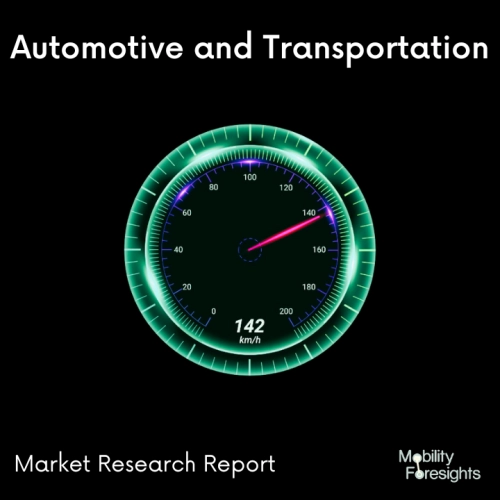
- Get in Touch with Us
Last Updated: Apr 25, 2025 | Study Period: 2023-2030
Printed circuit boards with high-density interconnect, or HDI, have more wiring per unit space than conventional printed circuit boards. Microvias, blind and buried vias, built-up laminations, and high signal performance considerations are generally considered to be HDI PCBs. The development of printed circuit boards has kept pace with the need for smaller and faster products as technology has changed.
The vias, pads, copper traces, and gaps on HDI boards are all smaller. Since HDIs have denser wiring, their PCBs are smaller, lighter, and have fewer layers. One HDI board can replace the functionality of several PCBs that were previously used in a device.
The Global Automotive ultra-HDI PCB market accounted for $XX Billion in 2021 and is anticipated to reach $XX Billion by 2030, registering a CAGR of XX% from 2022 to 2030.
Ultra HDI PCBs put high demands on technology and manufacturing. A strong tendency toward miniaturisation may be seen in the electronics industry. As components become smaller and smaller, new requirements are placed on the design of the PCBs that they are installed on. NCAB Group is fully dedicated to IPC's efforts to create standards for extremely dense Ultra HDI PCBs and will be able to provide clients with these products as a result.
NCAB receives requests on a daily basis about printed circuit boards with smaller conductor widths and isolation distances than normal HDI boards.
The extremely downsized new components have been employed, among other things, in 5G telecommunications technology, sensors, and high-end smartphones from major manufacturers.
We are now seeing the technology spread to other sectors of the industry. NCAB receives requests on a daily basis about printed circuit boards with smaller conductor widths and isolation distances than normal HDI boards. Medical technology and the automotive sector are two examples of applications.
The pattern must be able to be transferred on the board with a resolution that is high enough to accommodate the increasing level of miniaturisation. The factory must own state-of-the-art so-called LDI equipment (Laser Direct Imaging).
To eliminate contamination and dust, the surroundings must also be exceedingly clean, which requires a substantial expenditure. To identify and prevent any board flaws, testing procedures and automated optical inspection (AOI) tools must be updated. When copper plating, you must also consider the machinery and chemistry. Additionally, the requirement for cleaner and more uniform materials will result from miniaturisation.
Sl no | Topic |
1 | Market Segmentation |
2 | Scope of the report |
3 | Abbreviations |
4 | Research Methodology |
5 | Executive Summary |
6 | Introduction |
7 | Insights from Industry stakeholders |
8 | Cost breakdown of Product by sub-components and average profit margin |
9 | Disruptive innovation in the Industry |
10 | Technology trends in the Industry |
11 | Consumer trends in the industry |
12 | Recent Production Milestones |
13 | Component Manufacturing in US, EU and China |
14 | COVID-19 impact on overall market |
15 | COVID-19 impact on Production of components |
16 | COVID-19 impact on Point of sale |
17 | Market Segmentation, Dynamics and Forecast by Geography, 2023-2030 |
18 | Market Segmentation, Dynamics and Forecast by Product Type, 2023-2030 |
19 | Market Segmentation, Dynamics and Forecast by Application, 2023-2030 |
20 | Market Segmentation, Dynamics and Forecast by End use, 2023-2030 |
21 | Product installation rate by OEM, 2023 |
22 | Incline/Decline in Average B-2-B selling price in past 5 years |
23 | Competition from substitute products |
24 | Gross margin and average profitability of suppliers |
25 | New product development in past 12 months |
26 | M&A in past 12 months |
27 | Growth strategy of leading players |
28 | Market share of vendors, 2023 |
29 | Company Profiles |
30 | Unmet needs and opportunity for new suppliers |
31 | Conclusion |
32 | Appendix |