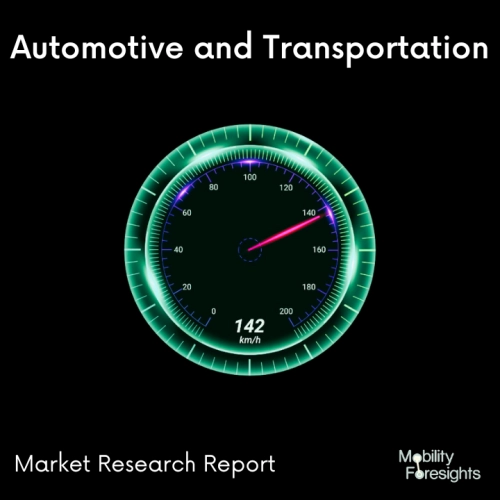
- Get in Touch with Us
Last Updated: Apr 25, 2025 | Study Period: 2023-2030
The damping force of the shock absorber is controlled by a type of automobile suspension system called semi-active suspension in response to information from the constantly changing road surfaces.
Suspension parts may be divided into three categories: linkages, springs, and shock absorbers. The bars and brackets that support the wheels, springs, and shock absorbers are known as links.
One kind of automotive suspension for a vehicle is an active suspension. In contrast to passive suspension provided by huge springs, where the movement is totally dependent on the road surface, it employs an onboard mechanism to regulate the vertical movement of the vehicle's wheels in relation to the chassis or vehicle body.
Between the frame and the road, a vehicle's suspension system is located. The main goal of a vehicle's suspension system is to improve overall performance as it travels along the road. Additionally, the suspension system contributes to a safe and comfortable ride by absorbing road imperfections.
The major duties of the suspension system are to maximise tire-road contact, provide steering stability and excellent handling, uniformly distribute the vehicle's weight (including the frame, engine, and body), and provide passenger comfort by absorbing and damping road shock.
The Global Automotive Semi-active suspension system market accounted for $XX Billion in 2022 and is anticipated to reach $XX Billion by 2030, registering a CAGR of XX% from 2023 to 2030.
For racing vehicles, a New Semi-Active Suspension System.
The major objective is to create a simple, compact variable geometry suspension system that uses less energy to operate, can be installed without requiring significant modifications to the passive suspension system's original design through retrofitting operations. The apparatus will be used on a car whose geometry was influenced by an open-wheel racing car with push-rod suspension.
Kinematic analysis was used to analyse the suspension system's geometry and kinematic characteristics, which was then followed by CAD modelling and a dynamic analysis.
Semi-active suspensions make it possible to achieve a fair balance between performance and prices, producing results that are on par with those of active suspensions while using less energy to operate. Variable geometry suspensions also provide advantages over other variable geometry options, such as a built-in fail-safe behaviour.
Sl no | Topic |
1 | Market Segmentation |
2 | Scope of the report |
3 | Abbreviations |
4 | Research Methodology |
5 | Executive Summary |
6 | Introduction |
7 | Insights from Industry stakeholders |
8 | Cost breakdown of Product by sub-components and average profit margin |
9 | Disruptive innovation in the Industry |
10 | Technology trends in the Industry |
11 | Consumer trends in the industry |
12 | Recent Production Milestones |
13 | Component Manufacturing in US, EU and China |
14 | COVID-19 impact on overall market |
15 | COVID-19 impact on Production of components |
16 | COVID-19 impact on Point of sale |
17 | Market Segmentation, Dynamics and Forecast by Geography, 2023-2030 |
18 | Market Segmentation, Dynamics and Forecast by Product Type, 2023-2030 |
19 | Market Segmentation, Dynamics and Forecast by Application, 2023-2030 |
20 | Market Segmentation, Dynamics and Forecast by End use, 2023-2030 |
21 | Product installation rate by OEM, 2023 |
22 | Incline/Decline in Average B-2-B selling price in past 5 years |
23 | Competition from substitute products |
24 | Gross margin and average profitability of suppliers |
25 | New product development in past 12 months |
26 | M&A in past 12 months |
27 | Growth strategy of leading players |
28 | Market share of vendors, 2023 |
29 | Company Profiles |
30 | Unmet needs and opportunity for new suppliers |
31 | Conclusion |
32 | Appendix |