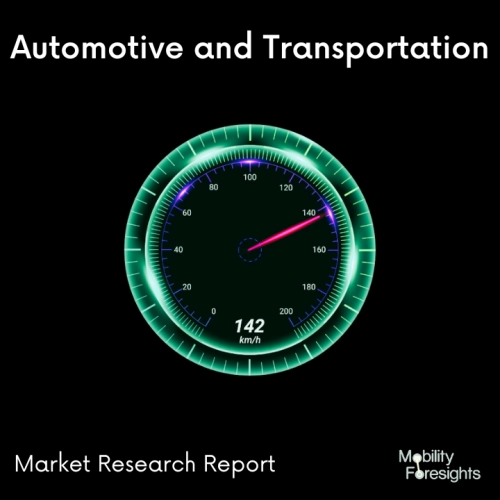
- Get in Touch with Us
Last Updated: Apr 25, 2025 | Study Period: 2023-2030
INTRODUCTION
Many contemporary cars have a structural element called the cockpit cross-car beam. It normally sits behind the dashboard, close to the bottom of the windscreen. The cockpit cross-car beam's main purpose is to give the car's passenger area more rigidity and strength, which helps to protect the occupants in the case of a collision.
The cockpit cross-car beam may store different parts including airbags, sensors, and other safety measures in addition to serving as structural support. By aiding in the dampening and absorption of vibrations, it may also contribute to the reduction of noise, vibration, and harshness (NVH).
The make, model, and specific safety and NVH criteria of the manufacturer can all affect the design and construction of cockpit cross-car beams. To attain the desired performance qualities, certain beams may be built of steel or aluminium, while others may use composite materials or other cutting-edge materials.
Overall, the cockpit cross-car beam is a crucial safety feature in contemporary cars that helps to save occupants in the case of a collision while also enhancing comfort and driving pleasure.
GLOBAL COCKPIT CROSS-CAR BEAM MARKET SIZE AND FORECAST
Global Cockpit cross-car beam market accounted for $XX Billion in 2022 and is anticipated to reach $XX Billion by 2030, registering a CAGR of XX% from 2023 to 2030.
NEW PRODUCT LAUNCH
The lightweight cockpit cross-car beams for the Tesla Model 3 are currently supplied by the German company ElringKlinger. The company recently received a new order "for series supply of cockpit cross-car beams in hybrid design for new model of a leading US electric vehicle manufacturer."
This, along with the production starting in 2020 (the contract is for a five-year period), and the Fremont production facility, strongly supports Model Y.
ElringKlinger creates lightweight plastic components for automobile bodies using an inventive manufacturing technique that combines hydroforming and injection moulding in a single stage.
The resulting hybrid components constructed of plastic and metal combine the benefits of both materials, providing significant structural strength in the case of a crash and great dimensional accuracy of complex designs with minimal tolerances. In addition, there are noticeable weight advantages over traditional metal variants.
Cooperation between ElringKlinger AG and a major American electric vehicle manufacturer is growing. The global US electric vehicle pioneer has entered into a series agreement with the Dettingen-based supplier to supply cockpit cross-car beams for its new full-electric model on the basis of their prior commercial connection with lightweighting components.
The order has a total volume in the mid- to high-double-digit million euro range and will initially last for five years. The Californian facility in Fremont, USA, is set to begin production.
COMPANY PROFILE
THIS REPORT WILL ANSWER FOLLOWING QUESTIONS
Sl no | Topic |
1 | Market Segmentation |
2 | Scope of the report |
3 | Abbreviations |
4 | Research Methodology |
5 | Executive Summary |
6 | Introduction |
7 | Insights from Industry stakeholders |
8 | Cost breakdown of Product by sub-components and average profit margin |
9 | Disruptive innovation in the Industry |
10 | Technology trends in the Industry |
11 | Consumer trends in the industry |
12 | Recent Production Milestones |
13 | Component Manufacturing in US, EU and China |
14 | COVID-19 impact on overall market |
15 | COVID-19 impact on Production of components |
16 | COVID-19 impact on Point of sale |
17 | Market Segmentation, Dynamics and Forecast by Geography, 2023-2030 |
18 | Market Segmentation, Dynamics and Forecast by Product Type, 2023-2030 |
19 | Market Segmentation, Dynamics and Forecast by Application, 2023-2030 |
20 | Market Segmentation, Dynamics and Forecast by End use, 2023-2030 |
21 | Product installation rate by OEM, 2023 |
22 | Incline/Decline in Average B-2-B selling price in past 5 years |
23 | Competition from substitute products |
24 | Gross margin and average profitability of suppliers |
25 | New product development in past 12 months |
26 | M&A in past 12 months |
27 | Growth strategy of leading players |
28 | Market share of vendors, 2023 |
29 | Company Profiles |
30 | Unmet needs and opportunity for new suppliers |
31 | Conclusion |
32 | Appendix |