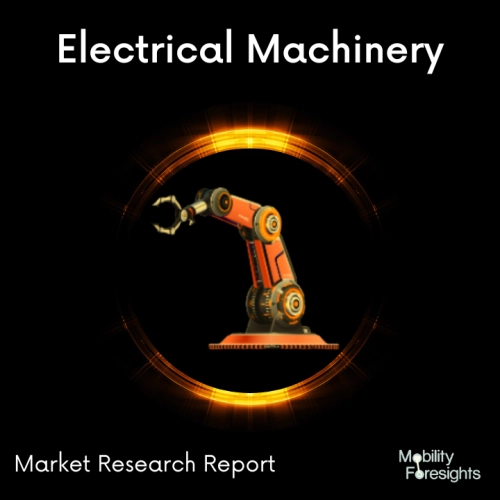
- Get in Touch with Us
Last Updated: Apr 25, 2025 | Study Period: 2023-2030
An air-cooled rectifier does not run the risk of freezing in a room with a temperature below zero degrees Celsius because it does not contain any water. Since no cold water passes through a heat sink, there is no risk of condensation inside the appliance. Water transports heat more effectively than air. As a result, the rectifier needs a lot of airflow to cool it properly.
especially when the temperature outside is high. The rectifier may malfunction as a result of overheating if the surrounding temperature rises beyond the recommended range, also known as getting too high.
The rectifier's performance may suffer as a result of poor air quality, necessitating a more frequent replacement of the inlet air filter. The rectifier may even fail if the air quality is extremely poor.
Water-cooling is a more proficient cooling technique since the warm obstruction is a lot of lower between the intensity sink and water tubes instead of the intensity sink and constrained air. Because water has a much higher energy density than air, it requires less volume.
Because cooling power is entirely dependent on water temperature and flow, the rectifier can continue to function normally even when the surrounding temperature is extremely high.
TheGlobal air cooled rectifier marketaccounted for $XX Billion in 2022 and is anticipated to reach $XX Billion by 2030, registering a CAGR of XX% from 2023 to 2030.
Kraft Powercon introduces an air-cooled rectifier for treating ballast water. ECKraft is made to meet the strict BWMS vibration requirements without the need for vibration dampers, which are a common way to isolate vibration on ships.
Because the rectifier does not move in relation to the ship when vibration dampers are removed, connections are simplified and expensive flexible cables are not required.
Even though ECKraft is simple for users to service and maintain, KraftPowercon has a global service network that can provide prompt support in the event of a problem. Before being discharged into foreign waters, ballast water can be treated with a variety of technologies to remove harmful organisms.
Electro Chlorination Systems (EC), in which ballast water is fed through an electrochemical cell, are currently the most prevalent technology. The salt water is then broken down into hydrogen and sodium hypochlorite by passing an electric current through the cell, which kills any remaining organisms.
Organisms are prevented from being transported between ports or seas as a result of this. The rectifier that supplies the electrical current to the cell is one of this process's most important components. KraftPowercon is now a world-leading supplier for a different BWMS because of its water-cooled FlexKraft Marine rectifiers.
Sl no | Topic |
1 | Market Segmentation |
2 | Scope of the report |
3 | Abbreviations |
4 | Research Methodology |
5 | Executive Summary |
6 | Introduction |
7 | Insights from Industry stakeholders |
8 | Cost breakdown of Product by sub-components and average profit margin |
9 | Disruptive innovation in the Industry |
10 | Technology trends in the Industry |
11 | Consumer trends in the industry |
12 | Recent Production Milestones |
13 | Component Manufacturing in US, EU and China |
14 | COVID-19 impact on overall market |
15 | COVID-19 impact on Production of components |
16 | COVID-19 impact on Point of sale |
17 | Market Segmentation, Dynamics and Forecast by Geography, 2023-2030 |
18 | Market Segmentation, Dynamics and Forecast by Product Type, 2023-2030 |
19 | Market Segmentation, Dynamics and Forecast by Application, 2023-2030 |
20 | Market Segmentation, Dynamics and Forecast by End use, 2023-2030 |
21 | Product installation rate by OEM, 2023 |
22 | Incline/Decline in Average B-2-B selling price in past 5 years |
23 | Competition from substitute products |
24 | Gross margin and average profitability of suppliers |
25 | New product development in past 12 months |
26 | M&A in past 12 months |
27 | Growth strategy of leading players |
28 | Market share of vendors, 2023 |
29 | Company Profiles |
30 | Unmet needs and opportunity for new suppliers |
31 | Conclusion |
32 | Appendix |