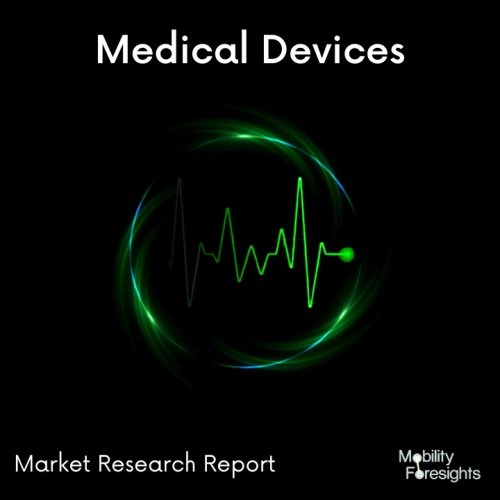
- Get in Touch with Us
Last Updated: Apr 25, 2025 | Study Period: 2024-2030
The cell washing centrifuges are specialized devices that assist particular clinical and medical applications, such as removing cellular waste, superfluous proteins, and other components from donor blood's red blood cells.
Rh and antiglobulin (AGT or Coombs) tests, slide staining, blood grouping, typing, compatibility, and cross-matching are all performed using cell washing centrifuges.
They are made up of the same fundamental parts as other centrifuges: an electric motor, a rotor or head, a bowl, and electronics for the motor drive.
The cooling system utilized in "ordinary '' refrigerated centrifuges is also used in some cell washing centrifuges.
A cell washing centrifuge can be identified by its particular purpose rotor or head that is mounted on the motor shaft.
Red blood cells can be automatically washed, decanted, mixed, and washed again with the help of this head.
As with any other centrifuge operation, cell cleaning starts with inserting test tubes into the rotor's holders.
In contrast to standard centrifugation, a lab technician inserts the tubes into the rotor without removing their covers.
Other designs incorporate the cover within the lid, whereas in certain cases a separate cover is dropped and fastened over the rotor.
The test tube is often washed by adding saline, centrifuging it, and then removing the supernant.
Global cell washing system market accounted for $XX Billion in 2022 and is anticipated to reach $XX Billion by 2030, registering a CAGR of XX% from 2023 to 2030.
For routine and research ELISA applications, their dependable and user-friendly Themo Scientific Well wash microplate strip washers offer secure cleaning performance.
For maximum usability, convenience, and safety, Well wash washers have a big color display with a graphical user interface, local language versions, and non-pressurized bottles.
Gene therapy, cell treatment, and tissue-engineering products are examples of regenerative medicine and advanced therapy medical products (ATMPs). It is obvious that ATMP manufacturing continues to confront substantial problems as more ATMPs flood the market.
One of these is the high cost of raw materials and specialized equipment, which immediately raises the price of products, which may subsequently find it difficult to obtain sufficient compensation for market viability.
The challenges also include requirements for Good Manufacturing Practice (GMP) production and quality assurance capacity, complex supply chain logistics, a workforce with insufficient skills, and these factors. One feat Gene therapy, cell treatment.
Sl no | Topic |
1 | Market Segmentation |
2 | Scope of the report |
3 | Abbreviations |
4 | Research Methodology |
5 | Executive Summary |
6 | Introduction |
7 | Insights from Industry stakeholders |
8 | Cost breakdown of Product by sub-components and average profit margin |
9 | Disruptive innovation in the Industry |
10 | Technology trends in the Industry |
11 | Consumer trends in the industry |
12 | Recent Production Milestones |
13 | Component Manufacturing in US, EU and China |
14 | COVID-19 impact on overall market |
15 | COVID-19 impact on Production of components |
16 | COVID-19 impact on Point of sale |
17 | Market Segmentation, Dynamics and Forecast by Geography, 2024-2030 |
18 | Market Segmentation, Dynamics and Forecast by Product Type, 2024-2030 |
19 | Market Segmentation, Dynamics and Forecast by Application, 2024-2030 |
20 | Market Segmentation, Dynamics and Forecast by End use, 2024-2030 |
21 | Product installation rate by OEM, 2023 |
22 | Incline/Decline in Average B-2-B selling price in past 5 years |
23 | Competition from substitute products |
24 | Gross margin and average profitability of suppliers |
25 | New product development in past 12 months |
26 | M&A in past 12 months |
27 | Growth strategy of leading players |
28 | Market share of vendors, 2023 |
29 | Company Profiles |
30 | Unmet needs and opportunity for new suppliers |
31 | Conclusion |
32 | Appendix |