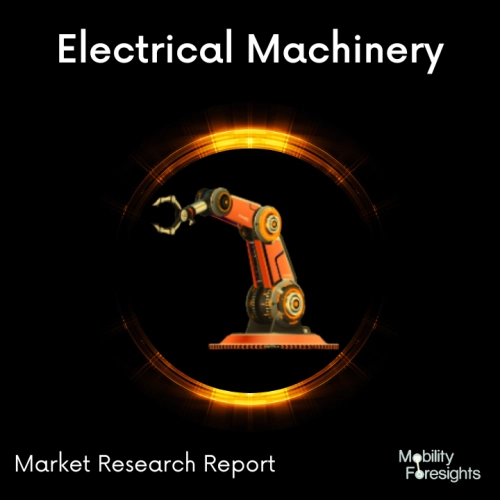
- Get in Touch with Us
Last Updated: Apr 25, 2025 | Study Period: 2023-2030
INTRODUCTION
Aluminum has unique characteristics that have made aluminium CNC machining a preferred technology for product manufacture. Manufacturers can employ Computer Numerical Control (CNC) machinery for production or prototype because they are computer-controlled.
Due to its exceptional machinability, aluminium is one of the most often utilised materials for CNC machining. Aluminum is also pliable and has specific mechanical and thermal characteristics that make it perfect for CNC machining applications. Aluminum is a far better choice than other lightweight metal alloys like titanium and magnesium because of these benefits.
Due to its machinability, engineers usually select aluminium over other metals. This metal can be efficiently and accurately cut using CNC machining tools since it is simple to shape and chip.
Due to the high degree of machinability, the machining job can be completed more quickly and more affordably. Additionally, the machinability of aluminium reduces the possibility of part deformation during workpiece cutting, resulting in improved precision, accuracy, and repeatability.
GLOBAL CNC ALUMINIUM MACHINING CENTER MARKET SIZE AND FORECAST
Global CNC Aluminum Machining center market accounted for $XX Billion in 2022 and is anticipated to reach $XX Billion by 2030, registering a CAGR of XX% from 2023 to 2030.
NEW PRODUCT LAUNCH
At the AMB trade fair in Stuttgart in September, INDEX unveiled their brand-new six-spindle CNC automated lathe capable of sliding-headstock turn-milling. Kingsbury, INDEX's lone agent, is able to provide INDEX to customers in the UK and Ireland.
The MS22-L is the first multi-spindle turning machine that enables simultaneous use of two tool carriers for sliding-headstock machining at all six spindle positions. This increases productivity.
These most recent technologies are used in the series manufacture of all long, thin, or complex pieces up to 200mm long and 5-22mm diameter as a variation of the INDEX MS22 fixed-head six-spindle multi.
The transition away from conventional single-spindle lathes has improved the efficiency of a number of parts, including injector nozzles for internal combustion engines, pistons and nozzles for fluid technology, dental implants, and a wide range of shafts for the developing electromobility sector.
Six air-cooled motor spindles and a three-part Hirth that ensures precise alignment work together to produce the best results. A double-cone collet ball-bearing guide brush has the ability to be programmed to apply various pressures to each individual brush.
With 120m of Z-axis travel and a swivelling 10,000 rpm synchro spindle, damage-free component removal is guaranteed. In addition, they permit reverse-end machining when used with six tools.
COMPANY PROFILE
THIS REPORT WILL ANSWER FOLLOWING QUESTIONS
Sl no | Topic |
1 | Market Segmentation |
2 | Scope of the report |
3 | Abbreviations |
4 | Research Methodology |
5 | Executive Summary |
6 | Introduction |
7 | Insights from Industry stakeholders |
8 | Cost breakdown of Product by sub-components and average profit margin |
9 | Disruptive innovation in the Industry |
10 | Technology trends in the Industry |
11 | Consumer trends in the industry |
12 | Recent Production Milestones |
13 | Component Manufacturing in US, EU and China |
14 | COVID-19 impact on overall market |
15 | COVID-19 impact on Production of components |
16 | COVID-19 impact on Point of sale |
17 | Market Segmentation, Dynamics and Forecast by Geography, 2023-2030 |
18 | Market Segmentation, Dynamics and Forecast by Product Type, 2023-2030 |
19 | Market Segmentation, Dynamics and Forecast by Application, 2023-2030 |
20 | Market Segmentation, Dynamics and Forecast by End use, 2023-2030 |
21 | Product installation rate by OEM, 2023 |
22 | Incline/Decline in Average B-2-B selling price in past 5 years |
23 | Competition from substitute products |
24 | Gross margin and average profitability of suppliers |
25 | New product development in past 12 months |
26 | M&A in past 12 months |
27 | Growth strategy of leading players |
28 | Market share of vendors, 2023 |
29 | Company Profiles |
30 | Unmet needs and opportunity for new suppliers |
31 | Conclusion |
32 | Appendix |