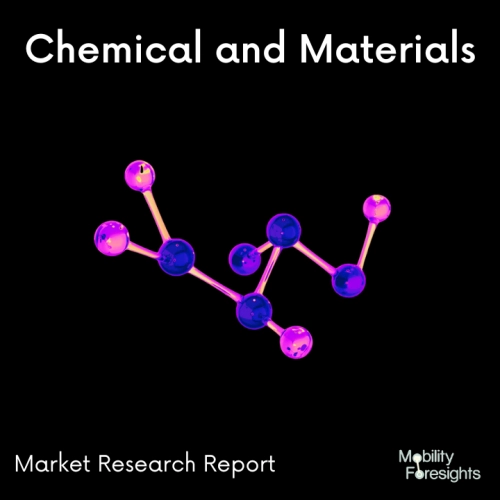
- Get in Touch with Us
Last Updated: Apr 25, 2025 | Study Period: 2024-2030
Aluminium surface treatment is the process of altering the surface of aluminium to improve its properties and performance. This is done by changing the chemical composition or physical structure of the material. Common surface treatments include anodising, painting, powder coating and polishing.
Anodising is an electrochemical process that involves passing a direct current through an electrolyte solution containing the aluminium. This causes the metalâs surface to oxidise, forming an oxide layer. Depending on the type of anodising, this layer can be coloured to improve the aesthetic of the aluminium. Anodising also increases the corrosion resistance of aluminium, making it more durable.
Painting aluminium is a common way to improve its appearance and make it more aesthetically pleasing. This is done using a base coat, followed by a colour coat and a final clear coat. Painting also increases the surface hardness of aluminium, making it more resistant to wear and tear.
Powder coating is a process that involves spraying a dry powder onto the aluminiumâs surface. This powder is made up of a resin and pigment, and it is melted and cured at high temperatures. Powder coating provides a durable finish that is resistant to corrosion and UV damage.
Polishing is the process of buffing the aluminiumâs surface to create a smooth finish. This is done using a rotary polishing machine and specialised polishing compounds. Polishing can enhance the appearance of aluminium and make it look more attractive.
Aluminium surface treatment is an important process that can help improve the properties, performance and aesthetic of aluminium. The type of treatment chosen depends on the application and desired outcome.
The Global Aluminium surface treatment market accounted for $XX Billion in 2023 and is anticipated to reach $XX Billion by 2030, registering a CAGR of XX% from 2024 to 2030.
Aluminium surface treatment is an important process used to improve the quality, longevity, and aesthetics of aluminium products. It is often used to prevent corrosion and wear and tear, as well as to improve the appearance of the product. The most common types of aluminium surface treatments are anodizing, chromate conversion coating, powder coating, and electroplating.
Anodizing is a process in which the surface of aluminium is treated with an acid and then immersed in an electrolytic solution. The acid etches the aluminium surface, creating small pores in the surface, which allow for the absorption of a dye or colouring. This process improves the corrosion resistance, wear resistance, and aesthetic appearance of the aluminium product.
Chromate conversion coating is a process in which the aluminium is treated with a chemical solution that converts the aluminium into a corrosion-resistant and wear-resistant surface. This process also improves the aesthetics of the aluminium product.
Powder coating is a process in which a dry powder coating is applied to the aluminium surface. The powder is then cured at high temperatures, creating a durable and aesthetically pleasing finish.
Electroplating is a process in which an electrical current is used to deposit a thin layer of metal onto the surface of the aluminium. This process improves the wear resistance of the aluminium and can also improve its aesthetic appearance.
In recent years, there have been several new products and companies that have emerged in the aluminium surface treatment market.
Companies such as Alumina, Alcoa, and Aluminum Aerospace have developed new technologies and processes for aluminium surface treatment. These companies have developed new anodizing, chromate conversion coating, and electroplating processes, as well as new powder coating processes.
In addition, several new products have been developed by companies such as 3M and Dow Chemical. These products include new anodizing and chromate conversion coating systems, as well as new powder coating and electroplating systems.
These new products have helped to improve the quality and longevity of aluminium products and have made aluminium surface treatment more efficient and cost-effective.
Sl no | Topic |
1 | Market Segmentation |
2 | Scope of the report |
3 | Abbreviations |
4 | Research Methodology |
5 | Executive Summary |
6 | Introduction |
7 | Insights from Industry stakeholders |
8 | Cost breakdown of Product by sub-components and average profit margin |
9 | Disruptive innovation in the Industry |
10 | Technology trends in the Industry |
11 | Consumer trends in the industry |
12 | Recent Production Milestones |
13 | Component Manufacturing in US, EU and China |
14 | COVID-19 impact on overall market |
15 | COVID-19 impact on Production of components |
16 | COVID-19 impact on Point of sale |
17 | Market Segmentation, Dynamics and Forecast by Geography, 2024-2030 |
18 | Market Segmentation, Dynamics and Forecast by Product Type, 2024-2030 |
19 | Market Segmentation, Dynamics and Forecast by Application, 2024-2030 |
20 | Market Segmentation, Dynamics and Forecast by End use, 2024-2030 |
21 | Product installation rate by OEM, 2023 |
22 | Incline/Decline in Average B-2-B selling price in past 5 years |
23 | Competition from substitute products |
24 | Gross margin and average profitability of suppliers |
25 | New product development in past 12 months |
26 | M&A in past 12 months |
27 | Growth strategy of leading players |
28 | Market share of vendors, 2023 |
29 | Company Profiles |
30 | Unmet needs and opportunity for new suppliers |
31 | Conclusion |
32 | Appendix |