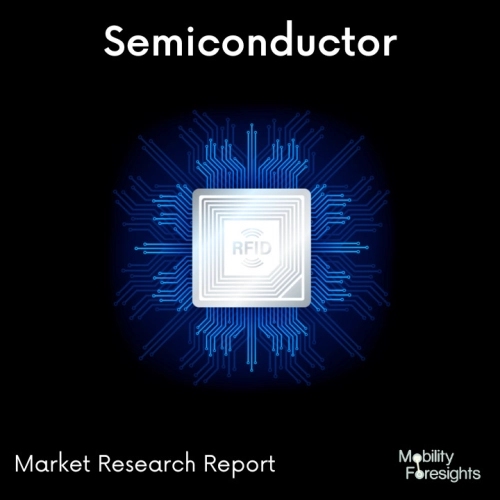
- Get in Touch with Us
Last Updated: Apr 25, 2025 | Study Period:
A self-limiting, sequential surface chemistry called atomic layer deposition (ALD) produces conformal thin films of materials onto substrates with different compositions. Quotation taken from: Handbook of Deposition Technologies for Films and Coatings.
A technology for producing thin films for a variety of uses is atomic layer deposition (ALD). ALD is a unique application of chemical vapour deposition where the desired material is formed by chemical surface reactions using gaseous reactants that are injected into the reaction chamber.
A controlled type of chemical vapour deposition is called atomic layer deposition (ALD) (CVD). To cover all exposed substrate surfaces for coating, ALD employs timed pulses of reactive precursors. Its name is derived from the fact that each of these pulses instals a single self-terminating layer.
Thick atomic layers are not required because ALD can build substrates for microelectronics and nanotechnology. Numerous substrates are ineffective due to their fragility or impurity. Typically, impurities can be detected there.
High-k dielectric films used in CMOS processors, memory devices, MEMS, and sensors are frequently produced using ALD in the semiconductor industry.
For the creation of functional and protective coatings in fuel cells and other applications needing corrosion or wear resistance, ALD technologies are used.
Reliable and exact: Process-dependent, the film growth thickness during a single ALD cycle is typically around 1. (0.1 nm).
ALD makes it possible to deposit layers that are thin, dense, and smoothâless than one nanometer thick. Currently, some industrial applications use coatings as thin as 0.8 nm.
The Global Atomic Layer Deposition Coating Systems market accounted for $XX Billion in 2023 and is anticipated to reach $XX Billion by 2030, registering a CAGR of XX% from 2024 to 2030.
Picosun Oy, a leading producer of atomic layer deposition (ALD) equipment, has introduced the new Picofloat particle coating technology.
The Picofloat technology provides uniform ALD film deposition on every particle down to nanoscaled dimensions by continuously moving the powder to be coated.
The advanced thin film coating technique known as atomic layer deposition (ALD) is used to create ultrathin, incredibly homogeneous, and conformal material layers.
Gas phase chemical processes that are sequential, self-limiting, and surface-controlled are used in ALD to regulate film growth in the nanometer/sub-nanometer thickness regime.
The ALD film is dense, free of cracks, defects, and pinholes, and its thickness, as well as its structural and chemical quality, can be accurately controlled on an atomic scale. Film growth occurs by adding successive atomic layers "up" from the surface.
Through the use of ALD coatings, the surface of the particles can be customised to correspond to their electrical, optical, physical, or chemical properties, or the particles can be functionalized to perform entirely new functions.
ALD is also more environmentally friendly than traditional, wet chemistry-based techniques for producing catalysts.
On the other hand, carbon-based nanomaterials like carbon nanoparticles, -wires, and -tubes have an almost infinite number of applications in fields like tomorrow's electronics, energy production, and storage.
Additionally, with the use of ALD coatings, these materials can be modified to create entirely new, unheard-of products, devices, and applications.
Sl no | Topic |
1 | Market Segmentation |
2 | Scope of the report |
3 | Abbreviations |
4 | Research Methodology |
5 | Executive Summary |
6 | Introduction |
7 | Insights from Industry stakeholders |
8 | Cost breakdown of Product by sub-components and average profit margin |
9 | Disruptive innovation in the Industry |
10 | Technology trends in the Industry |
11 | Consumer trends in the industry |
12 | Recent Production Milestones |
13 | Component Manufacturing in US, EU and China |
14 | COVID-19 impact on overall market |
15 | COVID-19 impact on Production of components |
16 | COVID-19 impact on Point of sale |
17 | Market Segmentation, Dynamics and Forecast by Geography, 2024-2030 |
18 | Market Segmentation, Dynamics and Forecast by Product Type, 2024-2030 |
19 | Market Segmentation, Dynamics and Forecast by Application, 2024-2030 |
20 | Market Segmentation, Dynamics and Forecast by End use, 2024-2030 |
21 | Product installation rate by OEM, 2023 |
22 | Incline/Decline in Average B-2-B selling price in past 5 years |
23 | Competition from substitute products |
24 | Gross margin and average profitability of suppliers |
25 | New product development in past 12 months |
26 | M&A in past 12 months |
27 | Growth strategy of leading players |
28 | Market share of vendors, 2023 |
29 | Company Profiles |
30 | Unmet needs and opportunity for new suppliers |
31 | Conclusion |
32 | Appendix |