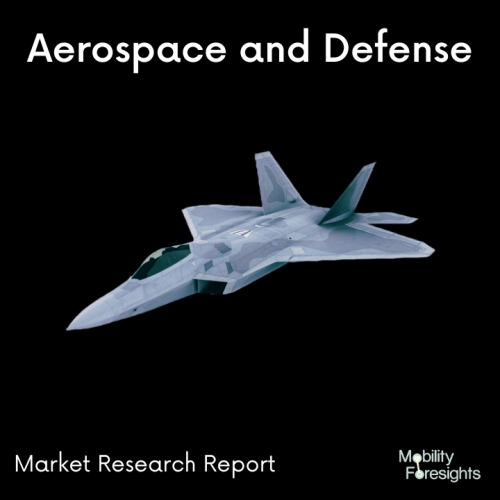
- Get in Touch with Us
Last Updated: Apr 25, 2025 | Study Period: 2024-2030
Aircraft hydraulic actuators are important components used in aircraft hydraulic systems to control various mechanical functions such as landing gear, flaps, rudder, etc. These devices convert hydraulic pressure into mechanical propulsion, allowing precise control of the aircraft surface and other moving objects.
Hydraulic actuators in aircraft are designed to operate under high pressure and harsh environmental conditions. Typically a cylinder, piston, and hydraulic fluid. When a tube is fed into a generator, it drives a piston, which in turn provides the mechanisms needed to control the interior of the aircraft which this mechanism is known for its capabilities reliable and can handle large forces accurately. They are equipped with safety features and redundancies that ensure constant operation even if the system malfunctions.
Recent developments in jet propulsion have included the development of smaller and lighter systems, which contribute to overall fuel efficiency and performance. Innovations point to increased durability and reduced maintenance requirements through advanced materials and advanced repair technologies. In addition, there has been a strong emphasis on integrating smart technologies with sensors that provide real-time information about actuator performance, helping to improve diagnostics and predictive maintenance.
The aircraft hydraulic system market is experiencing steady growth, driven by advances in aerospace technology and increasing demand for efficient and reliable aircraft control systems. Hydraulic actuators are components important in aircraft systems including landing gear, aircraft maintenance, and thrust reversers. Their increased capacity and weight and precise handling make them desirable for modern aircraft.
The market is also influenced by increasing focus on fuel efficiency and aircraft weight reduction including expansion in the aerospace industry, technological advancement in actuator manufacturing, and aircraft increased demand for new. However, challenges such as high development and maintenance costs, and regulatory compliance may affect the growth of the market. Despite these challenges, the market is expected to grow as airlines and aircraft manufacturers look for advanced fluid solutions to improve performance and safety.
The increasing efficiency and reliability of hydraulic systems in modern aircraft drives further advances in aircraft hydraulic systems Hydraulic systems are important components of aircraft systems, aircraft systems, landing gear, and braking systems along with increasing hydraulic efficiency. Increasing air traffic, and expanding commercial and military aircraft worldwide contribute to the increased demand for hydraulic engineers.
Untapped opportunities in the aircraft hydraulic actuator market include advances in materials and technologies to improve actuator performance and reduce weight Innovations such as advanced composites and hydraulic fluids production and better operation can increase the reliability and performance of the actuator.
In addition, there is growth in the aftermarket segment, with replacement and repair of hydraulic actuators offering significant revenue opportunities. Key demands include focusing on improving aviation fuel efficiency, development of actuator technology, and expansion of global aircraft fleet.
Sl No | Company | Product Description | Analyst View |
1 | Moog Inc. | Electro-Hydrostatic Actuator Integrated electric motor, high reliability, and energy efficiency.
| Moog Inc.'s Electro-Hydrostatic Actuator (EHA) represents a major advance in aircraft hydraulic systems by integrating electric motors for improved energy efficiency and reliability, with the airline industry going around more electric airplanes. |
2 | Parker Hannifin | High-Pressure Hydraulic Actuator Enhanced pressure handling, compact design, lightweight. | Parker Hannifin's high-pressure hydraulic actuator is designed for today's aircraft, enhancing performance by providing the ability to operate at higher pressures while maintaining the lightweight, compact design, essential for fuel efficiency. |
3 | Eaton Corporation | Smart Hydraulic Actuator Real-time monitoring, predictive maintenance capabilities, increased safety. | Eatonâs Smart Hydraulic Actuator provides real-time diagnostics and predictive maintenance, significantly improving safety and reducing downtime, which is critical in high--investment aerospace projects. |
4 | Safran | Next-Generation Hydraulic Actuator Lightweight materials, reduced maintenance, high durability. | Safran's next-generation hydraulic actuator focuses on reducing aircraft weight through advanced materials and reducing maintenance requirements, which are critical to modern aviation operational efficiency. Its life expectancy has increased. |
The aircraft hydraulic systems market is growing driven by advances in aerospace technology and increasing demand for high-performance aircraft systems Fluid systems are important control components for systems such as aircraft that are used for landing, wing flaps, and braking during flight to provide the power required for movement. Key players in this market include leading aircraft components manufacturers such as Honeywell International, Parker Hannifin, and Safran, whose focus is on producing high-performance and reliable devices.
New designs aimed at improving actuator performance, reducing weight, and increasing fuel efficiency influence the competitive landscape. Besides the continuing modernization of aircraft and next-generation aircraft that require advanced hydraulic systems to support the market, the commercial airline industryâs growth and rising security costs contribute to hydration as the demand for sophisticated machinery in new and refurbished products increases.
Sl no | Topic |
1 | Market Segmentation |
2 | Scope of the report |
3 | Abbreviations |
4 | Research Methodology |
5 | Executive Summary |
6 | Introduction |
7 | Average B2B price |
8 | Regional Analysis and Trends |
9 | Impact of Aerospace Industry Trends on Aircraft Hydraulic Actuator Demand |
10 | Technology trends in the Industry |
11 | Major key driver in the market |
12 | Recent product development in the market |
13 | Manufacturing footprint for major players |
14 | Recent Orders in Aircraft Hydraulic Actuator Market |
15 | Market dynamics and strategic initiatives |
16 | Analysis of Aircraft Hydraulic Actuator Initiatives on Market Growth |
17 | Impact of Sustainable Practices on Market Trends |
18 | Market Size, Dynamics, and Forecast by Geography, 2024-2030 |
19 | Market Size, Dynamics, and Forecast by End User, 2024-2030 |
20 | Market Size, Dynamics and Forecast by Technology, 2024-2030 |
21 | Market Size, Dynamics, and Forecast by Application, 2024-2030 |
22 | Pricing Strategies and Market Positioning |
23 | Competitive Landscape |
24 | M&A in past 12 months |
25 | Growth strategy of leading players |
26 | Market share of vendors, 2023 |
27 | Company Profiles |
28 | Unmet needs and opportunity for new suppliers |
29 | Conclusion |