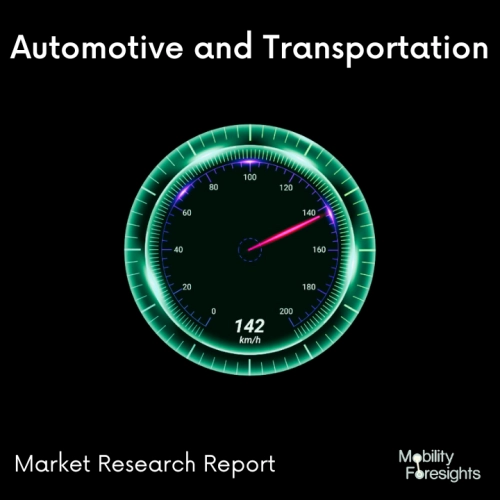
- Get in Touch with Us
Last Updated: Apr 25, 2025 | Study Period: 2023-2030
In addition to its basic function of producing dies, machining centres are essential tools for machining metal parts and components.
For instance, machining centres are utilised in the auto sector to efficiently drill and grind engine parts as well as create dies for body parts.
Machining centres produce a wide range of additional items that are frequently used in both industrial settings and day-to-day living.
A computerised automatic tool changing function is present in machining centres. On an NC machine tool, an operator typically needs to change the tools.
However, during the machining of workpieces, machining centres contain a change arm that automatically retrieves and switches out tools from a tool magazine.
This enables automated and power-saving operations while lowering costs because it saves the time and effort needed for standard tool changeovers.
In addition to using several complicated machining techniques including drilling, boring (enlarging holes), and threading, manufacturing metal products typically involves grinding surfaces and grooves.
Traditionally, various cutting tools like mills, end mills, drills, boring tools, and taps were employed for these machining procedures on a case-by-case basis.
Blade changing became more convenient with the subsequent development of NC lathes, which feature a turret, a manually driven tool change function.
Through automated tool exchanges that are computer-controlled, machining centres advance this concept. The efficiency of production is substantially increased by the ability of machining centres to constantly carry out many types of machining on various surfaces of a workpiece.
The Global automotive machining centre market accountedfor $XX Billion in 2021 and is anticipated to reach $XX Billion by 2030, registering a CAGR of XX% from 2022 to 2030.
A cutting-edge manufacturing tool is the CNC machine centre (also known as a CNC turning centre). Different machining operations can be carried out using machinery.
The CNC machine tool centre (also known as the machine centre) is a cutting-edge production tool that can carry out several machining operations with high quality, high precision, and high surface polish.
Drilling, milling, and turning operations can all be done with a CNC machine tool centre. The industry uses a variety of machining techniques, including milling, boring, drilling, tapping, and many more, to create prismatic parts, including gearboxes, partitions, frames, covers, etc.
The operation on many machine tools was able to generate a final product in the past, but it required dividing the production process into many working phases, which resulted in a lengthy delivery time and high cost.
A CNC machine tool centre was created to solve this issue. One machine may handle a wider range of machining needs by performing milling, lathing, and drilling operations on it.
Okuma America Corporation's executive team is eager to announce the introduction of a new double-column machining centre (DCMC).
The company's line-up of double-column machines now includes the MCR-BV, a brand-new machine. The MCR-BV was created as a tool for 5-face machining applications, but it may also be used for 5-axis contouring and 5-sided heavy milling.
Features include a strong integral motor and spindle, a larger work envelope, and an extremely sturdy table that is thicker than prior models, all of which are excellent for large-part machining, enabling these heavy-duty applications.
The machine is compatible with a large selection of attachment heads, enabling the creation of a wide variety of distinctive part shapes.
Sl no | Topic |
1 | Market Segmentation |
2 | Scope of the report |
3 | Abbreviations |
4 | Research Methodology |
5 | Executive Summary |
6 | Introduction |
7 | Insights from Industry stakeholders |
8 | Cost breakdown of Product by sub-components and average profit margin |
9 | Disruptive innovation in the Industry |
10 | Technology trends in the Industry |
11 | Consumer trends in the industry |
12 | Recent Production Milestones |
13 | Component Manufacturing in US, EU and China |
14 | COVID-19 impact on overall market |
15 | COVID-19 impact on Production of components |
16 | COVID-19 impact on Point of sale |
17 | Market Segmentation, Dynamics and Forecast by Geography, 2023-2030 |
18 | Market Segmentation, Dynamics and Forecast by Product Type, 2023-2030 |
19 | Market Segmentation, Dynamics and Forecast by Application, 2023-2030 |
20 | Market Segmentation, Dynamics and Forecast by End use, 2023-2030 |
21 | Product installation rate by OEM, 2023 |
22 | Incline/Decline in Average B-2-B selling price in past 5 years |
23 | Competition from substitute products |
24 | Gross margin and average profitability of suppliers |
25 | New product development in past 12 months |
26 | M&A in past 12 months |
27 | Growth strategy of leading players |
28 | Market share of vendors, 2023 |
29 | Company Profiles |
30 | Unmet needs and opportunity for new suppliers |
31 | Conclusion |
32 | Appendix |