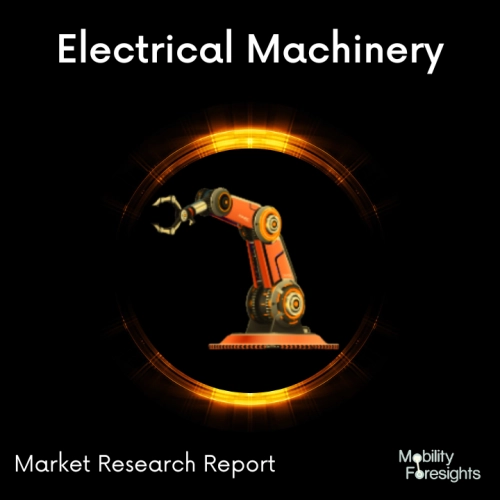
- Get in Touch with Us
Last Updated: Apr 25, 2025 | Study Period: 2024-2030
CNC machines enable thermoforming technology to produce high-quality plastic parts with lightning-fast turnaround. Their team can process hard polymers as well as other materials including wood, composites, and aluminium thanks to a powerful oscillating knife system, which is the essential mechanism.
The CNC machine can also cut through EPS, corrugated cardboard, rubber, cork, felt, wood, and leather in addition to X-Board, graphic foam board, and other types of foam board used as gaskets.
The Global CNC thermoforming machine market accounted for $XX Billion in 2023 and is anticipated to reach $XX Billion by 2030, registering a CAGR of XX% from 2024 to 2030.
In the product development process, machining prototype molds is the initial use for their 5-Axis CNC machines. Therma formers can be divided into two groups: thin gauge and thick gauge. Thick gauge thermoforming is done by Reliable Formed Plastics.
For the manufacture of the initial molds, they commonly use MDF (medium-density fiberboard). MDF is a less expensive option to the more expensive epoxy board, despite the fact that it is only effective for a relatively short run in vacuum thermoforming because it can deteriorate over longer runs.
As a result, by using MDF at the mold prototype stage, they may make changes to the mold and reduce the cost to the client before utilizing the more expensive production run tooling.
For forming plastics, there are numerous methods that can be used. Blow molding, rotational molding, injection molding, and thermoforming are a few of them. Due to the affordable price of molds and tools, thermoforming is frequently the preferred method, particularly for big parts and prototyping.
When thermoforming, a plastic sheet is heated to a temperature that makes it malleable, stretched over the surface of a mold, and the air between the plastic and the mold is removed using a vacuum.
By doing this, a plastic shell is produced whose surface corresponds to the mold's shape. After being cooled to a solid state, the formed sheet is cut into a useful plastic product. With a 2â²â3â² draw, Reliable Formed Plastics can form sheets up to 6'x12' in size.
Sl no | Topic |
1 | Market Segmentation |
2 | Scope of the report |
3 | Abbreviations |
4 | Research Methodology |
5 | Executive Summary |
6 | Introduction |
7 | Insights from Industry stakeholders |
8 | Cost breakdown of Product by sub-components and average profit margin |
9 | Disruptive innovation in the Industry |
10 | Technology trends in the Industry |
11 | Consumer trends in the industry |
12 | Recent Production Milestones |
13 | Component Manufacturing in US, EU and China |
14 | COVID-19 impact on overall market |
15 | COVID-19 impact on Production of components |
16 | COVID-19 impact on Point of sale |
17 | Market Segmentation, Dynamics and Forecast by Geography, 2024-2030 |
18 | Market Segmentation, Dynamics and Forecast by Product Type, 2024-2030 |
19 | Market Segmentation, Dynamics and Forecast by Application, 2024-2030 |
20 | Market Segmentation, Dynamics and Forecast by End use, 2024-2030 |
21 | Product installation rate by OEM, 2023 |
22 | Incline/Decline in Average B-2-B selling price in past 5 years |
23 | Competition from substitute products |
24 | Gross margin and average profitability of suppliers |
25 | New product development in past 12 months |
26 | M&A in past 12 months |
27 | Growth strategy of leading players |
28 | Market share of vendors, 2023 |
29 | Company Profiles |
30 | Unmet needs and opportunity for new suppliers |
31 | Conclusion |
32 | Appendix |