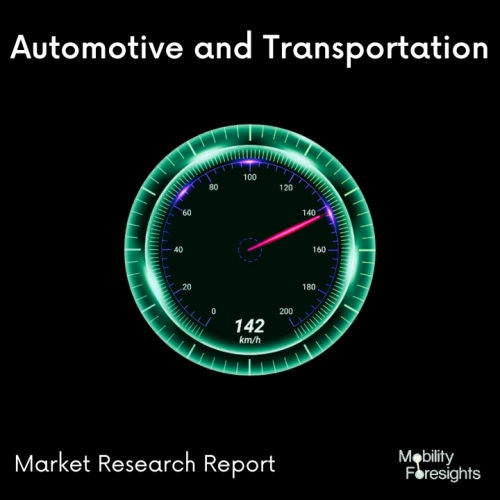
- Get in Touch with Us
Last Updated: Apr 25, 2025 | Study Period: 2024-2030
For different types of automated transmissions, variable-force transmission solenoids (VTS). The VTS adjusts the switching pressure, switches the lock-up clutch, and aids the safety functions in automatic-shift gearboxes.The flow of transmission fluid is managed by a transmission shift solenoid.
This is accomplished by a module that transmits an electrical signal instructing the shift solenoid precisely when and at what rate to transfer fluid into and out of the transmission.
An electro-hydraulic device called a variable force solenoid (VFS) regulates pressure either proportionately or inversely proportionally to a signal (voltage or current) supplied from the powertrain's on-board controller. When applying clutches or controlling transmission line pressure, a low flow VFS is employed as a signal level device.
A high flow VFS is utilised to directly control shift clutch or control line pressure. A specific kind of transmission solenoid is a VFS. It is possible to employ one or more VFS in an automatic transmission or instal them in the valve body of an automatic gearbox.
The Global Automotive variable-force transmission solenoid (VTS) market accounted for $XX Billion in 2023 and is anticipated to reach $XX Billion by 2030, registering a CAGR of XX% from 2024 to 2030.
Wheeled vehicles have some advantages over tracked vehicles, including quick acceleration, high mobility, extended operating distance, low cost, and ease of maintenance, but they also have several disadvantages, including a lack of cross-country power and a big turning radius. Military vehicles with tracks typically include tanks and armoured automobiles.
The most common sort of civilian vehicle is one with wheels (e.g. cars and trucks). A crucial part of wheeled vehicles is the automatic transmission (AT), which serves as the AT for gear shifts or pressure adjustments while the engine is running. Currently, automatic gearboxes with electronic control are used in AT vehicles with automatic shifting (ECAT).
This type of AT can use several sensors to tell the driving computer of the engine's operational status.This type of AT can employ a variety of sensors to communicate the engine's operating status to the driving computer.
The driving computer then sends signals to activate a variety of solenoids in the hydraulic control system to change the oil duct in the AT and regulate the gears or adjust the pressure. The solenoids of the ECAT can control the shift points, clutch locking, or line pressure.
Currently, numerous solenoid testers have been created to increase inspection efficiency. 9â15 The solenoid anomaly inspection capability is obviously inadequate as only one channel solenoid can be tested at a time, and the inspection efficiency is constrained.
Current test systems, on the other hand, primarily use the difference between the test hydraulic pressure curve and normal hydraulic pressure curve as the basis for determining whether or not the solenoid is normal. An AT solenoid can really be broken down into an electromagnetic structure and a mechanical valve body structure, and failures can occur in either one of these structures.
Sl no | Topic |
1 | Market Segmentation |
2 | Scope of the report |
3 | Abbreviations |
4 | Research Methodology |
5 | Executive Summary |
6 | Introduction |
7 | Insights from Industry stakeholders |
8 | Cost breakdown of Product by sub-components and average profit margin |
9 | Disruptive innovation in the Industry |
10 | Technology trends in the Industry |
11 | Consumer trends in the industry |
12 | Recent Production Milestones |
13 | Component Manufacturing in US, EU and China |
14 | COVID-19 impact on overall market |
15 | COVID-19 impact on Production of components |
16 | COVID-19 impact on Point of sale |
17 | Market Segmentation, Dynamics and Forecast by Geography, 2024-2030 |
18 | Market Segmentation, Dynamics and Forecast by Product Type, 2024-2030 |
19 | Market Segmentation, Dynamics and Forecast by Application, 2024-2030 |
20 | Market Segmentation, Dynamics and Forecast by End use, 2024-2030 |
21 | Product installation rate by OEM, 2023 |
22 | Incline/Decline in Average B-2-B selling price in past 5 years |
23 | Competition from substitute products |
24 | Gross margin and average profitability of suppliers |
25 | New product development in past 12 months |
26 | M&A in past 12 months |
27 | Growth strategy of leading players |
28 | Market share of vendors, 2023 |
29 | Company Profiles |
30 | Unmet needs and opportunity for new suppliers |
31 | Conclusion |
32 | Appendix |