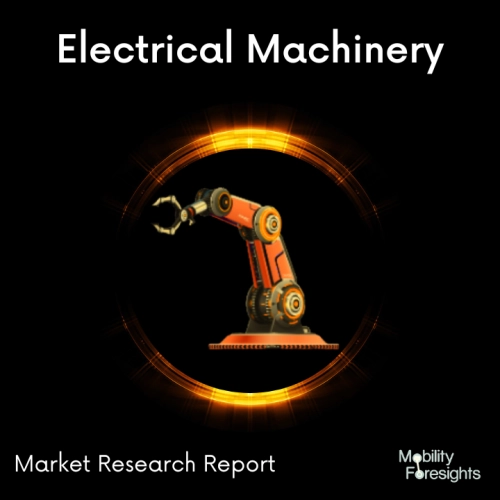
- Get in Touch with Us
Last Updated: Apr 25, 2025 | Study Period: 2024-2030
Through the use of software contained in a microcomputer connected to the tool, computer numerical control (CNC) is a technique for automating control of machine tools. It is frequently employed in manufacturing machine parts made of metal and plastic.
The system collects data on the surface of the part using a ball probe and compares it to the intended parameters. This method aids in ensuring that the components created by the CNC machine adhere to the necessary tolerances and specifications, enhancing the precision and calibre of the finished item.
Global CNC digital overball measuring system market accounted for $XX Billion in 2023 and is anticipated to reach $XX Billion by 2030, registering a CAGR of XX% from 2024 to 2030.
In comparison to current manual and semi-automatic inspection devices, the DBD series (DBD-250Ei) from Tokyo Technical Instruments Inc. are new inspection units with improved precision and more stable measuring results.
It resolved a number of common issues, including process complexity for gears with an odd number of teeth and result fluctuation related to operator experience. These machines now make it possible to measure shaft gears and ring gears over balls.
A ring gear-specific over-ball measurement device is the DBD-250Ei. It allows for the OBD measurement of both external and internal teeth up to an OD of 250mm. Both odd and even teeth are simple to measure. A shaft gear-specific over ball measurement device is the DBD-250SHh.
It allows for the automatic measurement of exterior teeth with an OD of up to 250mm. With automatic offset of even-numbered teeth and height setting at the tooth width functions, it is intended to measure the bias IN-OUT of the crowning lead correctly. Runout in the tooth space can also be measured.
Sl no | Topic |
1 | Market Segmentation |
2 | Scope of the report |
3 | Abbreviations |
4 | Research Methodology |
5 | Executive Summary |
6 | Introduction |
7 | Insights from Industry stakeholders |
8 | Cost breakdown of Product by sub-components and average profit margin |
9 | Disruptive innovation in the Industry |
10 | Technology trends in the Industry |
11 | Consumer trends in the industry |
12 | Recent Production Milestones |
13 | Component Manufacturing in US, EU and China |
14 | COVID-19 impact on overall market |
15 | COVID-19 impact on Production of components |
16 | COVID-19 impact on Point of sale |
17 | Market Segmentation, Dynamics and Forecast by Geography, 2024-2030 |
18 | Market Segmentation, Dynamics and Forecast by Product Type, 2024-2030 |
19 | Market Segmentation, Dynamics and Forecast by Application, 2024-2030 |
20 | Market Segmentation, Dynamics and Forecast by End use, 2024-2030 |
21 | Product installation rate by OEM, 2023 |
22 | Incline/Decline in Average B-2-B selling price in past 5 years |
23 | Competition from substitute products |
24 | Gross margin and average profitability of suppliers |
25 | New product development in past 12 months |
26 | M&A in past 12 months |
27 | Growth strategy of leading players |
28 | Market share of vendors, 2023 |
29 | Company Profiles |
30 | Unmet needs and opportunity for new suppliers |
31 | Conclusion |
32 | Appendix |