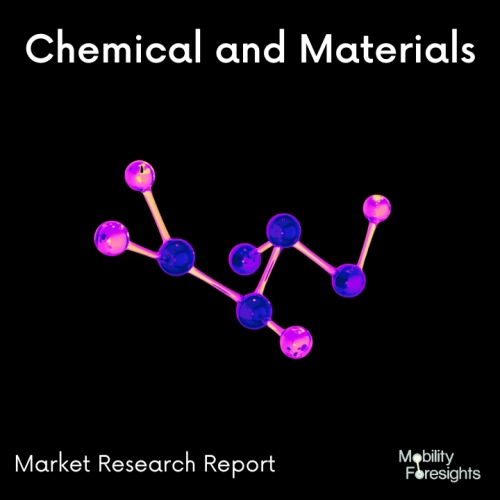
- Get in Touch with Us
Last Updated: Apr 25, 2025 | Study Period: 2024-2030
Metals with a high melting point, like aluminium, are best suited for cold-chamber die casting. This procedure involves ladling metal that has been liquefied at extremely high temperatures in a furnace into a cold chamber so that it may be injected into the die. Metals with a high melting point, like aluminium, are best suited for cold-chamber die casting.
This procedure involves ladling metal that has been liquefied at extremely high temperatures in a furnace into a cold chamber so that it may be injected into the die. In the manufacturing process known as die casting, molten metal is pressed or poured into steel moulds.
The moulds, which are often referred to as tools or dies, are made of steel and are uniquely manufactured for each project. This makes it possible to generate each component using.
The Global Cold Chamber Die Casting Machine market accounted for $XX Billion in 2023 and is anticipated to reach $XX Billion by 2030, registering a CAGR of XX% from 2024 to 2030.
The operation of the cold chamber die casting technique involves the addition of molten aluminium alloy material into the die shot cell from a separate source. The cold box casting machine can function with a lower temperature process because molten aluminium is brought in from an outside source.
For each die shot or manufacturing cycle in the cold chamber die casting process, the molten or liquid metal material must be introduced. This feature could potentially have an impact on the production rate efficiency for high volume projects because it calls for molten metal on a regular cycle.
A higher pressure must also be used during the cold chamber process. In comparison to the pressure needed to operate hot chamber die casting, the high pressure at which the liquid material is forced into and expands in the die cavity is noticeably higher.
To fill the mould cavities during the cold chamber process, pressures ranging from 3,000 psi to 50,000 psi are frequently used during the manufacturing process. Thinner part walls, improved mechanical qualities, and highly detailed design are a few benefits of the cold chamber method of producing die cast parts.
The range of cold box machines is extensive at Die Castings China. The equipment we use to make some parts for the auto industry is demonstrated in the video down below.
Sl no | Topic |
1 | Market Segmentation |
2 | Scope of the report |
3 | Abbreviations |
4 | Research Methodology |
5 | Executive Summary |
6 | Introduction |
7 | Insights from Industry stakeholders |
8 | Cost breakdown of Product by sub-components and average profit margin |
9 | Disruptive innovation in the Industry |
10 | Technology trends in the Industry |
11 | Consumer trends in the industry |
12 | Recent Production Milestones |
13 | Component Manufacturing in US, EU and China |
14 | COVID-19 impact on overall market |
15 | COVID-19 impact on Production of components |
16 | COVID-19 impact on Point of sale |
17 | Market Segmentation, Dynamics and Forecast by Geography, 2024-2030 |
18 | Market Segmentation, Dynamics and Forecast by Product Type, 2024-2030 |
19 | Market Segmentation, Dynamics and Forecast by Application, 2024-2030 |
20 | Market Segmentation, Dynamics and Forecast by End use, 2024-2030 |
21 | Product installation rate by OEM, 2023 |
22 | Incline/Decline in Average B-2-B selling price in past 5 years |
23 | Competition from substitute products |
24 | Gross margin and average profitability of suppliers |
25 | New product development in past 12 months |
26 | M&A in past 12 months |
27 | Growth strategy of leading players |
28 | Market share of vendors, 2023 |
29 | Company Profiles |
30 | Unmet needs and opportunity for new suppliers |
31 | Conclusion |
32 | Appendix |