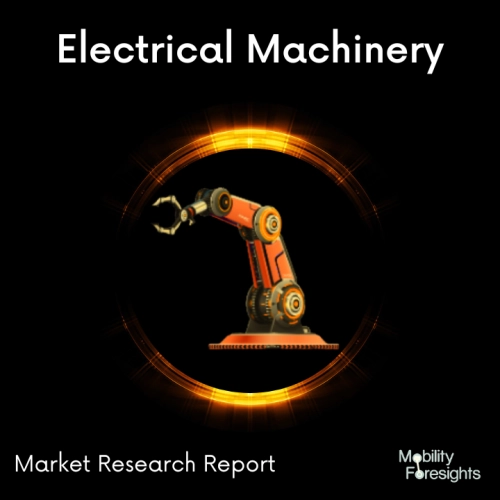
- Get in Touch with Us
Last Updated: Apr 25, 2025 | Study Period: 2024-2030
Most frequently used on smaller cylindrical gears up to about 5 mm, chamfer-rolling is an incredibly quick and adaptable method that removes burrs created by an earlier soft gear cutting operation.
To prevent harming the gears and bearings: Burrs may chip off during the operating cycle and harm other gears and bearings if they are not removed. preventing short tool lives during finishing operations.
Chamfering facilitates assembly, such as when installing nuts or bolts into holes. Additionally, chamfering eliminates sharp edges, greatly reducing the risk of cuts and injury to those handling the metal item.
The size of the machined surface can be easily measured and inspected with chamfer gauges, a measurement gauge.
Global CNC gear chamfering machine market accounted for $XX Billion in 2023 and is anticipated to reach $XX Billion by 2030, registering a CAGR of XX% from 2024 to 2030.
Helios Gear Products is pleased to introduce the Tecnomacchine ("TM") series of gear deburring and chamfering machines' most recent technological advancement.
In order to provide manufacturers with a higher level of repeatability, programmability, and usability, Helios now provides the TM 1000 platform with complete CNC.
The TM 1000-CNC represents the next stage in the development of our deburring platforms, according to Adam Gimpert, president of Helios.
Gear manufacturers require this CNC technology to reduce labour costs associated with deburring, boost repeatability, and minimise entry barriers for new operators and setup staff.
With a maximum face width of 1,000 mm, the TM 1000-CNC can deburr and chamfer items up to 1,000 mm (39.37 in) in diameter (39.37 in).
Before the totally enclosed machine uses 8 CNC axes for programmable placement (axial, radial, tangential, and inclination) of two tool spindles, an optical sensor locates each workpiece for the best deburring (top and bottom operations).
Tool spindles with speeds up to 30,000 rpm are used on the TM 1000 platform for effective deburring. For the purpose of removing coarse burrs prior to final deburring, the machine additionally features an optional pre-deburring station.
After a brief setup and one-time CNC programming, the machine deburrs top and bottom unattended with dependable quality.
The TM 1000-CNC allows for consistent, repeatable deburring and chamfering quality, and the equipment helps shops to recover expensive manual deburring time.
Sl no | Topic |
1 | Market Segmentation |
2 | Scope of the report |
3 | Abbreviations |
4 | Research Methodology |
5 | Executive Summary |
6 | Introduction |
7 | Insights from Industry stakeholders |
8 | Cost breakdown of Product by sub-components and average profit margin |
9 | Disruptive innovation in the Industry |
10 | Technology trends in the Industry |
11 | Consumer trends in the industry |
12 | Recent Production Milestones |
13 | Component Manufacturing in US, EU and China |
14 | COVID-19 impact on overall market |
15 | COVID-19 impact on Production of components |
16 | COVID-19 impact on Point of sale |
17 | Market Segmentation, Dynamics and Forecast by Geography, 2024-2030 |
18 | Market Segmentation, Dynamics and Forecast by Product Type, 2024-2030 |
19 | Market Segmentation, Dynamics and Forecast by Application, 2024-2030 |
20 | Market Segmentation, Dynamics and Forecast by End use, 2024-2030 |
21 | Product installation rate by OEM, 2023 |
22 | Incline/Decline in Average B-2-B selling price in past 5 years |
23 | Competition from substitute products |
24 | Gross margin and average profitability of suppliers |
25 | New product development in past 12 months |
26 | M&A in past 12 months |
27 | Growth strategy of leading players |
28 | Market share of vendors, 2023 |
29 | Company Profiles |
30 | Unmet needs and opportunity for new suppliers |
31 | Conclusion |
32 | Appendix |