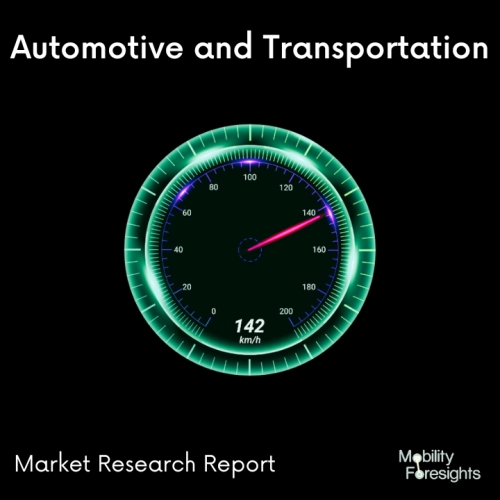
- Get in Touch with Us
Last Updated: Apr 25, 2025 | Study Period: 2023-2030
The automotive industry regularly uses the fabrication technique known as "hydroforming," also known as "counter-pressure forming." A unibody component structure with a high strength-to-weight ratio is produced via hydroforming, which enables the creation of complex geometries without the need to weld pieces together.
Some automakers produce components using the more conventional stamp and weld technique. To create suspension components, engine cradles, body frames, and other items, parts and panels are stamped out of steel sheets and joined together using welding.
In contrast, the hydroforming process employs pressure to press ductile metal into the shape of a die, which in some circumstances can be more effective in terms of cost and manufacturing time.
The Global Automotive Hydroformed Parts market accounted for $XX Billion in 2022 and is anticipated to reach $XX Billion by 2030, registering a CAGR of XX% from 2023 to 2030.
Governments in all the major nations have declared lockdowns and a number of other harsh measures in response to the COVID-19 outbreak. The pandemic has caused the automotive industry to shut down its factories, which has affected the need for hydroformed parts.
The pandemic has also decreased consumer spending, which has had a negative impact on the market for automotive hydroformed parts.
Additionally, curfews have been implemented since the outbreak in practically every country, allowing only a select group of people with permission to travel, which has led to a further fall in the sale of cars.
Furthermore, the lack of workforce has caused the production process to be delayed due to social distance standards and other restrictions.
Supply was also impacted by the shutdown since raw materials needed to produce hydroformed parts were unavailable. As a result, the COVID-19 pandemic had a detrimental impact on the market expansion for automobile hydroformed parts.
It is primarily employed in the production of sophisticated automotive components and lightweight automobiles in the automotive sector. In comparison to alternative techniques, hydroformed parts are more affordable, more robust, need less time to manufacture, are automated, and produce less waste.
With the help of this high-pressure water, a sheet is moulded into the desired shape in the die. Additionally, two die halves are used in tube hydroforming to expand the metal tubes in the appropriate shaper.
Sl no | Topic |
1 | Market Segmentation |
2 | Scope of the report |
3 | Abbreviations |
4 | Research Methodology |
5 | Executive Summary |
6 | Introduction |
7 | Insights from Industry stakeholders |
8 | Cost breakdown of Product by sub-components and average profit margin |
9 | Disruptive innovation in the Industry |
10 | Technology trends in the Industry |
11 | Consumer trends in the industry |
12 | Recent Production Milestones |
13 | Component Manufacturing in US, EU and China |
14 | COVID-19 impact on overall market |
15 | COVID-19 impact on Production of components |
16 | COVID-19 impact on Point of sale |
17 | Market Segmentation, Dynamics and Forecast by Geography, 2023-2030 |
18 | Market Segmentation, Dynamics and Forecast by Product Type, 2023-2030 |
19 | Market Segmentation, Dynamics and Forecast by Application, 2023-2030 |
20 | Market Segmentation, Dynamics and Forecast by End use, 2023-2030 |
21 | Product installation rate by OEM, 2023 |
22 | Incline/Decline in Average B-2-B selling price in past 5 years |
23 | Competition from substitute products |
24 | Gross margin and average profitability of suppliers |
25 | New product development in past 12 months |
26 | M&A in past 12 months |
27 | Growth strategy of leading players |
28 | Market share of vendors, 2023 |
29 | Company Profiles |
30 | Unmet needs and opportunity for new suppliers |
31 | Conclusion |
32 | Appendix |