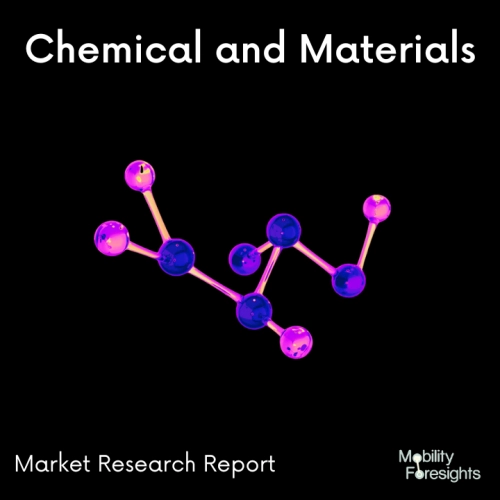
- Get in Touch with Us
Last Updated: Apr 25, 2025 | Study Period: 2024-2030
INTRODUCTION
Paraxylene (PX) is a key building block for the production of polyester, which is used for the production of fabrics, films, and packaging materials.
It is traditionally derived from petroleum-based sources, but recently, bio-based PX has been gaining significant attention due to its potential to reduce dependence on fossil fuels and the associated emissions.
Bio-based PX is derived from renewable biomass sources such as sugarcane and corn, which are fermented and hydrolyzed to produce xylose.
This xylose is then catalytically converted into a mixture of PX and isomers, which can be further purified to obtain pure PX.
The production of bio-based PX is more energy-efficient and cost-effective than traditional petroleum-based PX.
The use of renewable biomass sources also provides a much lower carbon footprint and reduces greenhouse gas emissions compared to its petroleum-based counterpart.
Furthermore, bio-based PX can be used as a drop-in substitute for the petroleum-based version, making the transition to a more sustainable alternative easier.
In addition to the environmental benefits, bio-based PX also has the potential to create new economic opportunities.
It can be used to create new value-added products, such as biodegradable plastics or bio-based fabrics, which can open up new markets for businesses.
Furthermore, the production of bio-based PX can also create jobs in the renewable energy sector. Overall, bio-based PX is a promising alternative to petroleum-based PX, offering environmental and economic benefits that could help to create a more sustainable future.
The Global Bio-Based Paraxylene market accounted for $XX Billion in 2023 and is anticipated to reach $XX Billion by 2030, registering a CAGR of XX% from 2024 to 2030.
The world's first 100% plant-based polyester shirts were made using VI rent's Bio Form PX® paraxylene, the company stated. With the help of this significant project, VI rent's technology may be used to generate bio-based, crude oil-free polyester in demonstration quantities for use in clothing and textile manufacturing. The largest and one of the synthetic fibers with the quickest growth rate in the world is polyester.
Paraxylene, which is currently only derived from crude oil, is a crucial raw ingredient used in the manufacturing of polyester. With far less greenhouse gas emissions and the same adaptability and performance as its petroleum-based cousin, VI rent's technology generates Bio Form PX paraxylene from plant-based resources.
VI rent's project established that it is possible to produce polyester clothing made entirely of plants and without petroleum, and that this alternative has a smaller carbon footprint than the existing polyester materials made from petroleum. Previously, PET plastic bottles made entirely of plants were made using VI rent's Bio Form PX paraxylene.
In order to create polyester that is free of crude oil for use in common fabrics and fiber applications, this project shows how our goods and technology may also be used in this way. Except for one significant differenceâtheir significantly smaller carbon footprintâthe fabric and shirts made from plant-based polyester are exactly the same as those made from petroleum polyester.
Working with Virent, Far Eastern New Century (FENC) developed the bio-polyester fabric and shirts as well as converted the Bio Form PX to bio-polyester. Virent has improved the process economics and brought its Bio Form PX paraxylene technology closer to commercial ready over the last few years of development effort.
Since it began operations in 2010, Virent has used its demonstration system to fulfil customer orders for both chemicals and fuels. Benzene, toluene, and mixed xylenes are examples of bio-based aromatic compounds that Virent can create in significant quantities for application development in the packaging, fabrics, and textiles industries. Additionally, Virent has created substantial petrol, jet and diesel biofuel samples for customer sampling and product development.
PetroChina unit lets contract for refining-chemical integration project.
PetroChina Guangdong Petrochemical let a contract to Honeywell UOP to provide technology licensing for multiple units as part of a refining-chemical integration project under way at its 400,000-b/d heavy crude oil site in China's Guangdong province.
PetroChina Guangdong Petrochemical Co. Ltd., a subsidiary of China National Petroleum Corp.'s PetroChina Co. Ltd., has awarded Honeywell UOP LLC a contract to provide technology licensing for multiple units as part of a refining-chemical integration project at its 400,000-b/d heavy crude oil processing and petrochemical site in China's Guangdong province's Jiayang Nanhai Petrochemical Industrial Zone.
Honeywell UOP will supply a variety of technological licenses, engineering design, critical equipment, and cutting-edge catalysts and adsorbents, as well as operator training and technical services for the site's initial and ongoing operation.
Honeywell UOP will offer a 74,300-b/d hydrocracking unit based on its unique Uncracking technology, which transforms heavy vacuum petrol oil into raw materials for motor fuels and petrochemicals, as part of the deal.
Two Honeywell UOP CCR Platforming units, each with a capacity of 60,250 b/d, will also be incorporated into the project in order to create the fuels, aromatics, and hydrogen necessary for other plant operations.
Additionally, the facility will contain a Light DE sorbent Pare Aromatics Complex that can generate high-purity paraxylene, which is a key ingredient in several plastic resins, films, and fibers, at a rate of 52,200 b/d. According to Honeywell UOP, this complex will be the biggest single-train paraxylene facility ever built.
To guarantee that the Pare process runs as efficiently as possible, Honeywell UOP's patented Sulfone, Isomer, and Tato ray processes will also be included in the aromatics block.
Due to its capability to combine refining, Honeywell UOP's range of technologies will allow PetroChina Guangdong to generate aromatics on a big scale.
Sl no | Topic |
1 | Market Segmentation |
2 | Scope of the report |
3 | Abbreviations |
4 | Research Methodology |
5 | Executive Summary |
6 | Introduction |
7 | Insights from Industry stakeholders |
8 | Cost breakdown of Product by sub-components and average profit margin |
9 | Disruptive innovation in the Industry |
10 | Technology trends in the Industry |
11 | Consumer trends in the industry |
12 | Recent Production Milestones |
13 | Component Manufacturing in US, EU and China |
14 | COVID-19 impact on overall market |
15 | COVID-19 impact on Production of components |
16 | COVID-19 impact on Point of sale |
17 | Market Segmentation, Dynamics and Forecast by Geography, 2024-2030 |
18 | Market Segmentation, Dynamics and Forecast by Product Type, 2024-2030 |
19 | Market Segmentation, Dynamics and Forecast by Application, 2024-2030 |
20 | Market Segmentation, Dynamics and Forecast by End use, 2024-2030 |
21 | Product installation rate by OEM, 2023 |
22 | Incline/Decline in Average B-2-B selling price in past 5 years |
23 | Competition from substitute products |
24 | Gross margin and average profitability of suppliers |
25 | New product development in past 12 months |
26 | M&A in past 12 months |
27 | Growth strategy of leading players |
28 | Market share of vendors, 2023 |
29 | Company Profiles |
30 | Unmet needs and opportunity for new suppliers |
31 | Conclusion |
32 | Appendix |