching to these new metals as their preferred material.
A bespoke weld programme with comprehensive repair graphics is included in the i4's OEM programmable function. In order to face every welding challenge with the greatest ease and accuracy possible, the i4 comes equipped with a variety of weld arm extensions (508mm U-Arm, C-Arm, and Wheelhouse Arm), and other types are available upon request.
The i4 has a simple, ergonomic interface structure, with the power button and electrode pressure knobs placed in an easy-to-use location. It also contains a sizable 4x6" monitor with the ability to show photos and OEM repair instructions. Both water and air cooling are used to cool the i4.
The air conditioning kicks on when the temperature reaches 42°C and turns off automatically at 37°C. Even with air cooling running, welding can continue.
The spot gun and transformer weld cables are cooled using a loop-based water cooling system. Welder operations can continue as usual while the water cooling system is working.
The two cooling systems were chosen because Pro Spot determined they were the most effective and would allow the welder to operate for longer periods of time.
Sl no | Topic |
1 | Market Segmentation |
2 | Scope of the report |
3 | Abbreviations |
4 | Research Methodology |
5 | Executive Summary |
6 | Introduction |
7 | Insights from Industry stakeholders |
8 | Cost breakdown of Product by sub-components and average profit margin |
9 | Disruptive innovation in the Industry |
10 | Technology trends in the Industry |
11 | Consumer trends in the industry |
12 | Recent Production Milestones |
13 | Component Manufacturing in US, EU and China |
14 | COVID-19 impact on overall market |
15 | COVID-19 impact on Production of components |
16 | COVID-19 impact on Point of sale |
17 | Market Segmentation, Dynamics and Forecast by Geography, 2023-2030 |
18 | Market Segmentation, Dynamics and Forecast by Product Type, 2023-2030 |
19 | Market Segmentation, Dynamics and Forecast by Application, 2023-2030 |
20 | Market Segmentation, Dynamics and Forecast by End use, 2023-2030 |
21 | Product installation rate by OEM, 2023 |
22 | Incline/Decline in Average B-2-B selling price in past 5 years |
23 | Competition from substitute products |
24 | Gross margin and average profitability of suppliers |
25 | New product development in past 12 months |
26 | M&A in past 12 months |
27 | Growth strategy of leading players |
28 | Market share of vendors, 2023 |
29 | Company Profiles |
30 | Unmet needs and opportunity for new suppliers |
31 | Conclusion |
32 | Appendix |