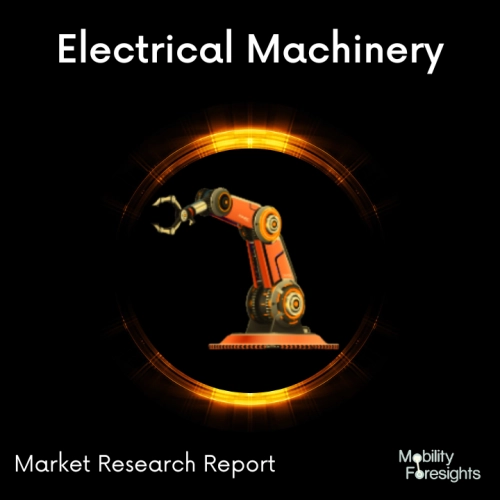
- Get in Touch with Us
Last Updated: Apr 25, 2025 | Study Period: 2024-2030
CNC projection welding machine uses Resistance welding techniques like projection welding that use pressure and electrical current to unite metal components that are intended to come into contact with one another at one or more key locations.
This enables stronger welds while using less energy during welding This form of weld can attach a nut, threaded stud, or protrusion to an assembly in addition to joining two pieces of steel together.
To guarantee that the component parts fit properly and maximum contact between the components during projection welding, the pieces must be specifically made with dimples or projections.
The intended use of the material and component informs the welding technique. At one point of contact, the welder uses the welding machine to transmit force and electricity.
The material and processing requirements will influence the pressure, current strength, and duration of the current application.
Over more conventional welding techniques, projection welding has a number of advantages, including:a rise in output. The method increases industrial output by enabling the completion of many welds and simultaneously prolonged lifespan.
The Global CNC projection welding machine market accounted for $XX Billion in 2023 and is anticipated to reach $XX Billion by 2030, registering a CAGR of XX% from 2024 to 2030.
With models ranging in power from 500 to 40,000 watts seconds/joules, Artech caters to a wide range of applications. Artech has created more than 100 custom CNC Projection welding machines in addition to conventional machines to meet the demands of varied applications.
Artech's application engineering and projection welder team takes full responsibility for assisting you in easily adjusting CNC Projection Welding using a tried-and-true methodology and profound understanding in joining technology.
Artech's long-standing relationships with its clients attest to its collaborative mindset. compact, comfortable designs, digital controls based on microcontrollers, programs for setting up welds for various jobs, Change weld parameters with password protection, monitoring of each weld's quality (peak current, peak time, RMS current and half-peak time),Weld counter overall (no-reset),Countdown timer with reset/preset
Sl no | Topic |
1 | Market Segmentation |
2 | Scope of the report |
3 | Abbreviations |
4 | Research Methodology |
5 | Executive Summary |
6 | Introduction |
7 | Insights from Industry stakeholders |
8 | Cost breakdown of Product by sub-components and average profit margin |
9 | Disruptive innovation in the Industry |
10 | Technology trends in the Industry |
11 | Consumer trends in the industry |
12 | Recent Production Milestones |
13 | Component Manufacturing in US, EU and China |
14 | COVID-19 impact on overall market |
15 | COVID-19 impact on Production of components |
16 | COVID-19 impact on Point of sale |
17 | Market Segmentation, Dynamics and Forecast by Geography, 2024-2030 |
18 | Market Segmentation, Dynamics and Forecast by Product Type, 2024-2030 |
19 | Market Segmentation, Dynamics and Forecast by Application, 2024-2030 |
20 | Market Segmentation, Dynamics and Forecast by End use, 2024-2030 |
21 | Product installation rate by OEM, 2023 |
22 | Incline/Decline in Average B-2-B selling price in past 5 years |
23 | Competition from substitute products |
24 | Gross margin and average profitability of suppliers |
25 | New product development in past 12 months |
26 | M&A in past 12 months |
27 | Growth strategy of leading players |
28 | Market share of vendors, 2023 |
29 | Company Profiles |
30 | Unmet needs and opportunity for new suppliers |
31 | Conclusion |
32 | Appendix |