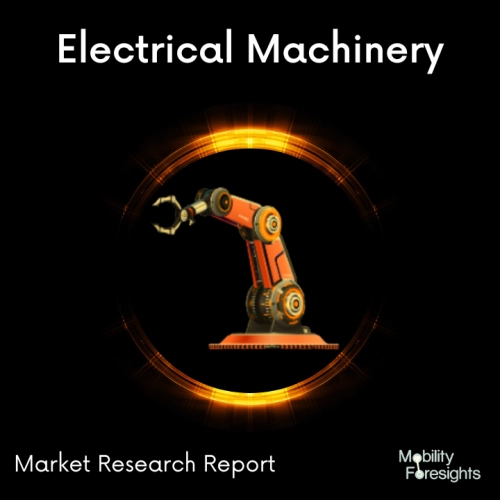
- Get in Touch with Us
Last Updated: Apr 25, 2025 | Study Period: 2024-2030
Electrical energy is used in electrical discharge machining to "erode" the material of the workpiece. An electrode constructed of copper, brass, graphite, or tungsten, or alloys of those materials, is used to spark a succession of high-frequency sparks between an electrically conductive workpiece.
EDM is being used by a growing number of CNC turning and milling companies to produce part characteristics that are otherwise nonmachinable. New machining techniques must be adopted in order to use EDM.
The CNC equipment is not "traditional." It's important to comprehend and manage the use of copper and graphite electrodes, as well as the necessity of using application-specific software and the right work holding.
The Global CNC Electrical Discharge Machine market accounted for $XX Billion in 2023 and is anticipated to reach $XX Billion by 2030, registering a CAGR of XX% from 2024 to 2030.
In order to precisely erode difficult-to-work materials like tungsten, the Soviet Union developed a basic CNC electric discharge machine that used discharges from a resistor-capacitor network.
A wider range of activities are now possible for the technology thanks to the development of 5-axis CNC wire EDM equipment. Because of the increased degrees of freedom in part design, it is significantly easier to create sophisticated three-dimensional products.
This advantage results from the procedure's capability to directly interact with pre-hardened tool steels. Serious internal strains and distortion/accuracy in machined items can be introduced by the hardening process. Almost all of this problem is eliminated by the capacity to cut pre-hardened materials.
Between a tool electrode and a billet of material that needs to be cut, an electrical discharge (or spark) is used as a machining technique. A minuscule spot where the spark energy is lost as heat can reach temperatures of 12,000°C, vaporizing both components.
However, due to the small size of the point of contact, the part does not absorb much of that heat. By passing the wire across the cut region so the cut is always facing new wire, wire EDM preserves the electrode. The work is advanced along a preprogrammed path by the table as the arc wears away at the workpiece. With this method, any CNC equipment produces the most accurate and fine cutting possible.
Sl no | Topic |
1 | Market Segmentation |
2 | Scope of the report |
3 | Abbreviations |
4 | Research Methodology |
5 | Executive Summary |
6 | Introdauction |
7 | Insights from Industry stakeholders |
8 | Cost breakdown of Product by sub-components and average profit margin |
9 | Disruptive innovation in theIndustry |
10 | Technology trends in the Industry |
11 | Consumer trends in the industry |
12 | Recent Production Milestones |
13 | Component Manufacturing in US, EU and China |
14 | COVID-19 impact on overall market |
15 | COVID-19 impact on Production of components |
16 | COVID-19 impact on Point of sale |
17 | Market Segmentation, Dynamics and Forecast by Geography, 2024-2030 |
18 | Market Segmentation, Dynamics and Forecast by Product Type, 2024-2030 |
19 | Market Segmentation, Dynamics and Forecast by Application, 2024-2030 |
20 | Market Segmentation, Dynamics and Forecast by End use, 2024-2030 |
21 | Product installation rate by OEM, 2023 |
22 | Incline/Decline in Average B-2-B selling price in past 5 years |
23 | Competition from substitute products |
24 | Gross margin and average profitability of suppliers |
25 | New product development in past 12 months |
26 | M&A in past 12 months |
27 | Growth strategy of leading players |
28 | Market share of vendors, 2023 |
29 | Company Profiles |
30 | Unmet needs and opportunity for new suppliers |
31 | Conclusion |
32 | Appendix |