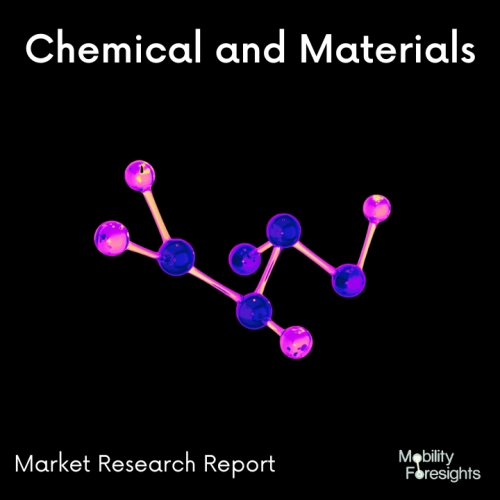
- Get in Touch with Us
Last Updated: Apr 25, 2025 | Study Period: 2024-2030
The weight of cables with corrugated aluminium sheaths (CAS), the initial lead substitution method used in the development of metallic shielding technology, is much lower than that of cables with lead alloy sheaths.
CAS cables, on the other hand, have the drawbacks of a bigger diameter and thus shorter delivery lengths, in addition to a decreased transmission capacity caused by the presence of an air gap under the corrugations.
The flawlessly welded aluminium sheath also ensures top-notch electrical and mechanical functionality, complete fluid tightness, and compliance with even the tightest environmental standards.
The Global Corrugated Aluminum Sheath Cable Market accounted for $XX Billion in 2022 and is anticipated to reach $XX Billion by 2030, registering a CAGR of XX% from 2024 to 2030.
In order to ensure the proper operation of a cable, the metallic sheath must fulfil crucial electrical and mechanical requirements.
This gives it a significant role in the design of high voltage underground cable networks. Cables with a lead alloy sheath, the original metallic shielding technology, offer the necessary technical assurances in terms of mechanical protection, fluid and moisture tightness, and short circuit current carrying capacity.
The main drawbacks of lead alloy-sheathed cables, however, are weight and, in some cases, fatigue strain. This is especially true when it comes to installation.
The weight of cables with corrugated aluminium sheaths (CAS), the initial lead substitution method used in the development of metallic shielding technology, is much lower than that of cables with lead alloy sheaths.
CAS cables, on the other hand, have the drawbacks of a bigger diameter and thus shorter delivery lengths, in addition to a decreased transmission capacity caused by the presence of an air gap under the corrugations.
The flawlessly welded aluminium sheath also ensures top-notch electrical and mechanical functionality, complete fluid tightness, and compliance with even the tightest environmental standards.
Sl no | Topic |
1 | Market Segmentation |
2 | Scope of the report |
3 | Abbreviations |
4 | Research Methodology |
5 | Executive Summary |
6 | Introduction |
7 | Insights from Industry stakeholders |
8 | Cost breakdown of Product by sub-components and average profit margin |
9 | Disruptive innovation in the Industry |
10 | Technology trends in the Industry |
11 | Consumer trends in the industry |
12 | Recent Production Milestones |
13 | Component Manufacturing in US, EU and China |
14 | COVID-19 impact on overall market |
15 | COVID-19 impact on Production of components |
16 | COVID-19 impact on Point of sale |
17 | Market Segmentation, Dynamics and Forecast by Geography, 2024-2030 |
18 | Market Segmentation, Dynamics and Forecast by Product Type, 2024-2030 |
19 | Market Segmentation, Dynamics and Forecast by Application, 2024-2030 |
20 | Market Segmentation, Dynamics and Forecast by End use, 2024-2030 |
21 | Product installation rate by OEM, 2023 |
22 | Incline/Decline in Average B-2-B selling price in past 5 years |
23 | Competition from substitute products |
24 | Gross margin and average profitability of suppliers |
25 | New product development in past 12 months |
26 | M&A in past 12 months |
27 | Growth strategy of leading players |
28 | Market share of vendors, 2023 |
29 | Company Profiles |
30 | Unmet needs and opportunity for new suppliers |
31 | Conclusion |
32 | Appendix |