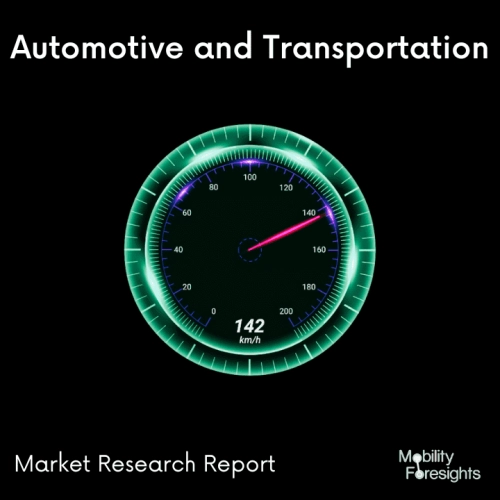
- Get in Touch with Us
Last Updated: Apr 25, 2025 | Study Period: 2024-2030
INTRODUCTION
The automotive metal market majorly comprised steel manufacturers in past decade, but now with growing emphasis on light-weighting and vehicle electrification, aluminium suppliers have a much bigger opportunity on their hands.
In developed markets of US and EU, a key trend in has been the development of the lightweight material to tackle the problem of high emission rates. Advanced high-strength steels (AHSS) are now used for nearly every new vehicle design. AHSS make up as much as 60% of todayâs vehicles body structures making lighter, optimised vehicle designs that enhance safety and improve fuel efficiency.
New grades of Advanced High-Strength Steels enable carmakers to reduce vehicle component weight by 25-39% and total vehicle weight by 8-10% compared to conventional steel. When applied to a typical five-passenger family car, the overall weight of the vehicle is reduced by 100-150 kg, which corresponds to a lifetime saving of 2-3 tonnes of greenhouse gases over the vehicleâs total life cycle.
Vehicle manufacturers are exploring the use of Aluminium, high-strength steel, magnesium, carbon-fiber composites, and other lightweight materials to reduce vehicle mass and improve fuel economy.
Significant time and investment is being made to develop high-strength components for applications ranging from car doors, electric battery enclosures and complete âbody in whiteâ (BiW) body shell for next-gen vehicles.
The average aluminum content of European manufactured cars has now reached more than 170kg in 2019.
The global trend of light weight substitution will be major growth driver in automotive metal market size. The global automotive metal market size was estimated at $XX Billion in 2021 growing at --% CAGR till 2026.
Eaton, the world's largest power management company, is increasing its 3D printing commitment by launching a new metal 3D printing programme through its Vehicle Group. The programme aims to increase the company's productivity while also reducing development timelines. The company's first metal 3D printer was placed in Kings Mountain, N.C., with plans to roll out polymer 3D printing across the board.
Consulting with GE Additive's AddWorks on how to use metal additive manufacturing in its aircraft operations was part of the agreement. Eaton has also looked into 3D printing sand moulds through a partnership with Bremen Castings, Inc. Airbus parts are already being 3D printed by the company.
Metal and polymer 3D printers are already in use within the Vehicle Group for tooling applications like poke-yokes and gauges. This latest statement demonstrates the company's continued commitment to the technology.
Eaton will use additive manufacturing to create fixtures, safety devices, robotic grippers for assembly and handling, and replacement components for equipment under its Vehicle Group. Eaton intends to employ 3D scanning to reverse engineer items that can then be improved using 3D printing techniques including topology optimization and part consolidation.
The Automotive Transportation Group (ATG) of the Aluminum Association has announced its 2022 Roadmap for Automotive Aluminum, which outlines short- mid and long-term R&D goals in support of automotive customers. The roadmap identifies and prioritises essential collaboration opportunities among aluminium suppliers, recyclers, automakers, policymakers, non-governmental organisations, and other industry players in order to stimulate innovation over the next decade.
The automobile industry is undergoing tectonic transformations in design, propulsion, materials, and manufacturability, ranging from electric vehicles and linked cars to autonomous technologies and supplier sustainability. To fulfil the demands of the market, the aluminium sector is preparing to release the most advanced automobile alloys and product designs ever created.
This technology roadmap outlines where the firm is now, where we're going, and the particular pathways and objectives that will let automakers envisage cars and trucks that are much superior to anything on the road now to fulfil consumer needs in the next decade and beyond.
The Aluminum Association brought together industry stakeholders to define and solve present obstacles, agree on goals, and develop technical pathways to reach those goals in five important areas in an era of rapid electrification.
The increasing usage of lightweight materials has been one of the largest changes in the automotive industry. A growing number of American automakers, including Ford, are employing lightweight metals to reduce the weight of their vehicles and, as a result, improve the fuel economy in order to comply with government pollution rules.
Aluminum is currently second to steel as the material that is utilized the most in the design of automobiles, according to this American Metals Market (AMM) article.
AMM claims that the usage of aluminum is expanding because it is a quick, safe, eco-friendly, and economical option to enhance performance, increase fuel economy, and lower emissions. Important aluminum suppliers like Alcoa have benefited from this development and anticipate further expansion on a worldwide basis.
Metals specialists believe that magnesium alloys will eventually play a role in the development of lightweight automobiles, despite the fact that they haven't garnered nearly as much attention as aluminum.
When using aluminum instead of steel, one experiences a weight reduction of about 40%. A comparative weight reduction greater than aluminum is achieved when using magnesium alloys in place of aluminum.
The Key players in the Automotive Metal and Light Weight Metals include Covestro AG (Germany), LyondellBasell Industries Holdings BV (Netherlands), Toray Industries Inc. (Japan), ArcelorMittal (Luxembourg), Thyssenkrupp AG (Germany), Novelis Inc. (US), Tata Steel (India), Jindal Steel(India) and the Alcoa Corporation (US).
With the development on a new R&D facility being implemented under AK Steel Holding Corporation, it has been determined and developed to focus on the aspects of new alloy combinations.
There has been extensive research being planned to have a proper source of lightweight metal progression and innovation which would satisfy the requirements down the lane to almost 15 years of production line manufacturing operations and consumer requirements.
Constellium- a leading European aluminium supplier derives ~25% of its annual sales from auto industry and is supplying to BMW and Daimler. It has also launched two new automotive Structureâs facilities in 2019, located in Vigo, Spain, and Nanjing, China.
Novelis is actively targeting BEV market, it has developed a new aluminium sheet battery enclosure solution for BEVs. The enclosure made of highly formable aluminium alloys is up to 50% lighter than an equivalent steel design allows 6-7% extra range per full charge.
Among Asian suppliers, Tata Steel developed DP1000HY-GI, a high-yield, ultra-high strength steel in 2014 product which allowed manufacturers to make lighter components without altering their production facilities. In the same year, it also introduced a new suite of hot-rolled sheet steel products aimed at helping OEMs reduce the weight of undercarriage.
Sl no | Topic |
1 | Market Segmentation |
2 | Scope of the report |
3 | Abbreviations |
4 | Research Methodology |
5 | Executive Summary |
6 | Introduction |
7 | Insights from Industry stakeholders |
8 | Cost breakdown of Product by sub-components and average profit margin |
9 | Disruptive innovation in the Industry |
10 | Technology trends in the Industry |
11 | Consumer trends in the industry |
12 | Recent Production Milestones |
13 | Component Manufacturing in US, EU and China |
14 | COVID-19 impact on overall market |
15 | COVID-19 impact on Production of components |
16 | COVID-19 impact on Point of sale |
17 | Market Segmentation, Dynamics and Forecast by Geography, 2024-2030 |
18 | Market Segmentation, Dynamics and Forecast by Product Type, 2024-2030 |
19 | Market Segmentation, Dynamics and Forecast by Application, 2024-2030 |
20 | Market Segmentation, Dynamics and Forecast by End use, 2024-2030 |
21 | Product installation rate by OEM, 2023 |
22 | Incline/Decline in Average B-2-B selling price in past 5 years |
23 | Competition from substitute products |
24 | Gross margin and average profitability of suppliers |
25 | New product development in past 12 months |
26 | M&A in past 12 months |
27 | Growth strategy of leading players |
28 | Market share of vendors, 2023 |
29 | Company Profiles |
30 | Unmet needs and opportunity for new suppliers |
31 | Conclusion |
32 | Appendix |