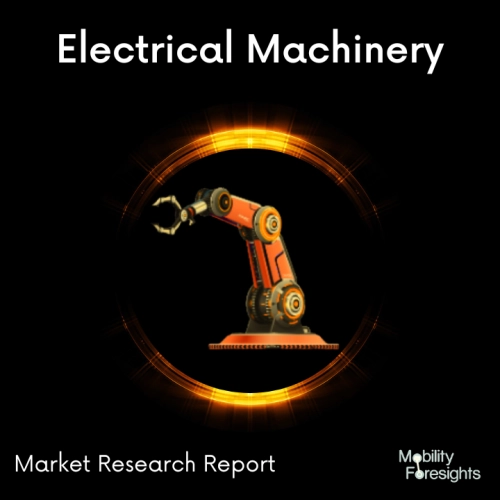
- Get in Touch with Us
Last Updated: Apr 25, 2025 | Study Period: 2023-2030
To use lessons learned from past mistakes to improve practises and activities moving forward; To hold both internal and external parties accountable for the resources used and the results attained; To make well-informed decisions about the initiative's future; To support the empowerment of the initiative's beneficiaries.
Monitoring enables the documentation of outcomes, procedures, and experiences for use as a foundation for decision-making and the learning process.
Monitoring involves comparing results to the plans. Evaluation is done using the information gathered via monitoring.
find underlying issues occasionally before they have a negative impact.Identify issues that have an impact on a user's productivity.
When an issue appears for the first time, gather data.Permit you to set a reference point for comparison.
Machine performance is monitored and reported to the system using condition monitoring sensors. These sensors are used to monitor wear, overheating, vibrations, and noise. The information gathered from these sensors is analysed and sent to the central system.
State monitoring (CM) is the act of keeping an eye on a certain machine condition (such as temperature, vibration, etc.) in order to spot any changes that could be signs of an impending failure.
Vibration analysis and vibration monitoring, oil analysis, and temperature tracking and measurement are examples of common condition-based monitoring techniques.
As we said above, some of the most popular kinds of condition-based monitoring take a look at temperature, vibration, and oil.
The Global Condition Monitoring Sensor market accounted for $XX Billion in 2022 and is anticipated to reach $XX Billion by 2030, registering a CAGR of XX% from 2023 to 2030.
New Wireless Condition Monitoring Sensor from SKF is unveiled.
For use in condition monitoring and equipment diagnostic applications, SKF has introduced a new wireless machine condition sensor that delivers dynamic vibration and temperature data.
With its ATEX Zone 0 accreditation, the SKF Wireless Machine Condition Sensor may be utilised in risky settings like those found in petrochemical, oil and gas, or pharmaceutical companies.
The gadget is a small, battery-powered instrument the size of a conventional industrial accelerometer that combines a sensor and a router node.
A mesh network is created by the sensors' communication with one another and a wireless gateway. For monitoring rotating equipment in big factories, in difficult-to-reach places, or in situations where conventional Wi-Fi connections won't function, this kind of network and communication protocol is suitable.
The WirelessHART gateway then connects with the included wireless sensor device manager software when data collection is complete.
A plant engineer may then automatically transfer the data from the device manager into a complete diagnostic and analytical software package for analysis.
With wired systems or handheld devices, monitoring capabilities may be unattainable, according to SKF's new wireless machine condition sensor. This may eventually result in lower condition monitoring expenses and a safer method of machine monitoring.
Sl no | Topic |
1 | Market Segmentation |
2 | Scope of the report |
3 | Abbreviations |
4 | Research Methodology |
5 | Executive Summary |
6 | Introduction |
7 | Insights from Industry stakeholders |
8 | Cost breakdown of Product by sub-components and average profit margin |
9 | Disruptive innovation in the Industry |
10 | Technology trends in the Industry |
11 | Consumer trends in the industry |
12 | Recent Production Milestones |
13 | Component Manufacturing in US, EU and China |
14 | COVID-19 impact on overall market |
15 | COVID-19 impact on Production of components |
16 | COVID-19 impact on Point of sale |
17 | Market Segmentation, Dynamics and Forecast by Geography, 2023-2030 |
18 | Market Segmentation, Dynamics and Forecast by Product Type, 2023-2030 |
19 | Market Segmentation, Dynamics and Forecast by Application, 2023-2030 |
20 | Market Segmentation, Dynamics and Forecast by End use, 2023-2030 |
21 | Product installation rate by OEM, 2023 |
22 | Incline/Decline in Average B-2-B selling price in past 5 years |
23 | Competition from substitute products |
24 | Gross margin and average profitability of suppliers |
25 | New product development in past 12 months |
26 | M&A in past 12 months |
27 | Growth strategy of leading players |
28 | Market share of vendors, 2023 |
29 | Company Profiles |
30 | Unmet needs and opportunity for new suppliers |
31 | Conclusion |
32 | Appendix |