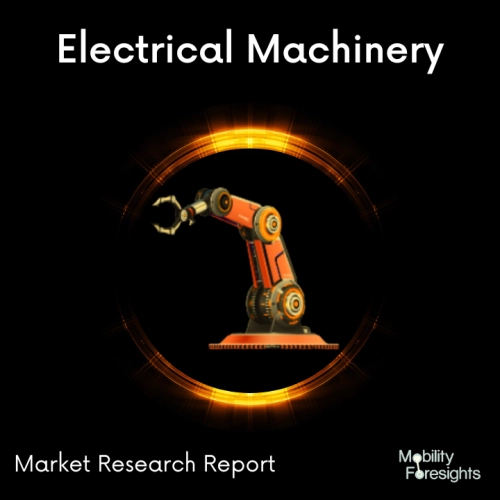
- Get in Touch with Us
Last Updated: Apr 25, 2025 | Study Period: 2024-2030
A family of iron-carbon alloys with a carbon concentration of more than 2% is called cast iron. Its comparatively low melting temperature is what makes it valuable. White cast iron has carbide impurities that allow cracks to pass through easily, grey cast iron has graphite flakes that deflect a passing crack and cause countless new cracks as the material breaks, and ductile cast iron has spherical graphite "nodules" that prevent the crack from spreading further.
The two main alloying components of cast iron are silicon (Si), which makes up 1-3 wt%, and carbon (C), which ranges from 1.8 to 4 wt%. Steel refers to iron alloys with a reduced carbon percentage.
Except for cast irons that are pliable, it usually has a brittle nature. Cast iron motors are utilized in pipelines, machinery, and parts for the automobile sector such as cylinder heads, cylinder blocks, and gearbox cases because of their comparatively low melting point, good fluidity, castability, great machinability, resistance to deformation, and wear resistance. It can withstand oxidation damage but is notoriously challenging to weld.
Pig iron, the byproduct of smelting iron ore in a blast furnace, is used to make cast iron. Cast iron can be produced either directly from the molten pig iron or by remelting the pig iron, frequently with significant additions of iron, steel, limestone, and carbon (coke), as well as after going through a number of procedures to eliminate unfavorable impurities.
The molten iron may burn off its phosphorus and sulfur, but this also burns off its carbon, which must be supplied. Carbon and silicon content are adjusted to the necessary amounts, which can range from 2-3.5% and 1-3%, respectively, depending on the application.
Before the final shape is cast, more elements may be added to the melt if desired. While cast iron is occasionally melted in a unique kind of blast furnace known as a cupola, in current applications, electric induction furnaces or electric arc furnaces are more frequently used. Once the cast iron has finished melting, it is placed into a holding furnace or ladle.
The Global Cast Iron Motors market accounted for $XX Billion in 2023 and is anticipated to reach $XX Billion by 2030, registering a CAGR of XX% from 2024 to 2030.
The small block "mouse" engines from GM have the biggest displacement. It had a legendary reputation for producing enormous levels of torque and was well-liked by both on- and off-road racers, but sadly it only had a ten-year production run before it was discontinued.
After a 35-year sabbatical, Blue Print Engines is now happy to announce the revival of its own 400 c.i. small block "mighty mouse," which was entirely new from the ground up.
This tough powerhouse was created exclusively by the technical team at Blue Print Engines using cutting-edge computer design software and production techniques. Its basis is a brand-new precision Cast Iron Motor with a CNC-machined iron block made wholly in the USA.
The Blue Print 400 has been entirely overhauled with roller lifters, a one-piece rear seal, and 4-bolt splayed main caps, giving it significantly more horsepower and strength than the original.
These brand-new, dyno-tested engines aren't your grandfather's 400; they're sold standard with aluminum heads and come in a variety of models ranging from 460 hp to 508 hp. These powerful engines were created with car enthusiasts in mind who wanted a new precision cast iron block combined with all new parts and finished off with one of the best warranties in the business.
Sl no | Topic |
1 | Market Segmentation |
2 | Scope of the report |
3 | Abbreviations |
4 | Research Methodology |
5 | Executive Summary |
6 | Introduction |
7 | Insights from Industry stakeholders |
8 | Cost breakdown of Product by sub-components and average profit margin |
9 | Disruptive innovation in the Industry |
10 | Technology trends in the Industry |
11 | Consumer trends in the industry |
12 | Recent Production Milestones |
13 | Component Manufacturing in US, EU and China |
14 | COVID-19 impact on overall market |
15 | COVID-19 impact on Production of components |
16 | COVID-19 impact on Point of sale |
17 | Market Segmentation, Dynamics and Forecast by Geography, 2024-2030 |
18 | Market Segmentation, Dynamics and Forecast by Product Type, 2024-2030 |
19 | Market Segmentation, Dynamics and Forecast by Application, 2024-2030 |
20 | Market Segmentation, Dynamics and Forecast by End use, 2024-2030 |
21 | Product installation rate by OEM, 2023 |
22 | Incline/Decline in Average B-2-B selling price in past 5 years |
23 | Competition from substitute products |
24 | Gross margin and average profitability of suppliers |
25 | New product development in past 12 months |
26 | M&A in past 12 months |
27 | Growth strategy of leading players |
28 | Market share of vendors, 2023 |
29 | Company Profiles |
30 | Unmet needs and opportunity for new suppliers |
31 | Conclusion |
32 | Appendix |