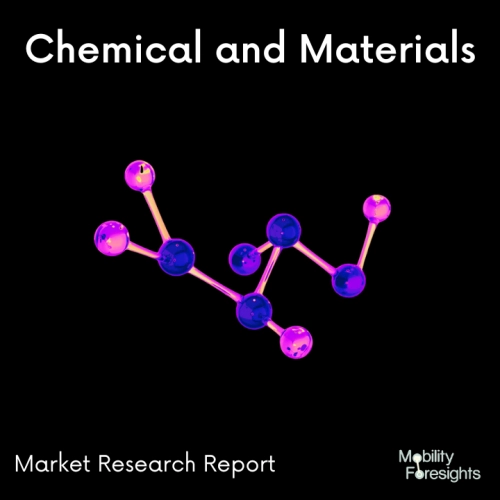
- Get in Touch with Us
Last Updated: Apr 25, 2025 | Study Period: 2023-2030
In a procedure known as chemical milling, the cutting edges of a metal item are submerged in an etchant, which is a caustic chemical solution, frequently an acidic mixture.
The portion of the material, which is frequently aluminium or steel, that needs to be etched reacts with this etching solution, dissolving the solid substance.
Maskants, inert compounds used to cover or protect the parts of the material not being milled during the chemical milling process, are utilised to cover or protect those particular portions. Similar to painting with a painter's mask, this step of the chemical milling process.
The Global Aluminum Chemical milling Market accounted for $XX Billion in 2022 and is anticipated to reach $XX Billion by 2030, registering a CAGR of XX% from 2023 to 2030.
Chemical milling is a procedure employed by the aerospace industry to dissolve undesired aluminium, titanium, steel, etc. during the production of aircraft parts.
Etchant is a strong acid or base solution. The main goal of the chemical milling process is to lighten the weight of fuselage skins and other components in order to increase aircraft performance.
The procedure entails covering the whole component in a special maskant film, followed by the removal (peeling away) of some parts to allow the etchant solution to dissolve (chemically grind) the undesirable portions from the sheet stock.
With removal depths exceeding 10 mm (0.4 inch), the method has been applied to a variety of metals.Chemical milling maskants produced considerable time losses throughout the production process due to the solvent emissions into the atmosphere and the frequent dumping of huge amounts of dissolved aluminium (etchants).
As a leading provider of chemical milling maskants on a global scale, AC Products has contributed to numerous scientific and procedural advancements that lessen the negative effects of the chemical milling process on human health and the environment.
In addition to safeguarding certain parts during different anodizing and plating processes, such as chromic acid anodizing, phosphoric acid anodizing, and metal plating, the maskant film is also useful for protecting other types of parts.
There are numerous ways to comply with current and upcoming VOC rules when using the maskant film, which can be applied either by spraying or by immersion.
Sl no | Topic |
1 | Market Segmentation |
2 | Scope of the report |
3 | Abbreviations |
4 | Research Methodology |
5 | Executive Summary |
6 | Introduction |
7 | Insights from Industry stakeholders |
8 | Cost breakdown of Product by sub-components and average profit margin |
9 | Disruptive innovation in the Industry |
10 | Technology trends in the Industry |
11 | Consumer trends in the industry |
12 | Recent Production Milestones |
13 | Component Manufacturing in US, EU and China |
14 | COVID-19 impact on overall market |
15 | COVID-19 impact on Production of components |
16 | COVID-19 impact on Point of sale |
17 | Market Segmentation, Dynamics and Forecast by Geography, 2023-2030 |
18 | Market Segmentation, Dynamics and Forecast by Product Type, 2023-2030 |
19 | Market Segmentation, Dynamics and Forecast by Application, 2023-2030 |
20 | Market Segmentation, Dynamics and Forecast by End use, 2023-2030 |
21 | Product installation rate by OEM, 2023 |
22 | Incline/Decline in Average B-2-B selling price in past 5 years |
23 | Competition from substitute products |
24 | Gross margin and average profitability of suppliers |
25 | New product development in past 12 months |
26 | M&A in past 12 months |
27 | Growth strategy of leading players |
28 | Market share of vendors, 2023 |
29 | Company Profiles |
30 | Unmet needs and opportunity for new suppliers |
31 | Conclusion |
32 | Appendix |