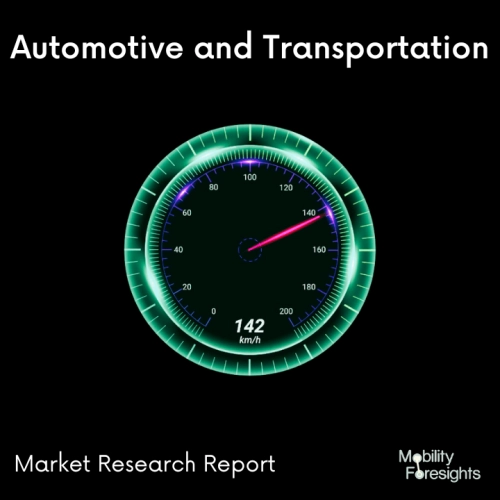
- Get in Touch with Us
Last Updated: Apr 25, 2025 | Study Period: 2024-2030
Over the course of a decade, 3D printers have progressed from an optional piece of equipment for manufacturing relatively simple prototypes to an imperative need â one that is fundamentally changing the automobile industry.
3D printers are now fixtures in automotive design studios, factory assembly lines, and test tracks, generating complicated parts, shortening manufacturing cycles, improving measurement and testing, and enabling customizable options across all facets of vehicle development.
The ISO/ASTM 52900 standard, developed in 2015 to unify the language around 3D printing, describes it as "the process of combining materials to manufacture things from 3D model data, generally layer upon layer, as contrasted to manufacturing methods and creative manufacturing approaches."
In layman's words, it is a new manner of making things that is very different from how things have been manufactured 'traditionally.'
It is often incredibly quick, has cheap fixed setup costs, and can produce far more complicated geometries than was previously conceivable, with the ever variety of materials.
It has been widely employed in engineering, notably for prototyping and producing lightweight geometries, as well as in medical, education, architecture, and entertainment. Maker culture, enthusiasts and amateurs, tiny desktop printers, low-cost printing methods such as FDM, and low-cost materials like ABS and PLA are all widely linked with 3D printing.
SI no | Timeline | Company | Mergers/New Plant |
1 | November 2021 | BigRep | A Berlin-based large-format 3D printer has announced a partnership with Teton Simulation to combine 3D printing and Smartslice Technology. |
2 | November 2021 | Protolabs | Protolabs will open a new production facility that will expand the 3D printing capacity by 60%. |
3 | October 2021 | WASP | Italian 3D printer manufacturer and Honda announced a joint project to provide greater freedom in clay motorcycle modelling. |
4 | September 2021 | Protolabs | Protolabs and RS components have been partnered to offer a new comprehensive 3D printing service. |
As the global automobile industry shifts away from internal combustion engines and toward electric cars, 3D printing emerges as a technology that can accelerate development and drastically alter the way we think about car component design.
Weight reduction has long been an aim in vehicles powered by combustion engines in order to reduce fuel usage and pollutants.
Reduced weight still plays a role in decreasing energy usage and hence extending driving range with a particular battery in electric vehicles. But there is another factor to consider. Several EV projects are leveraging 3D printing in research and manufacturing as of 2020.
The car sector was among the first to use 3D printing for fast prototyping. Automakers now see indirect (e.g., moulds) and direct part manufacture as the ultimate business model for AM. This shift in focus reflects an intriguing trend: OEMs in the automotive and 3D printing industries are moving toward digital mass manufacturing.
It has been widely employed in engineering, notably for prototype and producing lightweight designs, as well as in medical, education, architecture, and entertainment. Maker culture, enthusiasts and amateurs, tiny desktop printers, low-cost printing methods such as FDM, and low-cost materials like ABS and PLA are all widely linked with 3D printing.
The Global Automotive 3D Printing Market can be segmented into following categories for further analysis.
SI no | Timeline | Company | Developments |
1 | November 2021 | Bond3D | Dutch startup 3D printing company has showcased its void-free 3D printing technology to the world. |
2 | November 2021 | Vlare | Shenzhen-based 3D printing developer announced its new 3D printer control board-Core. |
3 | October 2021 | Automated Precision Inc(API) | US-based laser metrology device manufacturer has launched its new version of iSCAN3D 3D scanner. |
4 | October 2021 | UpNano | Two new resins for usage with its 2-photon polymerization(2PP) 3D printing technology have been developed by a Vienna-based manufacturer, UpNano. |
5 | September 2021 | Stratasys | Industrial 3D printer manufacturer has announced its new 3D printing materials for the Stratasys H350 and Stratasys Origin one systems. |
6 | September 2021 | Essentium | The manufacturer of High Speed Extrusion(HSE) 3D printer has launched the new Essentium PEKK 3D printing Filament. |
Companies and academic organisations alike are working hard to translate 3D printing into industrial, highly automated production methods for the automobile industry.
The increased collaboration is most seen in the number of initiatives that have lately been launched. As the globe approaches a new era of connected automobiles, the number of electronic equipment within the vehicle, such as sensors and antennas, is expanding. With this rise comes a larger requirement for smaller, more complicated devices to be designed and manufactured.
The developments in AM technologies for electronics open up the possibility of embedding these sensors directly into mechanical components and vehicle structures.
When compared to traditionally built sensors, this technique may result in improved reliability and a longer lifetime. There are distinct technologies inside each type of process, and for each unique technology, there are many different manufacturers offering identical printers.
Vat photopolymerization (particularly SLA technology), binder jetting (also known as FDM), and powder bed fusion are the most prevalent 3D printing techniques (specifically SLS technology).
With the release of the F190 CR and F370 CR machines, Stratasys has expanded its F123 Series of FDM 3D printers. The company has also introduced the new carbon fiber-reinforced FDM Nylon-CF10 material to go along with this announcement.
Manufacturers and industrial machinists can utilise the new composite 3D printers to create end-use components, as well as jigs, fixtures, and workholding tools. Both systems include GrabCAD Print software built in, as well as corporate application access via the MTConnect standard and GrabCAD Software Development Kit.
They also come with reusable build trays, a built-in camera for remote monitoring, and an auto-materials-changeover feature, which eliminates the need to interrupt builds to replace materials. Stratasys is supplying 3D printers and materials to manufacturers to promote the rise of additive manufacturing on the factory floor, including these new printers that allow businesses to make stronger, stiffer, and more precise parts.
GrabCAD Print for the Stratasys Origin One and Origin One Dental 3D printing systems has also been released by Stratasys. Users will be able to use this platform to streamline their 3D printing workflows, including print build file preparation and post-print analysis.
GrabCAD Print integration is reported to be the first step toward fully integrating the Origin One into the GrabCAD Additive Manufacturing Platform.
AddCat, a Dutch firm, is working to commercialise a 3D-printed metal catalytic. These filters potentially outperform their conventional equivalents by optimising structure and flow. And, if the performance is adequate, the increased expenses often associated with additives may vanish.
AddCat is developing air purifying filters for volatile organic chemicals by combining 3D printing and the effects of catalytic oxidation (VOCs).
VOCs are easily dispersed and concentrated in indoor air, which might have long-term and negative health consequences. Over the years, there has been considerable concern that 3D printers may emit too many VOCs. Although sufficient air circulation per hour may be enough to assure occupant safety.
SI no | Timeline | Company | Sales |
1 | Q3-2021 | Ford Motor Company | The revenue at the end of third quarter is $33.2 billion and in 2020 the revenue was $34.7 billion. |
2 | Q3-2021 | General Motors | At the end of the third quarter, the revenue of GM is $26.7 billion and in 2020 the revenue is $35.4 billion. |
3 | Q2-2021 | Jaguar Land Rover | Jaguar Land Rover reached £3.9 billion at the end of Q2 ended in September 2021. |
The Global Automotive 3D Printing Market Industry has started to experience significant growth in terms of applying stronger criteria for sustainable design. For the past few decades, carmakers have mostly employed 3D printing in the automobile sector to manufacture vehicle prototypes to test its shape and fit. Prototyping is an extremely significant component of the production process in the automobile sector, as it is in many other sectors.
Porsche has unveiled a new idea for sports vehicle seats that makes use of 3D printing and lattice architecture. The new chairs have 3D-printed polyurethane central seat and backrest cushion parts that can be adjusted to three hardness levels: hard, medium, and soft.
The German carmaker is adopting lessons from the racing industry with its customised seats, where bespoke driver-specific seat fitting is the standard.
Porsche intends to 3D print 40 prototype seats for use on European race courses as early as May 2020, with customer input used to build the final street-legal models for release in mid-2021.
Cadillac's manual transmission models for 2022 will be GM's first vehicles to employ scale production 3D printing. The automobiles will include two 3-d - printed nylon HVAC ducts created with Multi Jet Fusion, an aluminium bracket created with powder bed fusion, and a stainless-steel emblem on the shift knob created using binder jetting.
The RD Limited racing team's off-road racing car for the 2021 Dakar Rally contains a bespoke gear lever and three titanium brake pedals 3D manufactured. The powder bed fusion method also allowed the researchers to improve the design of the car's exhaust ball joint, which is prone to breaking.
Sl no | Topic |
1 | Market Segmentation |
2 | Scope of the report |
3 | Abbreviations |
4 | Research Methodology |
5 | Executive Summary |
6 | Introduction |
7 | Insights from Industry stakeholders |
8 | Cost breakdown of Product by sub-components and average profit margin |
9 | Disruptive innovation in the Industry |
10 | Technology trends in the Industry |
11 | Consumer trends in the industry |
12 | Recent Production Milestones |
13 | Component Manufacturing in US, EU and China |
14 | COVID-19 impact on overall market |
15 | COVID-19 impact on Production of components |
16 | COVID-19 impact on Point of sale |
17 | Market Segmentation, Dynamics and Forecast by Geography, 2024-2030 |
18 | Market Segmentation, Dynamics and Forecast by Product Type, 2024-2030 |
19 | Market Segmentation, Dynamics and Forecast by Application, 2024-2030 |
20 | Market Segmentation, Dynamics and Forecast by End use, 2024-2030 |
21 | Product installation rate by OEM, 2023 |
22 | Incline/Decline in Average B-2-B selling price in past 5 years |
23 | Competition from substitute products |
24 | Gross margin and average profitability of suppliers |
25 | New product development in past 12 months |
26 | M&A in past 12 months |
27 | Growth strategy of leading players |
28 | Market share of vendors, 2023 |
29 | Company Profiles |
30 | Unmet needs and opportunity for new suppliers |
31 | Conclusion |
32 | Appendix |