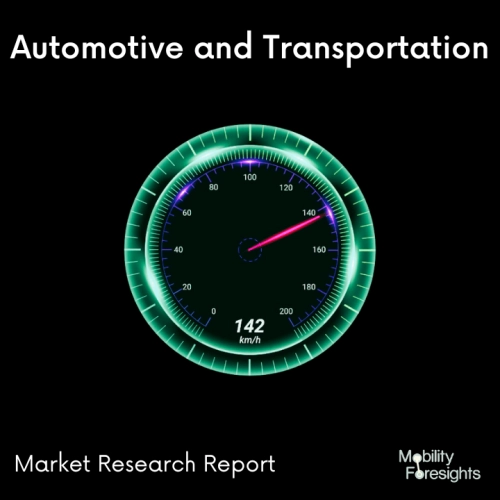
- Get in Touch with Us
Last Updated: Apr 25, 2025 | Study Period: 2024-2030
AGV (Automated Guided Vehicle) is a portable robot that follows a particular path designed for it. The path can be given as marked long lines, wires on the floor, radio waves, magnetic tapes, vision cameras, or laser navigation.They are most often used in industrial applications to transport heavy materials around a large industrial building, such as a factory or warehouse.
AGVs are programmed to ensure security & safety and come installed with cameras, lasers, and other sensors that allow them to safely operate within the industry, plant, or company. Increased safety leads to reduced cost and operational downtime, which, in turn, increases the productivity of many operations.
The growth of the AGV market is driven by growing demand for automation in material handling across industries, a shift in demand from mass production to mass customization, the rising popularity of e-commerce owing to COVID-19, and improved safety standards at workplaces. Moreover, industrial growth in emerging economies, the presence of the intralogistics sector in Southeast Asia, and the rising adoption of industrial automation by SMEs are likely to fuel the growth of the market.
To learn more about the Global Forked Automated Guided Vehicle Market, read our report
S No | Company Name | Development |
1 | Res Green | Res Green Introduces a New Automatic Guided Vehicle (AGV) that Moves Loads in Both DirectionsRes Green Group International, a provider of cutting-edge mobile robot and software solutions, unveiled its bidirectional Big Buddy, one of the most durable AGVs in the business that transports cargoes via magnetic tape. |
2 | Nidec-Shampoo Corporation | Nidec-Shampoo Corporation announces the introduction of a new automated guided vehicle under the S-CART brand.The new AGV, known as the S-CART-V, is equipped with a vision-based navigation system1 that makes use of Canon's Visual SLAM2 technology. |
3 | Syntonic | A cutting-edge AGV system-specific control platform has been created by Syntonic, a multinational design firm with sophisticated automation skills. |
4 | ECA GROUP | The industry will be introduced to ECA GROUP's latest generation Indoor/Outdoor autonomous AGV.Logistics operations within production management are also affected by these new issues and are continuously looking for creative solutions that can be developed, validated, and implemented without disrupting or changing current flow and infrastructures. |
Big Buddywas designed for packed warehouses that demand high agility as well as tough industrial settings. Big Buddy delivers zero-point turning because of its two separate driving motors. It moves straight ahead while empty.When designing the Big Buddy AGV, which has two 16-zone LiDAR lasers at the front and back of the vehicle, Res Green engineers put safety first. It makes use of LiFePO4 batteries, which are heat- and fire-resistant.
The firstS-CART-Vmodel will be based on the payload version of the original S-CART, but Nidec-Shampoo intends to continue releasing future versions with visual-based navigation. This AGV will be the first in the industry to use vision-based navigation. Since the logistics industry has turned its focus to improving efficiency and reducing labor costs in factories and warehouses, the demand for AGVs has grown.
Nidec-Shampoo provides a solution with the S-CART-V that can make use of a vision-based navigation system for AGVs created by Canon to simultaneously estimate its surroundings in three dimensions and the location of the AGV using wide-angle (horizontal and vertical) footage recorded by a stereo camera.
With the reliable integration of software and hardware, the new platformSYNTRONICScombines data acquisition and actuators to facilitate the seamless deployment of AGV systems. The control platform has a multi-core processor for signal processing and acquisition as well as a core computer server for cost-effectiveness and performance.
The platform is specifically designed to optimize integration, guarantee reliable product applications, and lower hardware costs. The control platform has several navigation characteristics, including the ability to support two-dimensional code, laser reflector, magnetic, laser, and visual composite navigation. Additionally, its motion chassis control supports differential drive, single steering gear drive, multiple steering gear drive omnidirectional, as well as a variety of other chassis designs, demonstrating outstanding adaptability to a variety of settings.
The Automated Guided Vehicles (AGV) fromECA Groupmeet the needs of manufacturers and the logistic equipment suppliers who serve them today. The automated industrial vehicles created by ECA GROUP are based on SLAM (Simultaneous Localization and Mapping) technology, which allows the machine to "recognize" its surroundings, adapt its navigation and behavior to a specific circumstance, and adhere to the highest safety standards.
ECA Group AGVs are the first of their kind and are currently being produced, delivered, and tested in one of the most demanding industrial environments, such as an aluminum smelter plant. They were designed and developed for indoor, outdoor, and multi-building operations without any existing infrastructure modification or additional installations.
The Global Ultrasonic Gas Leak Detector Market accounted for $XX Billion in 2023 and is anticipated to reach $XX Billion by 2030, registering a CAGR of XX% from 2024 to 2030.
Sl. no. | Company Name | Model | Application | Capacity | Type |
1 | KUKA | KUKA Mobile platform 1500 | handles the transport of products through process steps | 1500kg | Intelligent & Autonomous mobile platform |
KUKA Navigation solution mobile robots | perform driving and handling tasks in a fully self-contained manner | flexible | Material movement | ||
KUKA triple lift | maintenance, repairs, and overhauls (MRO) | 1000kg, 8m in 120 sec | Triple lift | ||
2 | SSI Schafer | Low lifters | load carrier between transfer stations | up to 200mm parallel to the ground | Heavy Load carrier |
High lifters | picked up and placed on transfer stations at low heights | up to 8.5m | |||
Very Narrow Aisle (VNA) | specially developed for use in warehouses with narrow aisles | ||||
WEASEL | Automating transport tasks | 35kg | Small load carrier | ||
Compact | Automating transport tasks | up to 100kg | |||
3 | Toyota Industries | Tug Cart | Movement of assembly workbenches | flexible | Material movement |
High-speed rail guided vehicle system | Sorting | 1000kg | Sorting | ||
4 | E&K Automation | VARIO Move L | High lift transport | Transport and material flow | |
VARIO Move CB | automatic counterweight transport | 1600kg | |||
VARIO MOVE CTO | Surface moving transport with conveyors | ||||
VARIO MOVE CTO | Transport with conveyor technology | ||||
VARIO MOVE AS | High-lift transport with external radars | 1600kg | |||
SMART MOVE L14 | Automated high-lift truck | Forklift | |||
Universal Counterweight forklift | Automated high-lift truck with laser navigation | 600,1000,1200,1600 kgs | |||
Driverless tug | High towing capacity | 5000kg | Trailer puller | ||
Smart move ERE 225 | Automated low-lift trucks | 2500kg | Material movement | ||
5 | Oceaneering | Compact Mover Vehicle | move small, light loads such as pallets, metal boxes, and plastic totes | up to 2000kg, 1.9m/s | Material movement |
Max Mover Vehicle | transport heavy loads with various sizes | up to 7000kg | forklifts | ||
Uni Mover Vehicle | Single and multi-load carrier, Omnidirectional/Unidirectional | up to 3000kg, 1.6m/s | tunneling vehicles |
Lights-out automation has been the intended result for various manufacturing facilities. Lights-out automation involves fully automated systems for various components in manufacturing.
Warehouses run completely based on automation which eliminates the need for additional costs for lighting. A majority of the factories have been trying to limit human intervention, limit the scope for errors, and increase productivity.
The overall need for high efficiency in the automotive, healthcare, e-commerce, and food & beverages industries is increasing the demand for automation.
The AGV-enabled automation of industrial facilities can help meet the requirements related to material handling capacity, along with reducing production time, lessening the chances of human errors, enhancing safety, ensuring high production volumes, and increasing accuracy and repeatability.
Traditional industrial facilities are slowly evolving into smart, connected, and highly efficient automated facilities by integrating Industry 4.0 with automation systems. Industry 4.0 is capable of converting an industrial facility into an autonomous plant.
It combines computers and industrial automation solutions with the help of robotics to form a single automated unit. The network of connected devices creates a smart architecture capable of making decentralized decisions. The growth of Industry 4.0 is changing the functioning of warehouses. Industry 4.0 also aims to create an operational environment wherein humans and robots can work together efficiently.
Low labor prices in emerging economies such as India, Bangladesh, and Tanzania restrict the adoption of automation across the industries in these countries. The automation of industrial facilities makes little or no economic sense in these countries where abundant cheap labor is readily available.
In India, automation in manufacturing facilities is less prevalent than their foreign counterparts, since the cost advantage in labor trade-off with robots is less due to the availability of cheap labor. Moreover, emerging countries such as Bangladesh, Cuba, and Tanzania have low average daily wages. Companies in emerging countries are reluctant to invest in automated equipment, such as AGVs, due to the availability of low-cost labor.
The retail industryâs growth is primarily driven by the increasing demand from e-commerce, primarily for automated warehouse solutions.
According to the e-commerce Europe report, the regionâs online sales increased by 13% in 2019, and total sales were valued at EUR 621 billion, and the concentration of the market is expected to be focused in Western Europe, a majority of the turnover from the B2C platform is from the region (66%). Owing to such developments, vendors in the market are increasingly adopting automation.
SI No | Timeline | Developments |
1 | Q4-2021 | The high-performance laser-guided automated vehicles are used in deep freeze warehouses for pallet movements for faster, safer, and increased performance of work and also reduce human efforts. |
2 | Q4-2021 | Natural navigation provider for AMRs and AGVS, Blue Biotics to expand its market in Asian regions by partnering with factory automation specialist Planet T & S Co Ltd for the Thailand automated guided vehicle market. |
3 | Q4-2021 | Due to labor shortages and increased demand for production industries are adopting automated guided vehicles for the induced production capacity, quality, and reduced labor costs. |
4 | Q3-2021 | Mitsubishi to implement automated guided vehicles for the packaging company DS Smith to maximize sustainability and efficiency. |
Owing to rapid technological advancements in robotics and automation, the manufacturing sector has witnessed increased adoption of technology in its production process. Manufacturers consider factors such as load, orientation, speed, precision, duty cycle, travel, and environment before selecting the robot that will be the most effective and profitable in their manufacturing plant.
The global Automated Guided Vehicle market growth is primarily driven by the rising e-commerce industry and the growing adoption of automation in warehouses for efficient and smooth operations. The use of Automated Guided Vehicles helps manufacturers to achieve enhanced quality and reliability in warehouse operations.
Moreover, factors such as a shortage of skilled workforce and high labor costs also drive the adoption of AGV across various industries worldwide. Several organizations have implemented automated guided vehicle solutions to reduce their labor costs and improve efficiency. Although the initial cost of procuring a robot is high, once implemented, it offers high productivity, efficiency, and profits.
The increasing automation in the material handling process has aided industries to have connected factories equipped with big data, machine learning, etc., resulting in the embracing of automated material handling systems.
Companies such as Amazon, Walmart, Alibaba, etc., are focusing on the automation of material handling processes to reduce operation costs and increase inventory size. This aids them in improved quality control and enhanced labor management.
Amid the ongoing outbreak of COVID-19 across the region, hospitals have also been seen increasingly using AGVs for delivering medicines to patients while reducing human interventions. For instance, in March 2020, Homogamy Base Hospital in Sri Lanka mentioned deploying AVG to assist in the treatment of persons suspected of COVID-19 virus.
A strategic agreement between Blue Biotics SA and Prologue Automation GmbH was announced last week to promote the use of automated guided vehicles or AGVs, throughout the German manufacturing and logistics sectors.
With more than 20 years of experience in the field, Blue Biotics offers its Autonomous Navigation Technology (ANT) and knowledgeable assistance to customers so they may commercialize their AGVs, automated forklifts, or mobile robots.
SI No | Timeline | Company | Developments |
1 | Q4-2021 | GECOM Corporation | GECOM Corporation introduced advanced automatic guided vehicles using navigation and control technologies for lineside delivery and pickup automation. |
2 | Q4-2021 | Continental | German company Continental unveiled its new automatic guided vehicle to improve production operations, the robot can lift heavy loads of more than tons and test autonomously for brake production. |
3 | Q4-2021 | Balyo | Robotic startup Balyo supplies automated guided vehicle robots for warehouses and factories around the world to increase the efficiency of production with minimal monitoring and interference.Q3 |
4 | Q4-2021 | Audi | Audi to use automated guided vehicles for intralogistics transport at its manufacturing site in Neckarsulm, Germany where the Audi R8 is manufactured. |
Tow vehicles, also known as tuggers, pull non-powered carts carrying huge loads. This is the most productive type of AGV used for towing and tugging as it can move more load with multiple trailers than a single fork truck.
The companies are focusing on operating more efficiently due to the growing pressure on retail companies to meet the ever-increasing demand of their customers. The foreseeable decline in the growth of end-user industries may have a considerable direct impact on the AGV market.
The growth of the laser-guided AGVs market can be attributed to the flexibility, scalability, and accuracy of the laser guidance technology. It also improves safety, increases throughput, and minimizes downtime. Laser guidance is the most flexible system for vehicle movement and offers accurate navigation. It allows the vehicles to operate in a warehouse without the need for invasive barriers.
APAC is likely to be the fastest-growing region in the AGV market. China and Japan are the countries driving the growth of the AGV market in APAC. The rapid growth of automotive, e-commerce, food & beverages, and healthcare industries in emerging economies, such as China, India, and South Korea, has contributed to the growth of the AGV market in APAC.
Moreover, governments in APAC countries are increasingly emphasizing safety and security on production floors, which can be best achieved by the implementation of AGVs. Asian countries under lockdown have suffered tremendous loss of business and revenue due to the shutdown of many manufacturing units. This has impacted the demand for AGV in 2020.
Toyota Industries Corporation (TICO) will combine its software development in autonomous vehicles (AVs), raise its global investments, and establish T-Hive B.V. as a new center of competence to satisfy the growing demands of its customers.
TICO's main brand's solution portfolio will be significantly strengthened and expanded by combining the software products, partnerships, and innovations from TICO's main Group companies, Toyota L&F, Toyota Material Handling, Toyota Material Handling Europe, Raymond, Bastian Solutions, and Vanderlande, and their respective brands.
The need for AVs has risen in recent years, owing to the rapid growth of the e-commerce business, general labor shortages, and the requirement for flexibility.
Flexibility in operations, application regions, and vehicle type, as well as the ability to deploy AV solutions globally, have become increasingly significant. To help TICO's customer-facing companies, T-Hive was created to centrally manage all developments, use current solutions for new market sectors, and expedite innovation globally.
T-major Hive's goal will be to provide a unified control system for all automated guided forklifts (AGFs), automated guided vehicles (AGVs), and autonomous mobile robots inside TICO (AMRs).
TICO's customers will be able to enjoy seamless transportation, storage, and distribution of goods throughout their entire supply chains thanks to the unified solution portfolio, which will be launched at logistics facilities around the world.
The K55 Pallet Stacker, one of Kivon's newest AGVs, will be made available. For end-of-line palletizing, food and beverage, and retail applications, the K55 is the best choice. It is intended to guarantee effectiveness, dependability, and total safety.
The K55 Pallet Stacker, which has lifting forks, can elevate objects to a height of up to 1500 mm and automatically carry palletized items weighing up to 1200 kg.
The automated forklift is based on a straightforward, dependable, well-engineered design that will ensure it completes its tasks smoothly and dependably, similar to all Kivon AGV/AMR ranges.
The Jung Heinrich EKX 516ka / 516a Automated High-Rack Stacker was just introduced by Mitsubishi Loges Next Americas group, the sole distributor of Jung Heinrich® lift trucks, narrow-aisle, and automated guided vehicles in the United States, Canada, and Mexico.
With a small design and 180-degree swiveling prongs, the EKX is specifically made for very tight aisle operations and can fit down aisles as narrow as 68 inches. With a lift height of up to 511 inches and a lift capability of 3,500 pounds, it is perfect for high-density storage, maximizing the available space in warehouses and distribution centers.
The world's first hydrogen-powered fuel cell Automated Guided Vehicles (AGV H2) for seaports have been introduced by GAUSSIAN, a pioneer in the clean and intelligent transport of products and people. Following the introduction of the hydrogen-powered fuel cell ATM and APM, these new vehicles round-up GAUSSIN's lineup of hydrogen-powered automobiles.
The AGV can operate autonomously in environments with mixed traffic and no infrastructure. It will support port operators' swift transition to zero-emission, as well as longer operation hours, quicker and less frequent fueling, and efficient and quiet transportation.
A revolutionary AGV (Automated Guided Vehicle) platform has been made commercially available by Comeau, an international firm based in Italy that specializes in industrial automation. This platform is adaptable enough to be used in a variety of manufacturing and non-manufacturing settings. The new AGV platform's first automated guided vehicle, called Agile1500, completely embodies Comeau's open automation design methodology.
Agile1500 is crucial in the creation of a new operating system mandated by Industry 4.0. Thanks to cutting-edge security features and an inbuilt laser scanner that stops the AGV when it detects an obstruction in its path, it can improve overall plant safety.
Stabil Robotics' brand-new PF3 automated guided vehicle, or AGV won this year's Best Smart Product prize in the prestigious Red Dot Design competition.
According to the company, the new robot has a positioning accuracy of +/-5 mm (0.19 in.) and can navigate around obstacles. Its height with the lift unit is 400 mm (15.7 in.). The PF3 has five emergency stop buttons, a collision avoidance sensor, a 360-degree human safety scanner, a collision avoidance sensor, and an LED strip that displays the state of the AGV for further security.
The STILL iGo neo-CX 20 is a new line of autonomous guided vehicles (AGVs) from the KION Group. The AGVs use laser and optical sensors to navigate around obstacles and are intended for use in warehouse and logistics operations.
SI No | Timeline | Company | Developments |
1 | Q4-2021 | Dematic | US-based material handling systems, software, and services provider Dematic made $3.2 billion in revenue in 2021 with a 21.2% growth rate. Dematicâs product demand increased during the pandemic because of a surge in automation. |
2 | Q4-2021 | Daifuku Co. Ltd. | Japanese material handling company Daifuku Co. Ltd. made INR 12320 crore in September 2021 with 6.17% year-over-year growth. |
3 | Q4-2021 | Hyster-Yale Material Handling | Hyster-Yale Material Handling, announced its third-quarter earnings of $748 million in revenue with a net loss of $77 million, the decrease in revenue from last year's quarter due to the production and shipment disrupted by components availability. |
4 | Q2-2021
| See grid | Autonomous robots developer for material handling company See Grid announced its revenue doubled year over year due to increased demand for automation technology in e-commerce, logistics, and manufacturing companies. |
The market players in the automated guided vehicle market are focusing on expanding through strategic interventions, such as acquisitions, collaborations, expansion, and launching advanced products in the automated guided vehicle market.
Factors such as the digital transformation and the advent of integrated Industry 4.0 with IoT, will provide considerable growth opportunities to automated guided vehicle industries.
In 2018, Nidec-Shampoo launched new versions of its automated guided vehicle, the S-Cart. The new model to be launched by Nidec-Shampoo is based on the companyâs guideless navigation AGV âS-Cartâ â the 100 kg payload version â that hit the market in 2016, and has been updated with a function that lets it track and follow a person or object.
In March 2020, See Grid Corporation raised USD 25 million in an equity funding round led by venture capital firm G2VP. The company has mentioned that the funding is driven due to the COVID-19 outbreak, and the industry requires non-essential workers to adhere to social distancing along with plenty of industrial roles that need people to be physically present.
In February 2020, China-based robotics firm - Geek+ specializes in robotics technologies for logistics, announced plans to expand its operations in the United States. The company has inaugurated its office in California to manage robotic warehouse and smart factory projects in the country.
North America
The North American market, particularly the USA, will be one of the prime markets for the automated Guided Vehicle Market) due to the nature of industrial automation in the region, high consumer spending compared to other regions, and the growth of various industries, mainly AI, along with constant technological advancements. The GDP of the USA is one of the largest in the world, and it is home to various industries such as Pharmaceuticals, Aerospace, and Technology. The average consumer spending in the region was $72K in 2023, and this is set to increase over the forecast period. Industries are focused on industrial automation and increasing efficiency in the region. This will be facilitated by the growth in IoT and AI across the board. Due to tensions in geopolitics, much manufacturing is set to shift towards the USA and Mexico, away from China. This shift will include industries such as semiconductors and automotive.
Europe
The European market, particularly Western Europe, is another prime market for (Automated Guided Vehicle Market) due to the strong economic conditions in the region, bolstered by robust systems that support sustained growth. This includes research and development of new technologies, constant innovation, and developments across various industries that promote regional growth. Investments are being made to develop and improve existing infrastructure, enabling various industries to thrive. In Western Europe, the margins for the automated Guided Vehicle Market) are higher than in other parts of the world due to regional supply and demand dynamics. Average consumer spending in the region was lower than in the USA in 2023, but it is expected to increase over the forecast period.
Eastern Europe is anticipated to experience a higher growth rate compared to Western Europe, as significant shifts in manufacturing and development are taking place in countries like Poland and Hungary. However, the Russia-Ukraine war is currently disrupting growth in this region, with the lack of an immediate resolution negatively impacting growth and creating instability in neighboring areas. Despite these challenges, technological hubs are emerging in Eastern Europe, driven by lower labor costs and a strong supply of technological capabilities compared to Western Europe.
There is a significant boom in manufacturing within Europe, especially in the semiconductor industry, which is expected to influence other industries. Major improvements in the development of sectors such as renewable energy, industrial automation, automotive manufacturing, battery manufacturing, recycling, and AI are poised to promote the growth of (the Automated Guided Vehicle Market) in the region.
Asia
Asia will continue to be the global manufacturing hub for (the Automated Guided Vehicle Market) over the forecast period with China dominating the manufacturing. However, there will be a shift in manufacturing towards other Asian countries such as India and Vietnam. The technological developments will come from China, Japan, South Korea, and India for the region. There is a trend to improve the efficiency as well as the quality of goods and services to keep up with the standards that are present internationally as well as win the fight in terms of pricing in this region. The demand in this region will also be driven by infrastructural developments that will take place over the forecast period to improve the output for various industries in different countries.
There will be higher growth in the Middle East as investments fall into place to improve their standing in various industries away from petroleum. Plans such as Saudi Arabia Vision 2030, Qatar Vision 2030, and Abu Dhabi 2030 will cause developments across multiple industries in the region. There is a focus on improving the manufacturing sector as well as the knowledge-based services to cater to the needs of the region and the rest of the world. Due to the shifting nature of fossil fuels, the region will be ready with multiple other revenue sources by the time comes, though fossil fuels are not going away any time soon.
Africa
Africa is expected to see the largest growth in (Automated Guided Vehicle Market) over the forecast period, as the region prepares to advance across multiple fronts. This growth aligns with the surge of investments targeting key sectors such as agriculture, mining, financial services, manufacturing, logistics, automotive, and healthcare. These investments are poised to stimulate overall regional growth, creating ripple effects across other industries as consumer spending increases, access to products improves, and product offerings expand. This development is supported by both established companies and startups in the region, with assistance from various charitable organizations. Additionally, the presence of a young workforce will address various existing regional challenges. There has been an improvement in political stability, which has attracted and will continue to attract more foreign investments. Initiatives like the African Continental Free Trade Area (AfCFTA) are set to facilitate the easier movement of goods and services within the region, further enhancing the economic landscape.
RoW
Latin America and the Oceania region will showcase growth over the forecast period in the automated Guided Vehicle Market). In Latin America, the focus in the forecast period will be to improve their manufacturing capabilities which is supported by foreign investments in the region. This will be across industries mainly automotive and medical devices. There will also be an increase in mining activities over the forecast period in this region. The area is ripe for industrial automation to enable improvements in manufacturing across different industries and efficiency improvements. This will lead to the growth of other industries in the region.
Margin Comparison (Highest to lowest) | Region | Remarks |
1 | Europe | The supply chain demands and the purchasing power in the region enable suppliers to extradite a larger margin from this region than other regions. This is for both locally manufactured as well as imported goods and services in the region. |
2 | North America | Due to the high spending power in this region, the margins are higher compared to the rest of the world, but they are lower than in Europe as there is higher competition in this region. All the suppliers of goods and services target the USA as a main market thereby decreasing their margins compared to Europe |
3 | Asia | Lower purchasing power, coupled with higher accessibility of services in this region doesnât enable suppliers to charge a high margin making it lower than Europe and North America. The quality of goods and services is also affected due to this aspect in the region |
4 | Africa and ROW | The margins are the lowest in this region, except for Australia and New Zealand as the countries in this region donât have much spending power and a large portion of the products and services from this area is exported to other parts of the |
Sl no | Topic |
1 | Market Segmentation |
2 | Scope of the report |
3 | Abbreviations |
4 | Research Methodology |
5 | Executive Summary |
6 | Introduction |
7 | Insights from Industry stakeholders |
8 | Cost breakdown of Product by sub-components and average profit margin |
9 | Disruptive innovation in the Industry |
10 | Technology trends in the Industry |
11 | Consumer trends in the industry |
12 | Recent Production Milestones |
13 | Component Manufacturing in US, EU and China |
14 | COVID-19 impact on overall market |
15 | COVID-19 impact on Production of components |
16 | COVID-19 impact on Point of sale |
17 | Market Segmentation, Dynamics and Forecast by Geography, 2024-2030 |
18 | Market Segmentation, Dynamics and Forecast by Product Type, 2024-2030 |
19 | Market Segmentation, Dynamics and Forecast by Application, 2024-2030 |
20 | Market Segmentation, Dynamics and Forecast by End use, 2024-2030 |
21 | Product installation rate by OEM, 2023 |
22 | Incline/Decline in Average B-2-B selling price in past 5 years |
23 | Competition from substitute products |
24 | Gross margin and average profitability of suppliers |
25 | New product development in past 12 months |
26 | M&A in past 12 months |
27 | Growth strategy of leading players |
28 | Market share of vendors, 2023 |
29 | Company Profiles |
30 | Unmet needs and opportunity for new suppliers |
31 | Conclusion |
32 | Appendix |