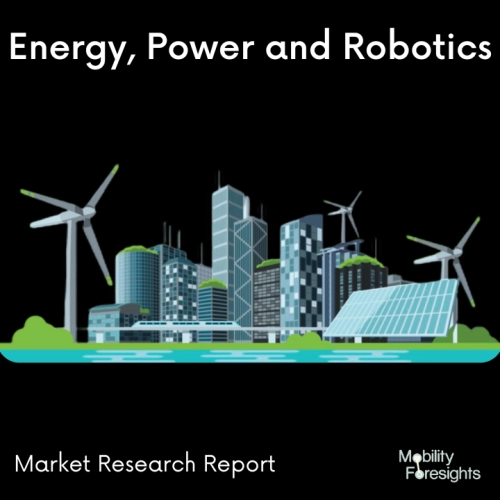
- Get in Touch with Us
Last Updated: Apr 25, 2025 | Study Period: 2023-2030
INTRODUCTION
Chemical synthesis reactors are specialized pieces of equipment used to carry out chemical reactions in a controlled environment. These reactors are designed to create a specific reaction, with controlled parameters such as temperature, pressure, and pH to name a few.
Chemical synthesis reactors can be divided into two main categories: batch reactors and continuous reactors. Batch reactors are used to carry out a single reaction, and can be thought of as a âclosed systemâ in that the reactants are added all at once, and the products are removed at the end of the reaction.
Continuous reactors are designed to run a reaction continuously, with reactants added and products removed as the reaction proceeds.
The type of reactor used for a particular reaction depends on the desired outcome, as well as the nature of the reactants. For example, some reactions require a higher temperature or pressure than would be achievable in a batch reactor, and so a continuous reactor would be needed. Similarly, some reactions require a very precise control of the reaction conditions, and so a continuous reactor may be the only option.
The type of reactor also depends on the scale of the reaction, with batch reactors typically used for small-scale reactions, and continuous reactors used for larger ones. Additionally, reactors can be specialized for specific reactions, such as those involving hazardous materials or those requiring the use of catalysts.
Overall, chemical synthesis reactors are an essential tool for the modern chemist, allowing for precise control over the parameters of a reaction. They are used in a variety of industries, from pharmaceuticals to food production, and provide a safe and effective way to carry out chemical reactions.
GLOBAL CHEMICAL SYNTHESIS REACTORS MARKET SIZE AND FORECAST
The Global Chemical Synthesis Reactors market accounted for $XX Billion in 2022 and is anticipated to reach $XX Billion by 2030, registering a CAGR of XX% from 2023 to 2030.
The development and discovery of new chemical reactions is being revolutionised by reactor automation. By delegating monotonous tasks like data gathering and experiment execution to machines, chemical synthesis researchers can devote more time to critical interpretation and innovative problem solving.
Applications such as efficient chemical space exploration and responsive manufacturing will heavily depend on the capacity to prepare complicated products and late-stage intermediates autonomously, instead of just basic starting ingredients.
Because of the tremendous structural diversity and chemical/physical interdependencies between the phases, it is still very difficult to translate automated technology from specific single-step jobs to more general multistep synthesis.
Many essential drugs and materials have been developed by synthesising complicated compounds, which involve a series of transformations from easily accessible starting components and exact control over the chemical reactivity and reaction circumstances.
Intermediary work-ups and purifications, which demand a large energy and material (such as solvent) input, are frequently used to prevent competing side reactions between chemical species engaged in each particular stage.
Conversely, reactions that are directly concatenatedâalso referred to as "one-pot processes" or "reaction telescoping"âcan produce less waste and are therefore more in line with the future net zero carbon goal.
As a result, they cover a range of intricate development difficulties that need for comprehensive examination. In practice, the majority of total syntheses will combine these methodologies when suitable.
The automated assembly of tiny molecules has come a long way, although these developments are still mainly confined to repeats of comparable events. A platform that can execute a wide range of multi step operations is important because of the complexity and variety of organic compounds. But in order to facilitate automation of chemical synthesis in general, a global standard would be necessary.
This was accomplished by Cronin et al. with the development of the Chemputer, a system that can conduct autonomously on a modular robotic platform and understand specified synthetic protocols.Using traditional bench chemistry, the platform was built to execute reactions in order to maximise the system's compatibility with current chemical literature.
THIS REPORT WILL ANSWER FOLLOWING QUESTIONS
Sl no | Topic |
1 | Market Segmentation |
2 | Scope of the report |
3 | Abbreviations |
4 | Research Methodology |
5 | Executive Summary |
6 | Introduction |
7 | Insights from Industry stakeholders |
8 | Cost breakdown of Product by sub-components and average profit margin |
9 | Disruptive innovation in the Industry |
10 | Technology trends in the Industry |
11 | Consumer trends in the industry |
12 | Recent Production Milestones |
13 | Component Manufacturing in US, EU and China |
14 | COVID-19 impact on overall market |
15 | COVID-19 impact on Production of components |
16 | COVID-19 impact on Point of sale |
17 | Market Segmentation, Dynamics and Forecast by Geography, 2023-2030 |
18 | Market Segmentation, Dynamics and Forecast by Product Type, 2023-2030 |
19 | Market Segmentation, Dynamics and Forecast by Application, 2023-2030 |
20 | Market Segmentation, Dynamics and Forecast by End use, 2023-2030 |
21 | Product installation rate by OEM, 2023 |
22 | Incline/Decline in Average B-2-B selling price in past 5 years |
23 | Competition from substitute products |
24 | Gross margin and average profitability of suppliers |
25 | New product development in past 12 months |
26 | M&A in past 12 months |
27 | Growth strategy of leading players |
28 | Market share of vendors, 2023 |
29 | Company Profiles |
30 | Unmet needs and opportunity for new suppliers |
31 | Conclusion |
32 | Appendix |