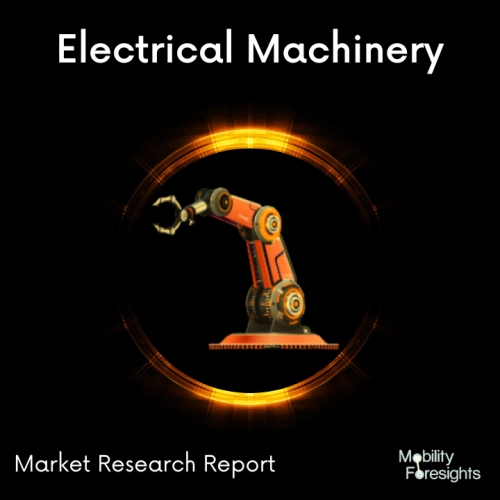
- Get in Touch with Us
Last Updated: Apr 25, 2025 | Study Period: 2024-2030
Multitasking machines have also become a critical part of smart shops and factories. But, the decision to invest in a multitasking machine relies on more than just wanting to get all your parts done in one operation.
Multitasking tends to be synonymous with nouns like productivity, proficiency, and effectiveness. In todayâs world, where everything is surrounded by advanced technology and tight deadlines, multitasking has certainly evolved from a luxury to a necessity.
From smartphones to all-in-one printers, combining capabilities into one product makes tasks go more quickly with added overall efficiency.
Multitasking machines combine the functionality of two or more traditional standalone machine tools to form one âsuperâ machine. In their most common form, multitasking machines combine one or two lathes with a machining center.
However, in recent years additional capabilities (grinding, gear cutting, even Laser Hybrid) have started to integrate as well. The beauty behind multitasking machines is that there are a variety of configurations available.
Multitasking machines evolved gradually, the earliest multitasking machines combining only turning and milling capabilities. However, thereâs a gray area around when they truly came to be because, for some time, they were only recognized as lathes with some machining center functionality and vice versa.
The Global ATC Multitasking Machine market accounted for $XX Billion in 2023 and is anticipated to reach $XX Billion by 2030, registering a CAGR of XX% from 2024 to 2030.
Nakamura-Tome Empowers Machine Operators With Smart Tuning Feature - Nakamura-Tome has added a highly demanded Smart Tuning feature to its ATC multitasking machines. The affected multitasking machines are those with multiple axes (X/Z/Y/B/C).
These multi axes machines are employed for the machining of smooth curves and complex shapes, as they allow for accurate positioning and high accuracy machining.
Prior to Smart Tuning, correcting geometric errors required highly skilled engineers and considerable time on adjustment/setup. With Smart Tuning it is now possible for operators themselves to tune the geometry on periodical maintenance and always keep the machine in high precision.
Common geometric errors can occur from mishaps on the machine, incorrect manual geometric alignment on set up and changes with the machine level/squareness due to temperature or foundation.
The Smart Tuning feature saves valuable time and enables operators to quickly rectify/qualify geometric errors themselves, which can cause deviations in the position of the tool spindle and the accuracy of the part being machined.
Sl no | Topic |
1 | Market Segmentation |
2 | Scope of the report |
3 | Abbreviations |
4 | Research Methodology |
5 | Executive Summary |
6 | Introduction |
7 | Insights from Industry stakeholders |
8 | Cost breakdown of Product by sub-components and average profit margin |
9 | Disruptive innovation in the Industry |
10 | Technology trends in the Industry |
11 | Consumer trends in the industry |
12 | Recent Production Milestones |
13 | Component Manufacturing in US, EU and China |
14 | COVID-19 impact on overall market |
15 | COVID-19 impact on Production of components |
16 | COVID-19 impact on Point of sale |
17 | Market Segmentation, Dynamics and Forecast by Geography, 2024-2030 |
18 | Market Segmentation, Dynamics and Forecast by Product Type, 2024-2030 |
19 | Market Segmentation, Dynamics and Forecast by Application, 2024-2030 |
20 | Market Segmentation, Dynamics and Forecast by End use, 2024-2030 |
21 | Product installation rate by OEM, 2023 |
22 | Incline/Decline in Average B-2-B selling price in past 5 years |
23 | Competition from substitute products |
24 | Gross margin and average profitability of suppliers |
25 | New product development in past 12 months |
26 | M&A in past 12 months |
27 | Growth strategy of leading players |
28 | Market share of vendors, 2023 |
29 | Company Profiles |
30 | Unmet needs and opportunity for new suppliers |
31 | Conclusion |
32 | Appendix |