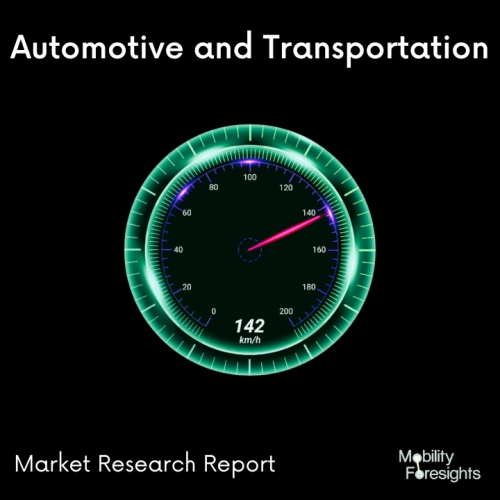
- Get in Touch with Us
Last Updated: Apr 25, 2025 | Study Period: 2023-2030
Additionally known as AC Drives or VFDs, inverters (variable frequency drive). They are electrical devices that convert direct current (DC) to alternating current (AC) (Alternating Current). Additionally, it is in charge of regulating the speed and torque of electric motors.
Using a power inverter while driving is doable! In fact, since a power inverter would deplete your car's battery, it could be better for your vehicle than operating the inverter when stationary.
Inverters are separated into two primary groups based on the output voltage and current phases. Both three-phase and single-phase inverters.
The inverter provides electricity to the rear motor that powers the rear wheels of four-wheel drive (4WD) vehicles. High flexibility in vehicle installation has been made possible by the deployment of a forced air-cooling system to cool the heat-generating components as well as the decrease in size and weight. Home, Products.
An inverter regulates the frequency of electricity sent to an AC motor in order to regulate the motor's rotational speed. Without an inverter, the moment the power source was turned ON, the AC motor would begin to run at full speed. The uses for the motor would be restricted because you wouldn't be able to alter the speed.
The Global Automotive Rear Drive Inverter market accounted for $XX Billion in 2022 and is anticipated to reach $XX Billion by 2030, registering a CAGR of XX% from 2023 to 2030.
SiC power modules for EV traction inverters are now available from Infineon.
A new vehicle power module from Infineon Technologies is based on the well-established, leading CoolSiC MOSFET technology. A six-pack full-bridge module with 1200 V blocking voltage is part of the HybridPACK Drive CoolSiC and is designed specifically for traction inverters in electric cars (EV).
The power module is able to achieve high-power density in high-performance applications while retaining a high level of reliability since it is based on Infineon's CoolSiC trench MOSFET technology.
This cutting-edge power source is approved for use in automotive applications and is especially well suited for EV inverters, particularly for vehicles with 800-V battery systems and higher battery capacity. It provides easier power scaling for conventional silicon-based systems together with improved efficiency, longer ranges, and reduced battery prices.
Silicon carbide, which is used in EV traction inverters, has proven to provide a longer range and more effective drive cycle performance. HybridPACK power modules may be simply included into the design of an electric car, as depicted, which alludes to a four-wheel drive arrangement.
A HybridPACK Drive CoolSiC MOSFET, an unique device that can give a greater range or, alternatively, can reduce the battery capacity for the same range, can be installed in the back axle. This innovation helps lower system costs. However, there is a method for the two technologies to coexist in the same application. As can be seen, silicon carbide is not meant to totally replace silicon.
A HybridPACK Drive CoolSiC MOSFET, an unique device that can give a greater range or, alternatively, can reduce the battery capacity for the same range, can be installed in the back axle. This innovation helps lower system costs. The two technologies may coexist in the same application, as seen in Figure 1, even if silicon carbide is not meant to totally replace silicon.
An HybridPACK Drive IGBT is put on the front axle in the example setup, providing the "on-demand" all-wheel drive system with the ideal solution. Only the rear axle is powered during regular driving circumstances.
A traction control mechanism sends torque also to the front axle if a wheel slide is detected. This occurs in most cars between 5% and 10% of the time, therefore an IGBT solution based on silicon helps keep prices down.
Therefore, use IGBT and SiC technologies on the two axles of the same vehicle, each with a unique set of performance characteristics. When efficiency is the primary consideration, silicon carbide is preferred over silicon, which is utilised when maximum performance at the lowest cost is required.
Sl no | Topic |
1 | Market Segmentation |
2 | Scope of the report |
3 | Abbreviations |
4 | Research Methodology |
5 | Executive Summary |
6 | Introduction |
7 | Insights from Industry stakeholders |
8 | Cost breakdown of Product by sub-components and average profit margin |
9 | Disruptive innovation in the Industry |
10 | Technology trends in the Industry |
11 | Consumer trends in the industry |
12 | Recent Production Milestones |
13 | Component Manufacturing in US, EU and China |
14 | COVID-19 impact on overall market |
15 | COVID-19 impact on Production of components |
16 | COVID-19 impact on Point of sale |
17 | Market Segmentation, Dynamics and Forecast by Geography, 2023-2030 |
18 | Market Segmentation, Dynamics and Forecast by Product Type, 2023-2030 |
19 | Market Segmentation, Dynamics and Forecast by Application, 2023-2030 |
20 | Market Segmentation, Dynamics and Forecast by End use, 2023-2030 |
21 | Product installation rate by OEM, 2023 |
22 | Incline/Decline in Average B-2-B selling price in past 5 years |
23 | Competition from substitute products |
24 | Gross margin and average profitability of suppliers |
25 | New product development in past 12 months |
26 | M&A in past 12 months |
27 | Growth strategy of leading players |
28 | Market share of vendors, 2023 |
29 | Company Profiles |
30 | Unmet needs and opportunity for new suppliers |
31 | Conclusion |
32 | Appendix |