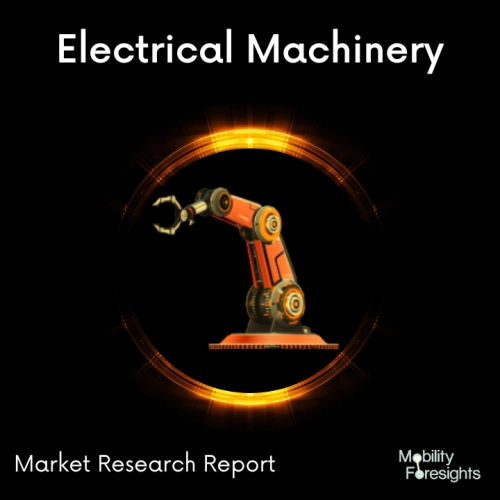
- Get in Touch with Us
Last Updated: Apr 25, 2025 | Study Period: 2023-2030
CNC Gas tungsten arc welding machine (GTAWM), also known as tungsten inert gas (TIG) welding machine, is an arc welding process that uses a non-consumable tungsten electrode to produce the weld.
The weld area and electrode are protected from oxidation or other atmospheric contamination by an inert shielding gas (argon or helium). A filler metal is normally used, though some welds, known as autogenous welds, or fusion welds do not require it. When helium is used, this is known as heliarc welding.
A constant-current welding power supply produces electrical energy, which is conducted across the arc through a column of highly ionized gas and metal vapors known as a plasma. TIG welding is most commonly used to weld thin sections of stainless steel and non-ferrous metals .
The process grants the operator greater control over the weld than competing processes such as shielded metal arc welding and gas metal arc welding, allowing for stronger, higher quality welds.
However, TIG welding is comparatively more complex and difficult to master, and furthermore, it is significantly slower than most other welding techniques.
A related process, plasma arc welding, uses a slightly different welding torch to create a more focused welding arc and as a result is often automated.
The Global CNC gas tungsten arc welding machine market accounted for $XX Billion in 2022 and is anticipated to reach $XX Billion by 2030, registering a CAGR of XX% from 2023 to 2030.
AMI, an ESAB brand, has collaborated with Wolfram Industrie, a vertically integrated manufacturer of premium tungsten and molybdenum materials, to offer an exclusive line of CNC gas tungsten arc welding machines.
The AMI-Wolfram Industrie ORBISTAR series of pre-ground tungsten electrodes can last more than two times longer than other tungstens and reduce arc fault failures by up to 80 percent.
The company offers different combinations of tungsten length, diameter, point geometry, surface finish, and type, including thoriated and non-thoriated options, to meet specific application requirements.
ORBISTAR electrodes provide superior arc stability and arc starting performance because of greater element purity, tighter control of grain size, more homogenous oxide distribution, and strict manufacturing process controls.
Sl no | Topic |
1 | Market Segmentation |
2 | Scope of the report |
3 | Abbreviations |
4 | Research Methodology |
5 | Executive Summary |
6 | Introduction |
7 | Insights from Industry stakeholders |
8 | Cost breakdown of Product by sub-components and average profit margin |
9 | Disruptive innovation in the Industry |
10 | Technology trends in the Industry |
11 | Consumer trends in the industry |
12 | Recent Production Milestones |
13 | Component Manufacturing in US, EU and China |
14 | COVID-19 impact on overall market |
15 | COVID-19 impact on Production of components |
16 | COVID-19 impact on Point of sale |
17 | Market Segmentation, Dynamics and Forecast by Geography, 2023-2030 |
18 | Market Segmentation, Dynamics and Forecast by Product Type, 2023-2030 |
19 | Market Segmentation, Dynamics and Forecast by Application, 2023-2030 |
20 | Market Segmentation, Dynamics and Forecast by End use, 2023-2030 |
21 | Product installation rate by OEM, 2023 |
22 | Incline/Decline in Average B-2-B selling price in past 5 years |
23 | Competition from substitute products |
24 | Gross margin and average profitability of suppliers |
25 | New product development in past 12 months |
26 | M&A in past 12 months |
27 | Growth strategy of leading players |
28 | Market share of vendors, 2023 |
29 | Company Profiles |
30 | Unmet needs and opportunity for new suppliers |
31 | Conclusion |
32 | Appendix |