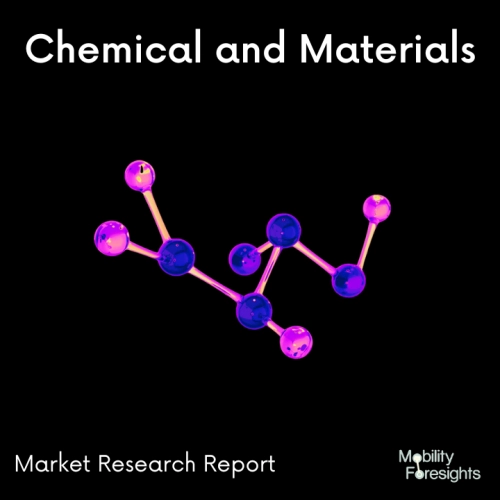
- Get in Touch with Us
Last Updated: Apr 25, 2025 | Study Period: 2024-2030
Buffing pads are circular instruments used to polish metal and other hard surfaces, including paint. They are typically constructed of microfiber, foam, or wool.
While some pads are designed for manual use, others are power tool-attachable. Additionally, they might be helpful for applying wax or sealer.
Buffing pads work to remove debris and give surfaces an even, smooth finish in a manner akin to that of fine sandpaper.
Buffering pads are a smart choice if you're applying polish or wax to a surface because they are absorbent, flexible, and create a barrier between hand and the surface and material which is being applied.
Typically, two materials are bonded together to create buffing pads. Usually, foam serves as the major component, holding the polish and making touch with the paint.
The backing material, which is often hook and loop and is also known as Velcro, lets the pad adhere to the polisher's backing plate while yet being easily detachable.
In pads made of microfiber or wool, the fibre is frequently glued to a foam core before being attached to a Velcro backing.
While tufted wool pads or other synthetic or natural fibre pads were once commonly used in buffing and polishing operations, foam buffing pads have since taken their place.
The Global Buffing Pad Market accounted for $XX Billion in 2023 and is anticipated to reach $XX Billion by 2030, registering a CAGR of XX% from 2024 to 2030.
The IKONI 2000 and IKONIC 3000 line of chemical mechanical planarization (CMP) buffing pads have been released by Dow Electronic Materials.
IKONIC 2000 buffing pads target copper barrier, HKMG, and buffing applications, whereas IKONIC 3000 buffing pads were initially intended for use in bulk copper polishing.
All pads in the IKONIC CMP buffing pad platform are designed for usage at the 28nm manufacturing node and below.
The pads are highly tunable and can be customised to address process specific requirements.Dow's volume manufacturing methods and commitment to process control further enhance performance by ensuring consistency and reliability in their customerâs processes.
When compared to the industry-standard IC1000 buffing pad, the IKONIC 4000 series offers step-out defectivity performance, which is a 70% improvement.
Sl no | Topic |
1 | Market Segmentation |
2 | Scope of the report |
3 | Abbreviations |
4 | Research Methodology |
5 | Executive Summary |
6 | Introduction |
7 | Insights from Industry stakeholders |
8 | Cost breakdown of Product by sub-components and average profit margin |
9 | Disruptive innovation in the Industry |
10 | Technology trends in the Industry |
11 | Consumer trends in the industry |
12 | Recent Production Milestones |
13 | Component Manufacturing in US, EU and China |
14 | COVID-19 impact on overall market |
15 | COVID-19 impact on Production of components |
16 | COVID-19 impact on Point of sale |
17 | Market Segmentation, Dynamics and Forecast by Geography, 2024-2030 |
18 | Market Segmentation, Dynamics and Forecast by Product Type, 2024-2030 |
19 | Market Segmentation, Dynamics and Forecast by Application, 2024-2030 |
20 | Market Segmentation, Dynamics and Forecast by End use, 2024-2030 |
21 | Product installation rate by OEM, 2023 |
22 | Incline/Decline in Average B-2-B selling price in past 5 years |
23 | Competition from substitute products |
24 | Gross margin and average profitability of suppliers |
25 | New product development in past 12 months |
26 | M&A in past 12 months |
27 | Growth strategy of leading players |
28 | Market share of vendors, 2023 |
29 | Company Profiles |
30 | Unmet needs and opportunity for new suppliers |
31 | Conclusion |
32 | Appendix |