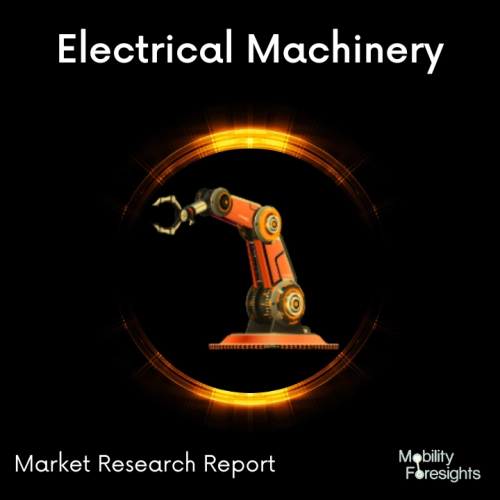
- Get in Touch with Us
Last Updated: Apr 25, 2025 | Study Period: 2023-2030
In the process of CNC machining, factory equipment and tools are moved in accordance with pre-programmed computer software. By doing away with the limitations of human control and producing high-quality output, CNC stands for computer numerical control.
Pouring a liquid metal into a hollow ceramic mould is called investment casting. The molten metal is removed from the cavity of the mould when it has cooled and solidified. The investment casting process is special and produces a better surface polish than other casting procedures because of the steps up until the metal is poured.
The Global CNC investment casting machine market accounted for $XX Billion in 2022 and is anticipated to reach $XX Billion by 2030, registering a CAGR of XX% from 2023 to 2030.
An affordable substitute for CNC machining, die and investment casting, and sand casting with machining has been developed: the quick casting method. Permanent graphite moulds are used in the process to create parts from the zinc-aluminium alloy ZA-12.
It typically takes four to six weeks from the completion of the CAD design to the first article samples. This technology offers OEMs and moulders a feasible substitute for die casting, which has a high cost per part, and machining parts from blanks (relatively low per-part cost but high up-front cost to machine the steel moulds).
Additionally, it's critical for the mould maker to stay current with emerging technologies that can enhance the production process as a whole and enable them to provide better customer service.
For the production of very precise components for electromechanical and electro-optical applications, Graphicast, Inc recommends using its ZA-12 casting method.
ZA-12 alloy, which has a density close to that of cast iron, is more durable than aluminium or bronze and tougher, stronger, and more robust. It is easier to machine than cast iron or aluminium and is comparable to brass or bronze in terms of ease.
With essential dimension tolerances of.003 inches per inch for the first inch and.001 inches per inch for successive inches, and surface finishes better than 125 microinches, it is usually possible to create graphite mould castings in large quantities.
Sl no | Topic |
1 | Market Segmentation |
2 | Scope of the report |
3 | Abbreviations |
4 | Research Methodology |
5 | Executive Summary |
6 | Introduction |
7 | Insights from Industry stakeholders |
8 | Cost breakdown of Product by sub-components and average profit margin |
9 | Disruptive innovation in the Industry |
10 | Technology trends in the Industry |
11 | Consumer trends in the industry |
12 | Recent Production Milestones |
13 | Component Manufacturing in US, EU and China |
14 | COVID-19 impact on overall market |
15 | COVID-19 impact on Production of components |
16 | COVID-19 impact on Point of sale |
17 | Market Segmentation, Dynamics and Forecast by Geography, 2023-2030 |
18 | Market Segmentation, Dynamics and Forecast by Product Type, 2023-2030 |
19 | Market Segmentation, Dynamics and Forecast by Application, 2023-2030 |
20 | Market Segmentation, Dynamics and Forecast by End use, 2023-2030 |
21 | Product installation rate by OEM, 2023 |
22 | Incline/Decline in Average B-2-B selling price in past 5 years |
23 | Competition from substitute products |
24 | Gross margin and average profitability of suppliers |
25 | New product development in past 12 months |
26 | M&A in past 12 months |
27 | Growth strategy of leading players |
28 | Market share of vendors, 2023 |
29 | Company Profiles |
30 | Unmet needs and opportunity for new suppliers |
31 | Conclusion |
32 | Appendix |