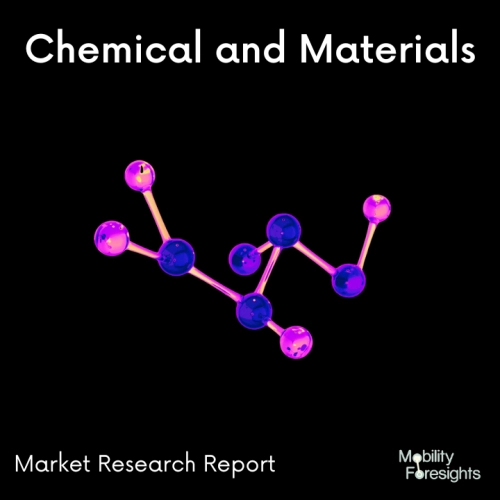
- Get in Touch with Us
Last Updated: Apr 25, 2025 | Study Period: 2024-2030
The process of adding a conversion coating to a metal surface, usually aluminum or zinc, in order to improve its corrosion resistance and adhesive qualities is known as chromatin coating.
The conversion coating is typically a thin layer of chromate that grows on the metal surface by a chemical reaction between the metal and a chromate solutionChromatin coating is commonly used in the aerospace and automotive industries, as well as in the fabrication of electronic components, to protect metal surfaces from corrosion and increase their electrical conductivity.
Numerous techniques, including spray coating, dip coating, and brush coating, can be used to complete the procedure.
It's crucial to remember that while chromatin coating can provide efficient corrosion protection, it can also be dangerous to human health and the environment due to the usage of hexavalent chromium, a carcinogenic substance.
As a result, several procedures like trivalent chromatin and non-chromate conversion coatings have been created to lessen the effects of chromatin coating on the environment.
Global chromatin coating market accounted for $XX Billion in 2023 and is anticipated to reach $XX Billion by 2030, registering a CAGR of XX% from 2024 to 2030.
Decorative plating, chromate conversion coatings, phosphating, black oxide coatings, and many other products for surface pretreatment and corrosion protection are all available on the new website from Heat bath Corp., a provider of metal finishing products.
The acid, liquid, and powder products known as BONDERITE chromate conversion coatings for aluminum were created especially for these coatings. The streamlined coating procedures and the highest requirements for corrosion protection and paint adhesion will help your manufacturing operations.
chromate conversion coating, rinsing, and drying with BONDERITE. The coated item can be painted when it has dried and is ready for usage. Depending on the coating thickness, the untreated color might range from yellow to brown. The skilled staff at Henkel has created specialized coating materials for various metals and functional finishes.
Numerous high-quality Al alloy coatings are available due to the vast range of uses. The main benefit of Henkel's liquid products is automatic dosing machinery, which simplifies life for employees while enhancing safety and maintaining their health.
Sl no | Topic |
1 | Market Segmentation |
2 | Scope of the report |
3 | Abbreviations |
4 | Research Methodology |
5 | Executive Summary |
6 | Introduction |
7 | Insights from Industry stakeholders |
8 | Cost breakdown of Product by sub-components and average profit margin |
9 | Disruptive innovation in the Industry |
10 | Technology trends in the Industry |
11 | Consumer trends in the industry |
12 | Recent Production Milestones |
13 | Component Manufacturing in US, EU and China |
14 | COVID-19 impact on overall market |
15 | COVID-19 impact on Production of components |
16 | COVID-19 impact on Point of sale |
17 | Market Segmentation, Dynamics and Forecast by Geography, 2024-2030 |
18 | Market Segmentation, Dynamics and Forecast by Product Type, 2024-2030 |
19 | Market Segmentation, Dynamics and Forecast by Application, 2024-2030 |
20 | Market Segmentation, Dynamics and Forecast by End use, 2024-2030 |
21 | Product installation rate by OEM, 2023 |
22 | Incline/Decline in Average B-2-B selling price in past 5 years |
23 | Competition from substitute products |
24 | Gross margin and average profitability of suppliers |
25 | New product development in past 12 months |
26 | M&A in past 12 months |
27 | Growth strategy of leading players |
28 | Market share of vendors, 2023 |
29 | Company Profiles |
30 | Unmet needs and opportunity for new suppliers |
31 | Conclusion |
32 | Appendix |