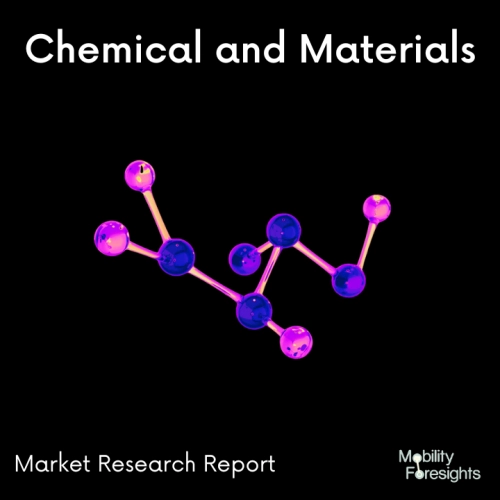
- Get in Touch with Us
Last Updated: Apr 25, 2025 | Study Period: 2024-2030
Since automotive encapsulants are significantly more adaptable than conventional epoxy mold compounds, they eliminate the requirement for costly molding plates and machines.
They make it possible for manufacturers to produce smaller, more adaptable batches, making the products ideal for a variety of low-quantity orders. LED encapsulation may also benefit from the use of optical grade encapsulants.
Encapsulants are mostly used to improve the mechanical strength of wire-bonded devices and protect the environment. They were designed to protect aluminum, wire bonds, and leads. For transistors, system in package (SIP) devices, ASICs, and chip-on-board applications, encapsulants provide unparalleled performance.
Utilizing glob tops can cut cycle time and expenses in half. For chip-on-board applications, these materials are designed to cure quickly, making it simple to work with high-speed manufacturing processes.
The Global Automotive Liquid Epoxy Encapsulant Material market accounted for $XX Billion in 2023 and is anticipated to reach $XX Billion by 2030, registering a CAGR of XX% from 2024 to 2030.
(Epoxy molding compound, or EMC) Shin-Etsu Chemical semiconductor encapsulation materials are made of epoxy and utilize a transfer molding system to make a variety of electronic components. They were created using cutting-edge technology that was developed through silicone's development.
Lead-based paint is sealed to a surface with encapsulants, which are substances that prevent paint chips or dust from escaping. The substance could be an adhesive or a liquid.
The most widely used encapsulant material is EVA, or ethyl vinyl acetate. Thin sheets of EVA are available, and they are inserted between the solar cells' top and rear surfaces. After that, the sandwich is heated to 150 °C to bond the module together and polymerize the EVA.
A membrane is applied to the surface by a bridging encapsulant. A penetrating encapsulant binds the material's components together by entering the material.
Formulation and testing of ultra motive encapsulants take place both during the manufacturing process and during the complete package assembly. They have been designed to provide outstanding performance in lead-free environments with high temperatures and meet the most stringent testing requirements at the JEDEC level.
There are a lot of liquid encapsulants available from Caplinq. We are pleased to offer both our own LinqSil and Optolinq products as well as all of Henkel's LOCTITE offerings.
Sl no | Topic |
1 | Market Segmentation |
2 | Scope of the report |
3 | Abbreviations |
4 | Research Methodology |
5 | Executive Summary |
6 | Introduction |
7 | Insights from Industry stakeholders |
8 | Cost breakdown of Product by sub-components and average profit margin |
9 | Disruptive innovation in the Industry |
10 | Technology trends in the Industry |
11 | Consumer trends in the industry |
12 | Recent Production Milestones |
13 | Component Manufacturing in US, EU and China |
14 | COVID-19 impact on overall market |
15 | COVID-19 impact on Production of components |
16 | COVID-19 impact on Point of sale |
17 | Market Segmentation, Dynamics and Forecast by Geography, 2024-2030 |
18 | Market Segmentation, Dynamics and Forecast by Product Type, 2024-2030 |
19 | Market Segmentation, Dynamics and Forecast by Application, 2024-2030 |
20 | Market Segmentation, Dynamics and Forecast by End use, 2024-2030 |
21 | Product installation rate by OEM, 2023 |
22 | Incline/Decline in Average B-2-B selling price in past 5 years |
23 | Competition from substitute products |
24 | Gross margin and average profitability of suppliers |
25 | New product development in past 12 months |
26 | M&A in past 12 months |
27 | Growth strategy of leading players |
28 | Market share of vendors, 2023 |
29 | Company Profiles |
30 | Unmet needs and opportunity for new suppliers |
31 | Conclusion |
32 | Appendix |