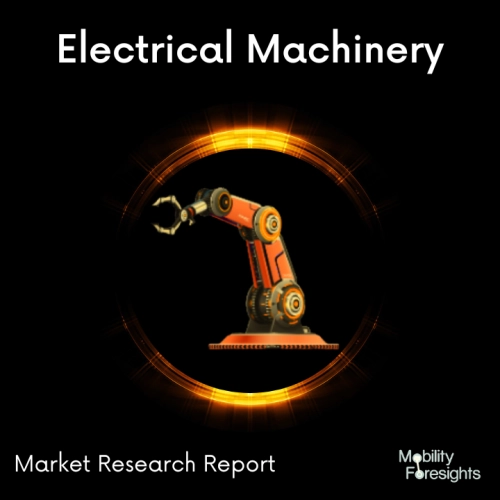
- Get in Touch with Us
Last Updated: Apr 25, 2025 | Study Period: 2023-2030
The production procedure for cold forging is carried out at room temperature. The workpiece is forced till it takes on its shape between two dies.
The process involves rolling, drawing, pressing, spinning, extruding, and heading to produce a completed, ready-to-fit component.
The billet is guided by sensors that are integrated into the CNC machine. It is entirely motorised, and a computer panel controls it. The part is formed by removing extra metal using a spinning tool.
The Global CNC Cold Forging Machine market accounted for $XX Billion in 2022 and is anticipated to reach $XX Billion by 2030, registering a CAGR of XX% from 2023 to 2030.
AmTech International offers OEM customers in the United States, Mexico, and Canada services for cold forging manufacturers who specialise in machined parts.
When compared to CNC machining, AmTech's cold forging manufacturing process can be 100 times faster while maintaining accuracy. There are six raw cold forgings being processed in the six-station machine, each in a distinct stage of production.
A new raw forging is fed into the first die while being sheared to a designed length at the end of each cycle of the machine, ejecting the precision machined item from the last die.
One minute's worth of cycles are spent repeating the entire process.For the production of high volume goods at a low cost, this manufacturing procedure is quite effective.
Cold forging machining is extremely cost-effective for AmTech since raw forged parts allow for precise machining of net shape or nearly net shape parts with a tolerance of 1/10mm in overall diameter.
The lack of material grain growth, which leaves the surface of cold-forged items exactly aligned to the geometry of the steel or aluminium material grains, is another advantage.
This surface is also incredibly hard and resistant. With high production lines, the forging plant is optimised. To produce high-quality, machined forgings that meet strict tolerance standards, each line is outfitted with CNC turning, milling, and broaching stations.
Sl no | Topic |
1 | Market Segmentation |
2 | Scope of the report |
3 | Abbreviations |
4 | Research Methodology |
5 | Executive Summary |
6 | Introduction |
7 | Insights from Industry stakeholders |
8 | Cost breakdown of Product by sub-components and average profit margin |
9 | Disruptive innovation in the Industry |
10 | Technology trends in the Industry |
11 | Consumer trends in the industry |
12 | Recent Production Milestones |
13 | Component Manufacturing in US, EU and China |
14 | COVID-19 impact on overall market |
15 | COVID-19 impact on Production of components |
16 | COVID-19 impact on Point of sale |
17 | Market Segmentation, Dynamics and Forecast by Geography, 2023-2030 |
18 | Market Segmentation, Dynamics and Forecast by Product Type, 2023-2030 |
19 | Market Segmentation, Dynamics and Forecast by Application, 2023-2030 |
20 | Market Segmentation, Dynamics and Forecast by End use, 2023-2030 |
21 | Product installation rate by OEM, 2023 |
22 | Incline/Decline in Average B-2-B selling price in past 5 years |
23 | Competition from substitute products |
24 | Gross margin and average profitability of suppliers |
25 | New product development in past 12 months |
26 | M&A in past 12 months |
27 | Growth strategy of leading players |
28 | Market share of vendors, 2023 |
29 | Company Profiles |
30 | Unmet needs and opportunity for new suppliers |
31 | Conclusion |
32 | Appendix |