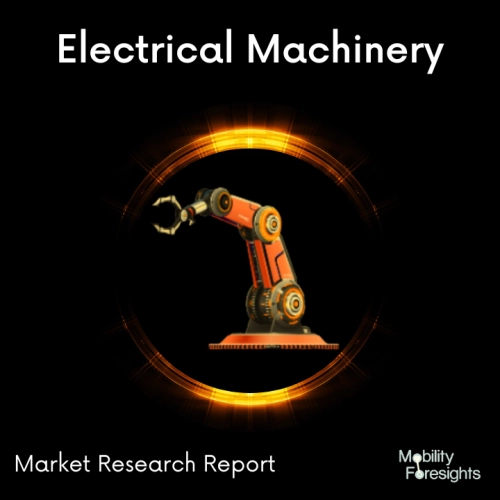
- Get in Touch with Us
Last Updated: Apr 25, 2025 | Study Period: 2024-2030
One sort of surface finish deposition technique used in CNC electroless plating machines is electronic packaging is electroless plating. The industry is moving toward this approach because of its benefits as a result of improvements in electronic devices.
The electroless plating procedure is unstable, though. Its stability is entirely dependent on the substrate type, pretreatment method, solution type, pH, and temperature conditions, as well as the plating procedure. The three forms of electroless plating formulas utilized in electronic packaging that have been investigated by prior researchers are electroless gold, electroless palladium, and electroless nickel.
Pd membrane production has frequently utilized electroless plating. Reference provides an excellent summary of the present stage of progress and pertinent references.
Electroless deposition is so common because it is inexpensive, has simple operations, and uses basic equipment. It is not necessary for supports to be conductive, and even complicated geometries can have uniform coverage.
However, the deposition of metal alloys is difficult. In order to create a Pd alloy, the two metals are typically placed one after the other and then heated to high temperatures. To deposit active Pd seeds on the surface, supports must first be activated by consecutive immersion in SnCl2 and PdCl2 solutions.
The Global CNC electroless plating machine market accounted for $XX Billion in 2023 and is anticipated to reach $XX Billion by 2030, registering a CAGR of XX% from 2024 to 2030.
Using a fully autonomous, closed galvanic system, The Holzapfel Group (Sinn, Germany) has created a novel high-speed CNC electroless plating machine for addressing customer-specific component plating requirements.
The coatings are made to be applied precisely, within very small tolerances, and with great reproducibility to each individual component.high-grade plating using item-specific anodesAnodes or reactor cells customised to each individual component are used in the electroplating process
The consistent process parameters are intended to guarantee extremely reproducible plating outcomes, that is, an unusually uniform, precisely repeatable distribution of coating thickness and, consequently, high-quality surface finishes.
Sl no | Topic |
1 | Market Segmentation |
2 | Scope of the report |
3 | Abbreviations |
4 | Research Methodology |
5 | Executive Summary |
6 | Introduction |
7 | Insights from Industry stakeholders |
8 | Cost breakdown of Product by sub-components and average profit margin |
9 | Disruptive innovation in the Industry |
10 | Technology trends in the Industry |
11 | Consumer trends in the industry |
12 | Recent Production Milestones |
13 | Component Manufacturing in US, EU and China |
14 | COVID-19 impact on overall market |
15 | COVID-19 impact on Production of components |
16 | COVID-19 impact on Point of sale |
17 | Market Segmentation, Dynamics and Forecast by Geography, 2024-2030 |
18 | Market Segmentation, Dynamics and Forecast by Product Type, 2024-2030 |
19 | Market Segmentation, Dynamics and Forecast by Application, 2024-2030 |
20 | Market Segmentation, Dynamics and Forecast by End use, 2024-2030 |
21 | Product installation rate by OEM, 2023 |
22 | Incline/Decline in Average B-2-B selling price in past 5 years |
23 | Competition from substitute products |
24 | Gross margin and average profitability of suppliers |
25 | New product development in past 12 months |
26 | M&A in past 12 months |
27 | Growth strategy of leading players |
28 | Market share of vendors, 2023 |
29 | Company Profiles |
30 | Unmet needs and opportunity for new suppliers |
31 | Conclusion |
32 | Appendix |