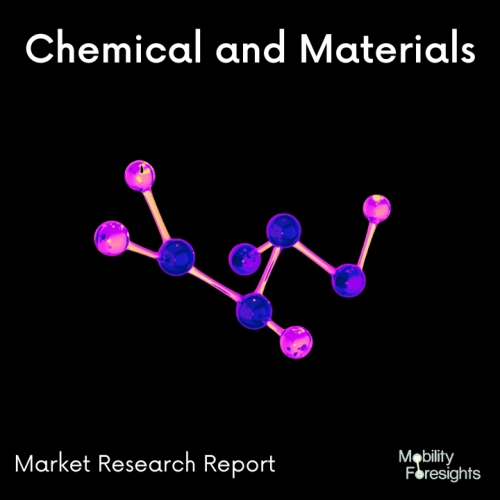
- Get in Touch with Us
Last Updated: Apr 25, 2025 | Study Period: 2024-2030
The bio-based conductive ink incorporates carbon nanotubes and cellulosic fibers, as well as furanic resin, which meets the carbonization requirements for printable conductive inks.The rheological behaviour of the bio-ink was optimised by creating various ink formulations. The innovative bio-printability ink's and electrical conductivity were enhanced.
The majority of research has concentrated on creating highly conductive inks for direct ink extrusion 3D printing, which involves pushing pasty ink materials through a nozzle at room temperature without going through a material phase transition in order to support the produced structure.
The precise tailoring of the composite material is made possible by this printing technology, opening the door to the use of numerous non-melting binders and fillers such cellulose fibres, hydrogels, and thermosetting resins.
By combining conductive particles like graphene, silver wires, carbon black, and carbon nanotubes (CNTs) with various oligomers and polymers like epoxy resin precursors, PLA solution, acrylate monomers, and poly (ethylene oxide), conductive inks for 3D printing have been created.
The Global Bio-Based Conductive Ink market accounted for $XX Billion in 2021 and is anticipated to reach $XX Billion by 2030, registering a CAGR of XX% from 2024 to 2030.
In a new work published in the journal Composites Science and Technology, researchers investigated the development of bio-based electrically conductive inks for use in additive manufacturing. An Italian and French scientific team conducted the study.
This direct ink extrusion method enables the insertion of non-melting fillers and binders such thermosetting resins, hydrogels, and cellulose fibres while improving the tailoring of composite materials.
Printing conductive inks using direct ink writing has been achieved when using conductive particles like silver wires, graphene, oligomers, polymers like PLA, and epoxy resin precursors.
The ink is made of furanic resin, which contains cellulosic fibres and carbon nanotubes and satisfies the carbonization requirements for printable conductive inks.
The impact of carbon nanotube morphology on ink rheological behaviour and their dispersibility in ethanol. Various ink formulations were created to enhance the rheological behaviour of the bio-ink. The innovative bio-printability ink's and electrical conductivity were also improved. Using a pyrolysis procedure, the potential improvement in electrical conductivity was further evaluated.
Sl no | Topic |
1 | Market Segmentation |
2 | Scope of the report |
3 | Abbreviations |
4 | Research Methodology |
5 | Executive Summary |
6 | Introduction |
7 | Insights from Industry stakeholders |
8 | Cost breakdown of Product by sub-components and average profit margin |
9 | Disruptive innovation in the Industry |
10 | Technology trends in the Industry |
11 | Consumer trends in the industry |
12 | Recent Production Milestones |
13 | Component Manufacturing in US, EU and China |
14 | COVID-19 impact on overall market |
15 | COVID-19 impact on Production of components |
16 | COVID-19 impact on Point of sale |
17 | Market Segmentation, Dynamics and Forecast by Geography, 2024-2030 |
18 | Market Segmentation, Dynamics and Forecast by Product Type, 2024-2030 |
19 | Market Segmentation, Dynamics and Forecast by Application, 2024-2030 |
20 | Market Segmentation, Dynamics and Forecast by End use, 2024-2030 |
21 | Product installation rate by OEM, 2023 |
22 | Incline/Decline in Average B-2-B selling price in past 5 years |
23 | Competition from substitute products |
24 | Gross margin and average profitability of suppliers |
25 | New product development in past 12 months |
26 | M&A in past 12 months |
27 | Growth strategy of leading players |
28 | Market share of vendors, 2023 |
29 | Company Profiles |
30 | Unmet needs and opportunity for new suppliers |
31 | Conclusion |
32 | Appendix |