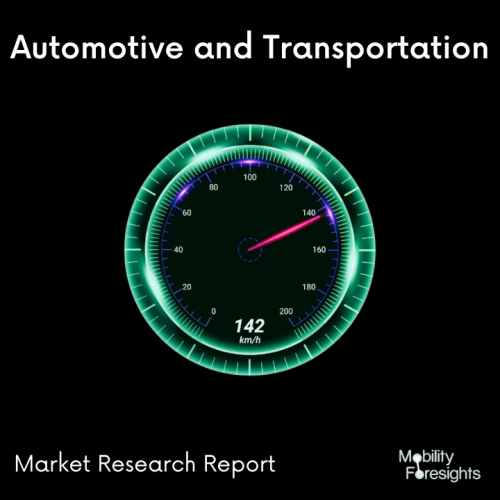
- Get in Touch with Us
Last Updated: Apr 25, 2025 | Study Period: 2024-2030
Structural metal sheets are used in the manufacture of interior and exterior automotive components.
The demand for interior and exterior components develops in tandem with the desire for luxury in cars. The metal sheet used to provide structure to automobiles is referred to as automotive structural sheet metal.
Sheet metal is metal that has been transformed into sheets via a number of industrial processes. Metal sheet is cut or twisted into various shapes to build various structures.
Aluminium, titanium, brass, stainless steel, and copper are among the materials used in the construction of various interior and exterior components of cars.
Another important market trend that is projected to boost demand is weight reduction in vehicles, with manufacturers choosing lightweight materials to cut emission rates.
The power of competition has risen as major vehicle manufacturers and suppliers compete on a worldwide basis.
The metal sheet is cut or twisted into numerous shapes to assemble various buildings. Some of the materials used to make the inside and external features of vehicles include aluminium, titanium, metal, treated steel, and copper.
The body construction of every car is the most crucial component. The body of a vehicle connects all of its components; it houses the drive train and, most importantly, it carries and protects people and things.
The body structure must be strong enough to withstand weight and stress while also securely connecting all of the components.
The demand for facade components develops in parallel with the quest for elegance in automobiles. Increased component demand needs the usage of more metal sheets, which will result in the rise of the automotive structural sheet metal market in the near future.
There are three varieties of sheet metal: mild steel, aluminium, and stainless steel. Aluminium and mild steel are by far the most common materials used in automotive applications.
Sheet metal fabricators use aluminium for dashboards, bulkheads, and most other applications because it is light, soft, and easy to work with.
In non-industrial nations, structural sheet metals are receiving relentless interest as a result of rising automobile ownership and significant financial flows.
The rising per capita income and concomitant boom in car sales may potentially create excellent prospects in new sectors for the primary sheet metal business.
The mass production of automobiles may potentially play an important role in the global market's rise.
Rising automobile sales and strong demand for metal sheets for creating interior and exterior components are key drivers driving the global automotive structural sheet metal market.
However, raw material and trade prices are volatile. Vehicle weight reduction is a relatively new phenomena.
The increasing usage of lightweight metal components with high explicit strength and low width is also gaining popularity among automakers.
Mechanical advances in basic sheet metal assembly, such as the introduction of processes and half electromagnetically assisted sheet metal met
The Global Automotive Structural Sheet Metal Market can be segmented into following categories for further analysis.
In automobile engineering, materials and tactics for lowering vehicle weight are prevalent. Large weight reductions while maintaining vehicle utility, safety, performance, ride, and handling are commonly considered to demand drastic changes, such as the all-aluminum bodywork or carbon-fibre composites seen in concept automobiles.
While these materials are now used selectively and are projected to be used more widely in the future, it is vital to be aware of the enormous, near-term possibilities arising from continual breakthroughs in less expensive, established materials and design techniques.
These current technologies, which use engineered plastics and light metals in addition to steel and iron, give strategies for gradually reducing weight while keeping or enhancing other attributes, and can do so at a low or even zero cost.
Improved iron and steel technology has advanced greatly over the previous decade and is now frequently employed in all manufacturers' new designs and redesigns.
The breadth of sheet metal work for automotive applications is expanding thanks to computer simulation. Many current metal forming methods are based on a deep understanding of the crystallites of various metals, as well as the physical processes that take place inside metal when it is subjected to pressure and heat.
Some of the new methods are hybrids of old ones. A trend toward hot-metal procedures has also occurred, permitting the use of metals that would not be suitable for cold processes.
These new technologies allow for advancements such as the usage of lighter metals while preserving the strength of standard automobile parts.
This is critical in the manufacture of fuel-efficient autos or battery-electric vehicles, for example. Electromagnetic forming techniques, for example, where the metal product is exposed to a magnetic field that generates an electric flow in the metal itself, can be utilised to speed up the forming process while avoiding the typical tearing and wrinkling.
The usage of alternatives in automobiles, such as fibre and plastic composite parts, may potentially be a worldwide development limiting factor.
Because of the rising interest in self-sufficient, versatile administrations, digitalization, and electric powertrains and driving in the vehicle business worldwide, the car primary sheet metal sector will rush to recover.
With the rising desire for luxury in automobiles and the need for interior and exterior elements, structural metal sheets are being utilized to fabricate interior and external vehicle components.
Increased demand for parts demands the employment of more metal sheets, which leads to the progress of the car's basic structure.
BlueScope Australia is one of the most recent innovations in the market for automotive sheet metal requirements. The Ultralight Steel Auto Body (ULSAB) project indicates the potential viability of steel in automotive body manufacture.
ULSAB is a lighter, stronger automotive body construction that improves fuel efficiency while costing no more to build than conventional automobile body structures.
The steel body construction of the ULSAB weighs just 203kg, which is 25% lighter than the average benchmarked during the project's concept phase.
Porsche Engineering Services, based in Michigan, USA, was in charge of ULSAB design and production management. Porsche's goal was to gain a significant amount of weight.
In the worldwide scale of manufacturing, Nucor Corporation is also a part of the sheet metal market requirements. At Nucor's sheet mill in Crawfordsville, Indiana, we pioneered EAF thin-slab casting.
Since this achievement, we have remained the market leader by investing in exceptional sheet steel goods and technology. Steel sheet is rolled to its final thickness at high temperatures on a hot-rolling mill.
Pickling and oiling, a process of eliminating surface oxides and applying an oil to improve lubricity and a more rust-resistant product, can be used to further this operation. Surestride floor plates are hot rolled and have a raised lug pattern for safe walking and working.
Castrip is a Nucor-exclusive Ultra-thin Cast Steel (UCS) product, may be utilised in a variety of applications, replacing both hot-rolled and cold-rolled sheet. This is available in hot-rolled, pickled, and oiled, and galvanised forms.
The automotive structural sheet metal market is expanding as a result of the present focus on mobility services, autonomous driving, digitization, and electric powertrains, which are reshaping the automobile industry.
Additionally, the market for structural sheet metal for the automotive sector has grown significantly over the past several years, mostly as a result of rising car ownership and the expanding global automotive industry.
The market has grown because emerging nations have seen a sharp increase in the ownership of cars. The market has expanded due to the trend of weight reduction because of its high specific strength and low density.
Additionally, technological advancements in the production of structural sheet metals, such as hybrid electromagnetically assisted sheet metal stamping machines and coining processes, also had a favourable impact.
The creation of such components is now economically possible and the preferred option of car manufacturers due to advancements in the manufacturing of structural sheet metal components.
There is also a demand for lightweight structural sheets as a result of strict regulatory rules relating to emission standards and environmental concerns.
The market for structural sheet metal for the automotive industry is, on the other hand, significantly constrained by the fluctuating price of steel and aluminium.
The market for automotive structural sheet metal is likely to see growing challenges from replacements such as the use of plastic and fibre composite components in automobiles.
Increased sales of automobiles and the strong need for metal sheets for building interior and exterior components are the main factors influencing the growth of the worldwide automotive structural sheet metal market.
But the fluctuating price of raw materials and trade restrictions restrain the development of the worldwide automotive structural sheet metal market.
However, the global market for structural sheet metal for the automotive industry will be driven by new innovations and rising luxury vehicle demand.
Vehicle interior and exterior components are constructed using structural metal sheets. Demand for interior and exterior parts rises as luxury in automobiles becomes more and more in demand.
In the not too distant future, the market for automotive structural sheet metal will expand as a result of rising component demand requiring additional metal sheets. The framework of the vehicles is provided by steel.
Metal sheets are needed in greater quantities as more automobiles are manufactured.
As a result, the market for automotive structural sheet metal is seeing growth due to the increasing demand for automobiles and the consequent need for additional metallic structures.
Thus, in the near future, the market for automobile structural sheet metal will expand.
Metal sheet, which is useful for giving vehicles structure, is the subject of automotive structural sheet metal. The term "sheet metal" refers to metal that has undergone numerous industrial processes to become sheets.
1 | Market Segmentation |
2 | Scope of the report |
3 | Abbreviations |
4 | Research Methodology |
5 | Executive Summary |
6 | Introduction |
7 | Insights from Industry stakeholders |
8 | Cost breakdown of Product by sub-components and average profit margin |
9 | Disruptive innovation in the Industry |
10 | Technology trends in the Industry |
11 | Consumer trends in the industry |
12 | Recent Production Milestones |
13 | Component Manufacturing in US, EU and China |
14 | COVID-19 impact on overall market |
15 | COVID-19 impact on Production of components |
16 | COVID-19 impact on Point of sale |
17 | Market Segmentation, Dynamics and Forecast by Geography, 2024-2030 |
18 | Market Segmentation, Dynamics and Forecast by Product Type, 2024-2030 |
19 | Market Segmentation, Dynamics and Forecast by Application, 2024-2030 |
20 | Market Segmentation, Dynamics and Forecast by End use, 2024-2030 |
21 | Product installation rate by OEM, 2023 |
22 | Incline/Decline in Average B-2-B selling price in past 5 years |
23 | Competition from substitute products |
24 | Gross margin and average profitability of suppliers |
25 | New product development in past 12 months |
26 | M&A in past 12 months |
27 | Growth strategy of leading players |
28 | Market share of vendors, 2023 |
29 | Company Profiles |
30 | Unmet needs and opportunity for new suppliers |
31 | Conclusion |
32 | Appendix |