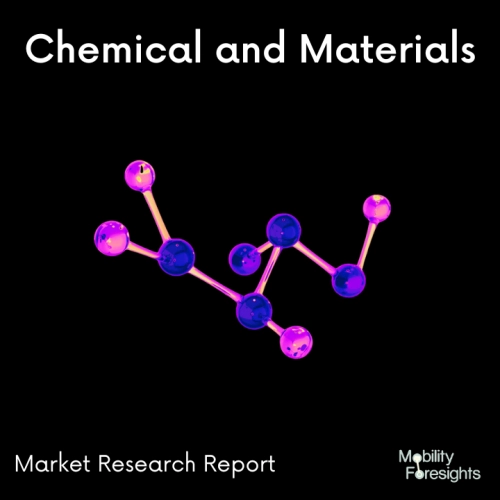
- Get in Touch with Us
Last Updated: Apr 26, 2025 | Study Period: 2024-2030
Copper-nickel alloys (Cu-Ni) are a family of alloys composed of copper and nickel which exhibit superior corrosion resistance, strength, and ductility compared to other alloys.
The composition of these alloys can vary, but typically contain anywhere from 5-35% nickel and the remainder copper. Cu-Ni alloys are known for their excellent formability, weldability, and machinability, making them ideal for a variety of industrial and commercial applications.
Cu-Ni alloys are commonly used in the production of pipes, tubes, and fittings for the transportation of chemical and corrosive liquids.
This is due to the high corrosion resistance of the alloys, which allows them to withstand the harsh chemical environment.
Additionally, Cu-Ni alloys are often used in the production of marine equipment such as propellers, pumps, and valves as they are resistant to saltwater corrosion.
Cu-Ni alloys are also frequently used in the production of electrical components such as circuit boards, wiring, and connectors.
Their superior electrical conductivity makes them ideal for these applications. Additionally, Cu-Ni alloys are often used in the automotive industry due to their strength and ductility. They can be used to create engine parts, exhaust systems, and fuel tanks.
Cu-Ni alloys are an incredibly versatile family of alloys and their broad range of applications makes them invaluable for many industries.
Their superior strength, ductility, and corrosion resistance make them the ideal choice for many applications.
The Global Copper-Nickel Alloys Market accounted for $XX Billion in 2022 and is anticipated to reach $XX Billion by 2030, registering a CAGR of XX% from 2024 to 2030.
Copper-nickel alloy is introduced by 3D Systems for use with Metal 3D printing. Up until 3D Systems, no business in the AM sector had been able to qualify copper-nickel for usage with metal 3D printing.
The industry leader in additive manufacturing presents a copper-nickel alloy that resists corrosion and may be used with laser powder bed fusion. The material, known as CuNi30, was created in partnership with HII's Newport News Shipbuilding branch and is already compatible with the company's DMP Flex 350 metal 3D printer.
HII is acknowledged globally as the biggest shipbuilder in America and a partner in defense and innovations across all domains. As a result of this partnership, Newport News Shipbuilding will be the first partner of 3D Systems to replace its conventional casting methods with additive manufacturing and CuNi30.
Since copper-nickel alloys have strong corrosion resistance and anti-microbial and anti-algae characteristics that prevent algae growth even after prolonged contact with water, they are widely employed in salt water, petroleum, and acidic environments. CuNi30 is frequently used in the production of valves and pipe fittings for the nuclear, chemical, and marine offshore oil and gas sectors.
The Molybdenum, Nickel, and Zinc Marks are being implemented in pilot form by the Copper Mark. Producers of these metals are able to demonstrate their leadership in sustainable and ethical production practices by achieving their respective "Mark" using the Copper Mark certification system.
The primary goal of the pilot program is to evaluate how well producers of nickel, zinc, and molybdenum can use the Copper Mark assurance framework. Its specific goals are to gain a greater understanding of how the multi-metal method is applied to both single and multi-metal manufacturers, as well as how much it helps participants satisfy impending market expectations and regulatory needs.
In order to promote sustainable and ethical production and sourcing practices within the value chains for copper, molybdenum, nickel, and zinc, the Copper Mark, the International Molybdenum Association (IMOA), the Nickel Institute (NI), and the International Zinc Association (IZA) have been working together to develop the pilot. The partnership utilizes current protocols and frameworks.
No new standards are being set by the four organizations. Any site that extracts, processes, treats, mixes, recycles, handles, or otherwise manipulates goods containing mined molybdenum, nickel, or zinc ore, metals, chemicals, alloys, or other materials is eligible to participate in the pilot program on a voluntary basis.
Sl no | Topic |
1 | Market Segmentation |
2 | Scope of the report |
3 | Abbreviations |
4 | Research Methodology |
5 | Executive Summary |
6 | Introduction |
7 | Insights from Industry stakeholders |
8 | Cost breakdown of Product by sub-components and average profit margin |
9 | Disruptive innovation in the Industry |
10 | Technology trends in the Industry |
11 | Consumer trends in the industry |
12 | Recent Production Milestones |
13 | Component Manufacturing in US, EU and China |
14 | COVID-19 impact on overall market |
15 | COVID-19 impact on Production of components |
16 | COVID-19 impact on Point of sale |
17 | Market Segmentation, Dynamics and Forecast by Geography, 2024-2030 |
18 | Market Segmentation, Dynamics and Forecast by Product Type, 2024-2030 |
19 | Market Segmentation, Dynamics and Forecast by Application, 2024-2030 |
20 | Market Segmentation, Dynamics and Forecast by End use, 2024-2030 |
21 | Product installation rate by OEM, 2023 |
22 | Incline/Decline in Average B-2-B selling price in past 5 years |
23 | Competition from substitute products |
24 | Gross margin and average profitability of suppliers |
25 | New product development in past 12 months |
26 | M&A in past 12 months |
27 | Growth strategy of leading players |
28 | Market share of vendors, 2023 |
29 | Company Profiles |
30 | Unmet needs and opportunity for new suppliers |
31 | Conclusion |
32 | Appendix |