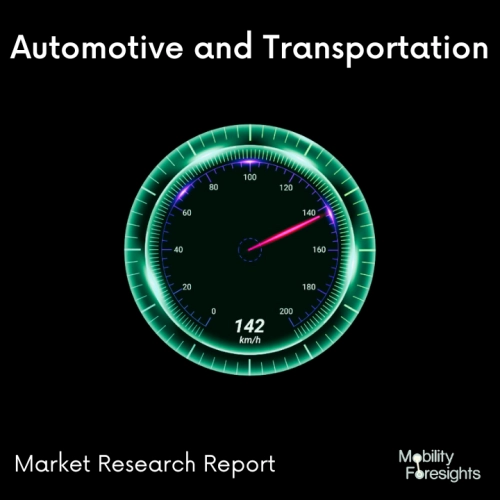
- Get in Touch with Us
Last Updated: Apr 25, 2025 | Study Period: 2023-2030
The intake-manifold injection system with suction engines or charged engines uses the natural gas injection valve NGI2 in civil vehicle applications. The intake manifold receives a natural gas injection at system pressure from the natural gas injection valve. The CNG fuel rail provides the injector for CNG systems.
The engine management system calculates a signal that the electronic control unit uses to initiate the injection. As a result, the engine receives an exact dose of gas.
The NGI2 was created expressly to satisfy the needs of CNG operation, and it functions as an electromagnetic valve with a bigger gas volume, a higher flow rate, and wear resistance even when used with oil-free gas. Its performance and lifespan can be comparable to that of fuel injectors.
Direct injection is not just for gasoline and diesel engines. It might also increase how economical and environmentally friendly cars are using compressed natural gas (CNG) engines. In comparison to current systems that employ manifold gas injection, it might generate up to 60% greater torque at low rpm and offer the possibility of an even more dynamic driving experience in the CNG cars of the future.
This would increase driving enjoyment. Natural gas cannot currently be directly injected into the combustion chamber because to technological limitations. Researchers are now working on a direct injection method for monovalent engines, or engines that only use CNG, as part of the Direct4Gas project.
The Global Automotive CNG injection system market accountedfor $XX Billion in 2022 and is anticipated to reach $XX Billion by 2030, registering a CAGR of XX% from 2023 to 2030.
For a demonstration project, a brand-new fuel system design for CNG engines with direct injection was created. The engine's cylinder head was modified during the development of the fuel system so that apertures for the fuel injector and spark plug were added. Additionally, the piston was altered to have a greater compression ratio.
The fuel rails and regulators are also made to work with the direct injection system when it is operating at 2.0 MPa or higher pressure. The Electronic Control Unit, which was specifically created for direct injectors as part of another group project, also controls the injection timing for these devices. After testing with various injection pressures and spray angles, the injectors are chosen.
Sl no | Topic |
1 | Market Segmentation |
2 | Scope of the report |
3 | Abbreviations |
4 | Research Methodology |
5 | Executive Summary |
6 | Introduction |
7 | Insights from Industry stakeholders |
8 | Cost breakdown of Product by sub-components and average profit margin |
9 | Disruptive innovation in the Industry |
10 | Technology trends in the Industry |
11 | Consumer trends in the industry |
12 | Recent Production Milestones |
13 | Component Manufacturing in US, EU and China |
14 | COVID-19 impact on overall market |
15 | COVID-19 impact on Production of components |
16 | COVID-19 impact on Point of sale |
17 | Market Segmentation, Dynamics and Forecast by Geography, 2023-2030 |
18 | Market Segmentation, Dynamics and Forecast by Product Type, 2023-2030 |
19 | Market Segmentation, Dynamics and Forecast by Application, 2023-2030 |
20 | Market Segmentation, Dynamics and Forecast by End use, 2023-2030 |
21 | Product installation rate by OEM, 2023 |
22 | Incline/Decline in Average B-2-B selling price in past 5 years |
23 | Competition from substitute products |
24 | Gross margin and average profitability of suppliers |
25 | New product development in past 12 months |
26 | M&A in past 12 months |
27 | Growth strategy of leading players |
28 | Market share of vendors, 2023 |
29 | Company Profiles |
30 | Unmet needs and opportunity for new suppliers |
31 | Conclusion |
32 | Appendix |