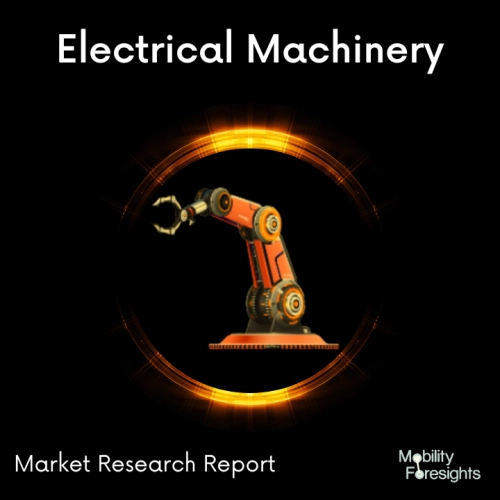
- Get in Touch with Us
Last Updated: Apr 25, 2025 | Study Period: 2024-2030
One of the earliest methods of joining two or more sheets of metal together is spot welding, a type of resistance welding in which no filler material is used.
Using CNC spot welding machineâs shaped alloy copper electrodes that conduct an electrical current through the weld pieces, the procedure entails applying pressure and heat to the weld region.
When the material melts and fuses the components together, the current is cut off, the electrodes' pressure is maintained, and the liquid "nugget" solidifies to create the joint.
Electric current, which is transmitted to the workpiece through copper alloy electrodes, produces the welding heat.
Since copper has a higher thermal conductivity and lower electrical resistance than the majority of other metals, it is utilized for the electrodes, ensuring that heat is generated preferentially in the work pieces rather than the electrodes.
The Global CNC spot welding machine market accounted for $XX Billion in 2023 and is anticipated to reach $XX Billion by 2030, registering a CAGR of XX% from 2024 to 2030.
In order to achieve automatic welding,PROFISPOT-CNCCNC spot welding machine uses a single-head long-arm type row welding structure, workpiece molds that move along the X and Y axes, and inputs coordinate data for the welding position, welding current, and other data.
It is only necessary to manually position the material and remove the workpiece, and the mesh may be welded up to a size of 1000mm by 1000mm.
Design Principle:designed with a body made of strengthened special steel and a gantry-style construction.All-digital control, self-developed intelligent microcomputer quick reaction touch controller, and a straightforward user interface. HMI may be quickly and easily learned.
(human-Machine-Interface)utilizing a premium double-layer cylinder as the pressured source and a premium imported electromagnetic The CNC X-Y table makes it possible to quickly position flat material. The CNC-controlled axes are located at the back and one side of the table, giving you a working corner.
By enabling exact placement and accurate repeatability, this technology offers a considerable advantage over marking and manually locating material, potentially leading to a large decrease in the cost per part.
Sl no | Topic |
1 | Market Segmentation |
2 | Scope of the report |
3 | Abbreviations |
4 | Research Methodology |
5 | Executive Summary |
6 | Introduction |
7 | Insights from Industry stakeholders |
8 | Cost breakdown of Product by sub-components and average profit margin |
9 | Disruptive innovation in the Industry |
10 | Technology trends in the Industry |
11 | Consumer trends in the industry |
12 | Recent Production Milestones |
13 | Component Manufacturing in US, EU and China |
14 | COVID-19 impact on overall market |
15 | COVID-19 impact on Production of components |
16 | COVID-19 impact on Point of sale |
17 | Market Segmentation, Dynamics and Forecast by Geography, 2024-2030 |
18 | Market Segmentation, Dynamics and Forecast by Product Type, 2024-2030 |
19 | Market Segmentation, Dynamics and Forecast by Application, 2024-2030 |
20 | Market Segmentation, Dynamics and Forecast by End use, 2024-2030 |
21 | Product installation rate by OEM, 2023 |
22 | Incline/Decline in Average B-2-B selling price in past 5 years |
23 | Competition from substitute products |
24 | Gross margin and average profitability of suppliers |
25 | New product development in past 12 months |
26 | M&A in past 12 months |
27 | Growth strategy of leading players |
28 | Market share of vendors, 2023 |
29 | Company Profiles |
30 | Unmet needs and opportunity for new suppliers |
31 | Conclusion |
32 | Appendix |