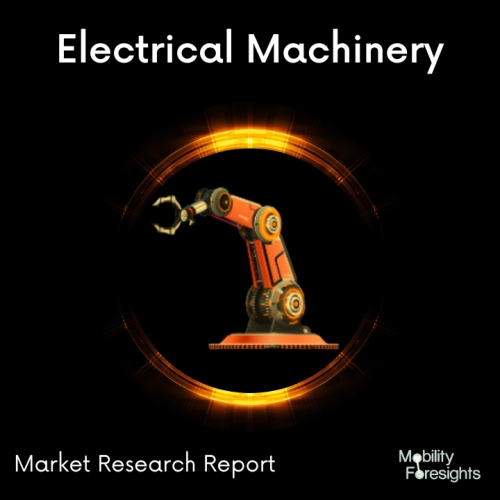
- Get in Touch with Us
Last Updated: Apr 25, 2025 | Study Period: 2024-2030
CNC non-destructive testing machines are advanced automated systems that use computer numerical control (CNC) to inspect the integrity of materials and components without damaging them. They are commonly used in a variety of industries, including aerospace, automotive, and petrochemical, to ensure a productâs reliability and safety.
In a typical non-destructive testing process, a CNC machine is programmed with a specific set of instructions regarding the type of inspection required.
Depending on the type of inspection, the machine may be used to measure, detect, or analyze the surface of a material or component. It can then compare the results to a predetermined standard to determine if the material or component is safe to use.
CNC non-destructive testing machines are highly accurate and efficient, and can be used to detect a wide range of problems. For example, they can detect cracks, porosity, corrosion, and other irregularities that could affect the performance and safety of a product. These machines can also be used to inspect welds for defects and to detect hidden objects within a material.
CNC non-destructive testing machines are versatile and can be used in a variety of applications. They are widely used to inspect complex components, such as aircraft parts, medical implants, and oil and gas pipelines. They are also used to inspect materials for the mining and construction industries.
The use of CNC non-destructive testing machines has revolutionized the quality control process and allowed companies to reduce costs and improve safety. By automating the inspection process, companies can ensure that their products meet industry standards and avoid costly rework or product recalls.
The Global CNC non-destructive testing machine market accounted for $XX Billion in 2023 and is anticipated to reach $XX Billion by 2030, registering a CAGR of XX% from 2024 to 2030.
Olympus Corporation is a leading manufacturer of CNC non-destructive testing machines. Olympus Corporation announced the launch of a new CNC non-destructive testing machine, the OLYMPUS VantaTM X-ray Fluorescence (XRF) Analyzer. This machine is designed to provide fast, accurate, and reliable measurements of a variety of elements in various materials.
The XRF Analyzer uses a unique and powerful combination of X-ray Fluorescence (XRF) and digital imaging technologies to detect and measure the presence of elements in materials. It is ideal for a wide range of applications, including the detection and characterization of contaminants in metals, alloys, and polymers.
The machine is capable of analyzing a wide range of elements from aluminum to uranium, with extremely low detection limits. The OLYMPUS Vanta XRF Analyzer is designed to provide reliable and repeatable results, enabling users to maximize their efficiency and accuracy in their analysis of materials.
GE Inspection Technologies is a leading provider of CNC non-destructive testing machines and services.GE Inspection Technologies announced the launch of the new GE Inspection Technologies SonoXRT digital radiography system. This machine is designed to provide fast and accurate imaging and analysis of a wide range of materials, from metals and alloys to plastics and composites.
The SonoXRT digital radiography system uses a high-resolution digital detector that is capable of detecting small features and defects in materials. The system features advanced imaging and analysis software that can be used to quickly and accurately identify and measure defects in materials.
The SonoXRT digital radiography system is designed to provide reliable and repeatable results that enable users to maximize their efficiency and accuracy in their analysis of materials.
Sl no | Topic |
1 | Market Segmentation |
2 | Scope of the report |
3 | Abbreviations |
4 | Research Methodology |
5 | Executive Summary |
6 | Introdauction |
7 | Insights from Industry stakeholders |
8 | Cost breakdown of Product by sub-components and average profit margin |
9 | Disruptive innovation in theIndustry |
10 | Technology trends in the Industry |
11 | Consumer trends in the industry |
12 | Recent Production Milestones |
13 | Component Manufacturing in US, EU and China |
14 | COVID-19 impact on overall market |
15 | COVID-19 impact on Production of components |
16 | COVID-19 impact on Point of sale |
17 | Market Segmentation, Dynamics and Forecast by Geography, 2024-2030 |
18 | Market Segmentation, Dynamics and Forecast by Product Type, 2024-2030 |
19 | Market Segmentation, Dynamics and Forecast by Application, 2024-2030 |
20 | Market Segmentation, Dynamics and Forecast by End use, 2024-2030 |
21 | Product installation rate by OEM, 2023 |
22 | Incline/Decline in Average B-2-B selling price in past 5 years |
23 | Competition from substitute products |
24 | Gross margin and average profitability of suppliers |
25 | New product development in past 12 months |
26 | M&A in past 12 months |
27 | Growth strategy of leading players |
28 | Market share of vendors, 2023 |
29 | Company Profiles |
30 | Unmet needs and opportunity for new suppliers |
31 | Conclusion |
32 | Appendix |