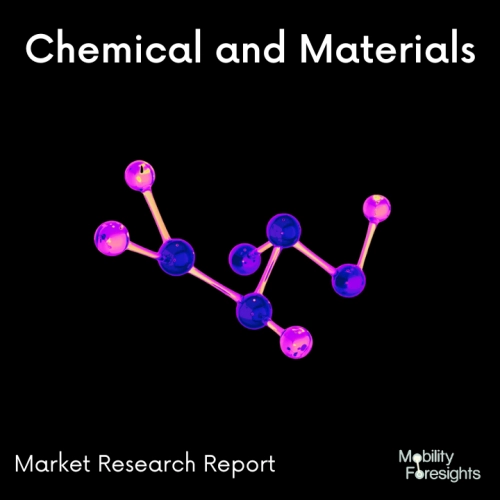
- Get in Touch with Us
Last Updated: Apr 25, 2025 | Study Period: 2024-2030
The adaptability and effectiveness of a welding technique are determined by how the energy needed for welding is introduced into the laminates.
Carbon fibre-reinforced polymer composites (CFRPC) can be heated using electrical induction because the carbon fibres (CF) offer a sufficient level of electrical conductivity.
The CF must, however, be positioned in the laminate in order to produce closed electrical conductor loops for this purpose.
Heat is dissipated as a result of the electric losses within the CF and between CF-CF junctions (caused by dielectric hysteresis or contact resistance).
In order to create eddy currents in the thermoplastic CFRPC during continuous induction welding, an induction coil is moved along the weld seam.
As a result, the thermoplastic matrix in the area where the two adherends intersect is heated past its melting point.
Because of its low density, high specific strength, high specific modulus, great degree of design freedom, etc.CFRP is a well-liked composite.
For creating composite and metal hybrid structures,CFRP is the perfect material. A decrease in vehicle weight results in fuel savings.
The Global CFRP High-Speed Thermal Welding market accountedfor $XX Billion in 2023 and is anticipated to reach $XX Billion by 2030, registering a CAGR of XX% from 2024 to 2030.
Carbon fibre-reinforced thermoset pieces may now be thermally welded at high speeds thanks to technology created by Toray Industries Inc.
Toray claims that this technique will make it possible to produce carbon fibre-reinforced polymer (CFRP) airframes at a high rate while reducing their weight.
The company is working on demonstrations with the intention of commercialising airframes by 2030 and extending applications at the same time.
Without the need of adhesive bonding or bolt fastening, Toray's straightforward bonding method creates a thermally weldable layer on the surface of thermoset or thermoplastic components reinforced with carbon fibre.
This layer may then be instantly heated to join the part surfaces.
The company used thermally weldable CFRP thermoset pieces to construct a demonstrator that replicated the fundamental structure of an aircraft at high speed.
They found that the mechanical characteristics and joint strength were comparable to those of co-cured CFRP constructions for current aircraft models.
In addition to reducing CO2 emissions over the course of the CFRP airframe's life cycle and reducing weight, Toray claims its technology will enable high-rate production that is comparable to or greater than that for aluminium alloy airframes.
Results from the project "Development of Novel Innovative Composite Materials and Forming Technologies," sponsored by the New Energy and Industrial Technology Development Organization, have contributed to Today's advancement in this development effort (NEDO).
Sl no | Topic |
1 | Market Segmentation |
2 | Scope of the report |
3 | Abbreviations |
4 | Research Methodology |
5 | Executive Summary |
6 | Introduction |
7 | Insights from Industry stakeholders |
8 | Cost breakdown of Product by sub-components and average profit margin |
9 | Disruptive innovation in the Industry |
10 | Technology trends in the Industry |
11 | Consumer trends in the industry |
12 | Recent Production Milestones |
13 | Component Manufacturing in US, EU and China |
14 | COVID-19 impact on overall market |
15 | COVID-19 impact on Production of components |
16 | COVID-19 impact on Point of sale |
17 | Market Segmentation, Dynamics and Forecast by Geography, 2024-2030 |
18 | Market Segmentation, Dynamics and Forecast by Product Type, 2024-2030 |
19 | Market Segmentation, Dynamics and Forecast by Application, 2024-2030 |
20 | Market Segmentation, Dynamics and Forecast by End use, 2024-2030 |
21 | Product installation rate by OEM, 2023 |
22 | Incline/Decline in Average B-2-B selling price in past 5 years |
23 | Competition from substitute products |
24 | Gross margin and average profitability of suppliers |
25 | New product development in past 12 months |
26 | M&A in past 12 months |
27 | Growth strategy of leading players |
28 | Market share of vendors, 2023 |
29 | Company Profiles |
30 | Unmet needs and opportunity for new suppliers |
31 | Conclusion |
32 | Appendix |