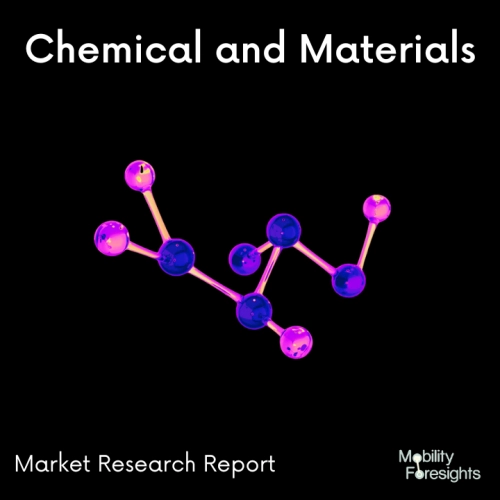
- Get in Touch with Us
Last Updated: Apr 25, 2025 | Study Period: 2024-2030
High temperature aluminium alloys called aluminium cerium alloys have recently been created for use in aerospace and automotive applications.
These lightweight alloys are crucial for the transportation sector, where the design of energy-efficient vehicles is heavily influenced by parameters like weight, cost, and operating temperature.
Aluminium can be alloyed with cerium to produce a castable alloy that is compatible with conventional aluminium alloy additives and has significantly better high-temperature performance. The purpose of the study was to examine how etching of the aluminium cerium might affect its capacity to show its microstructure.
Keller's, Kroll's, and Tucker's reagents were three different etchants that were put to the test. Whereas Keller's reagent revealed the pores and grain boundaries, Kroll's reagent produced dark field illumination.It is possible to see the grain boundaries, topography, precipitates, and pores.
Since the microstructure influences the mechanical characteristics of these alloys, it is beneficial to research how features in the microstructure affect the ultimate tensile strength, toughness, ductility, hardness, corrosion resistance, high/low temperature behaviour, or wear resistance.
The findings indicate that the number and makeup of the precipitates generated are influenced by the cooling rate and the percentage composition of cerium.
The Global Aluminum Cerium Alloy market accountedfor $XX Billion in 2023 and is anticipated to reach $XX Billion by 2030, registering a CAGR of XX% from 2024 to 2030.
A recently created aluminium-cerium alloy has outstanding high-temperature stability and strong corrosion resistance, making it suitable for use in advanced engine components as well as other aerospace, automotive, and power generation applications.
Aluminium can be alloyed with cerium to produce a highly castable alloy that is compatible with conventional aluminium alloy additives and has significantly better high-temperature performance.
These materials have an ultimate tensile strength of 400 MPa at room temperature, a yield strength of 320 MPa, and an 80% mechanical property retention at 240°C.
Al-alloys' mechanical property stability to at least 300 °C and their microstructural stability to over 500 °C are addressed by a mechanism that may permit applications without the need for heat treatment. Last but not least, neutron diffraction under load sheds light on the peculiar principles behind mechanical strength.
The transportation sector, where weight, cost, and operating temperature are crucial considerations in the design of energy-efficient vehicles, benefits from the use of lightweight high-temperature alloys. Aluminium alloys fill this gap affordably, but they have poor mechanical properties at high temperatures.
Sl no | Topic |
1 | Market Segmentation |
2 | Scope of the report |
3 | Abbreviations |
4 | Research Methodology |
5 | Executive Summary |
6 | Introduction |
7 | Insights from Industry stakeholders |
8 | Cost breakdown of Product by sub-components and average profit margin |
9 | Disruptive innovation in the Industry |
10 | Technology trends in the Industry |
11 | Consumer trends in the industry |
12 | Recent Production Milestones |
13 | Component Manufacturing in US, EU and China |
14 | COVID-19 impact on overall market |
15 | COVID-19 impact on Production of components |
16 | COVID-19 impact on Point of sale |
17 | Market Segmentation, Dynamics and Forecast by Geography, 2024-2030 |
18 | Market Segmentation, Dynamics and Forecast by Product Type, 2024-2030 |
19 | Market Segmentation, Dynamics and Forecast by Application, 2024-2030 |
20 | Market Segmentation, Dynamics and Forecast by End use, 2024-2030 |
21 | Product installation rate by OEM, 2023 |
22 | Incline/Decline in Average B-2-B selling price in past 5 years |
23 | Competition from substitute products |
24 | Gross margin and average profitability of suppliers |
25 | New product development in past 12 months |
26 | M&A in past 12 months |
27 | Growth strategy of leading players |
28 | Market share of vendors, 2023 |
29 | Company Profiles |
30 | Unmet needs and opportunity for new suppliers |
31 | Conclusion |
32 | Appendix |